Inconel 625 and Hastelloy C276 are renowned for their unique properties and widespread applications in various industries. However, they differ significantly in composition, corrosion resistance, mechanical properties, and optimal usage conditions. In this article, we will delve into these differences in detail, providing an accurate, professional, meticulous, and authoritative comparison.
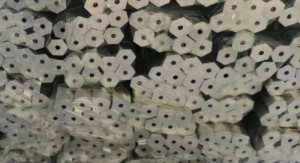
The Difference between Inconel 625 and Hastelloy C276 – 1. Composition
Firstly, let’s discuss the compositional differences between Inconel 625 and Hastelloy C276. Inconel 625, also known as UNS N06625, is primarily composed of nickel, chromium, and molybdenum. Nickel serves as the base metal, providing a strong and stable matrix for the alloy. Chromium and molybdenum are added to enhance corrosion resistance, particularly against oxidizing environments. This alloy’s composition allows it to retain its strength and ductility at high temperatures, making it suitable for use in extreme conditions.
On the other hand, Hastelloy C276, or UNS N10276, has a slightly different composition. It is a nickel-chromium-molybdenum alloy with the addition of tungsten and a small amount of cobalt. Tungsten significantly improves the alloy’s resistance to reducing environments, making it particularly resistant to corrosion caused by acids like hydrochloric acid. Cobalt further enhances the alloy’s mechanical properties, such as toughness and ductility.
The Difference between Inconel 625 and Hastelloy C276 – 2. Corrosion Resistance
Moving on to corrosion resistance, both alloys excel in this aspect but in slightly different ways. Inconel 625 demonstrates excellent resistance to oxidation and corrosion in high-temperature environments. It can withstand exposure to oxidizing agents and hot corrosive gases, maintaining its integrity even under severe conditions. This makes it ideal for applications such as turbine blades and exhaust systems in the aerospace and power generation industries.
Hastelloy C276, on the other hand, is renowned for its resistance to corrosion in reducing environments. It is particularly effective against corrosion caused by chlorides, sulfuric acid, and phosphoric acid. This alloy’s resistance to chloride-induced stress corrosion cracking is a key advantage, making it suitable for use in chemical processing equipment and piping that handles corrosive chemicals.
The Difference between Inconel 625 and Hastelloy C276 – 3. Mechanical Properties
In terms of mechanical properties, Inconel 625 excels at high temperatures. It maintains good strength and ductility even at temperatures approaching 1000°C, making it an excellent choice for high-temperature applications. Its high creep resistance and good fatigue strength further enhance its performance in demanding environments.
Hastelloy C276, while not as strong at extremely high temperatures as Inconel 625, still possesses good mechanical properties at room and elevated temperatures. It is tough and ductile, allowing it to be formed and welded into complex shapes. Its excellent corrosion resistance, combined with its mechanical properties, makes it a suitable choice for applications where both corrosion resistance and mechanical strength are critical.
The Difference between Inconel 625 and Hastelloy C276 – 4. Processing and Welding
When it comes to processing and welding, both alloys can be welded and formed using conventional techniques. However, Hastelloy C276 may require special welding parameters and post-weld heat treatment to ensure optimal corrosion resistance in the welded joints. Both alloys can also be forged, rolled, and extruded to meet specific manufacturing requirements.
The Difference between Inconel 625 and Hastelloy C276 – 5. Applications
Finally, let’s discuss the applications of these alloys. Inconel 625 finds widespread use in industries that require high-temperature performance and corrosion resistance. It is commonly used in turbine engines, rocket motors, and industrial furnaces, where it can withstand extreme heat and corrosive environments. Its ability to retain strength and ductility at high temperatures makes it a critical component in many high-performance applications.
Hastelloy C276, on the other hand, is widely used in the chemical processing industry. Its excellent resistance to corrosion by chlorides, sulfuric acid, and other corrosive chemicals makes it an ideal choice for equipment and piping that handle these substances. It is commonly found in chemical reactors, heat exchangers, and storage tanks, where it ensures the safe and efficient operation of the equipment.
Conclusion
In conclusion, Inconel 625 and Hastelloy C276 are both exceptional alloys with unique properties and applications. Their differences in composition, corrosion resistance, mechanical properties, and optimal usage conditions make them suitable for different industrial scenarios.
Thank you for reading our article and we hope it can help you to have a better understanding of the differences between Inconel 625 and Hastelloy C276. If you are looking for Inconel 625 and Hastelloy C276 suppliers and manufacturers online now, we would advise you to visit Huaxiao Alloy.
As a leading supplier of Inconel and Hastelloy alloys from Shanghai China, Huaxiao Alloy offers customers high-quality Inconel 625, Inconel 600, Inconel 601, Inconel 718, Hastelloy C276, Hastelloy C22, Hastelloy C2000, and Hastelloy B2 at a very competitive price.