In the realm of metallurgy, Monel, Inconel, and Hastelloy alloys occupy distinct niches, each offering a unique set of properties that cater to specific industrial applications. So, Monel vs Inconel vs Hastelloy Alloys: What’s the difference? In this article, we will try to answer that question in detail.
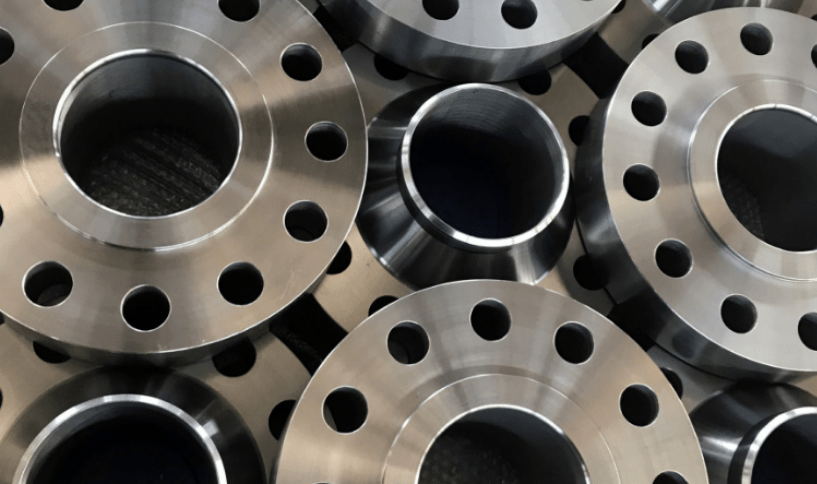
Monel vs Inconel vs Hastelloy Alloys: What’s the difference?
Let’s start with Monel. Monel, primarily a nickel–copper alloy, is renowned for its exceptional corrosion resistance. This alloy’s resilience against a wide range of corrosive environments, particularly marine settings and chemical processing plants, has made it a trusted material in these industries. Monel’s good mechanical properties, including high tensile strength and ductility, also contribute to its widespread use in structural applications. Furthermore, its weldability and formability allow for easy fabrication into complex shapes and components.
Now, turning our attention to Inconel, we find a nickel-chromium-based alloy with superior performance at high temperatures. Inconel alloys are known for their outstanding resistance to oxidation and corrosion at elevated temperatures, making them ideal for use in extreme environments such as jet engines, turbines, and other high-temperature applications. These alloys maintain their mechanical properties even at temperatures well above those that would cause other metals to soften or lose their strength.
Hastelloy alloys, on the other hand, are nickel-based alloys with molybdenum and other elements added to enhance corrosion resistance in the most demanding environments. These alloys are particularly suitable for handling highly corrosive acids and other chemicals. Hastelloy’s unique composition allows it to withstand even the most aggressive chemical attack, making it a preferred choice in chemical processing, petrochemical, and pulp and paper industries.
Comparing the three alloys, it becomes evident that each one excels in specific areas. Monel’s strength lies in its corrosion resistance and mechanical properties, making it a good choice for structural applications in corrosive environments. Inconel, on the other hand, shines in high-temperature applications due to its exceptional thermal stability and oxidation resistance. Hastelloy, with its unmatched resistance to aggressive chemicals, is the alloy of choice for the most challenging corrosion scenarios.
In terms of processing, all three alloys can be welded and formed to meet specific design requirements. However, the welding parameters and post-weld heat treatment may vary depending on the alloy, reflecting their unique material properties.
Cost is another factor that needs to be considered when choosing between these alloys. Generally, Hastelloy alloys tend to be the most expensive due to their complex composition and specialized manufacturing processes. Inconel alloys, while also relatively costly, offer a cost-effective solution for high-temperature applications. Monel, while not the cheapest alloy available, offers good value for its corrosion resistance and mechanical properties.
Conclusion
In summary, the choice between Monel, Inconel, and Hastelloy alloys depends on the specific requirements of the application. Monel is suitable for structural applications in corrosive environments, Inconel excels in high-temperature scenarios, and Hastelloy is the preferred choice for handling aggressive chemicals.
Thank you for reading our article, and we hope it can help you to have a better understanding of the differences between Monel vs Inconel vs Hastelloy Alloys. If you are looking for Monel Alloy, Inconel Alloy, and Hastelloy Alloy suppliers online now, we would advise you to visit Huaxiao Alloy.
As a leading supplier of high-temperature alloys from Shanghai China, Huaxiao Alloy offers customers high-quality Monel 400 Alloy, Monel 500, Inconel 602 Alloy, Hastelloy S Alloy, Inconel Alloy 600, Inconel Alloy 601, Inconel 625 UNS N06625, Hastelloy B3 (UNS N10675), Hastelloy D205, Hastelloy G30 (UNS N06030), and Hastelloy C-2000 at a very competitive price.