Among various alloys, two alloys that have garnered significant attention in recent years are Alloy 59 and C2000. Both alloys possess exceptional characteristics that make them suitable for a wide range of applications, but there also exist distinct differences between alloy 59 and C2000. In this article, we will delve into the composition, properties, and uses of both Alloy 59 and C2000 to provide a comprehensive and authoritative comparison of these two alloys.
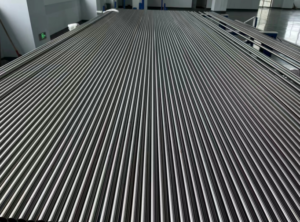
What are the differences between alloy 59 and C2000?
Let’s start with Alloy 59. This alloy is renowned for its low magnetic permeability, making it a prime choice for applications where magnetic properties are crucial. Its low magnetic signature ensures minimal interference with magnetic fields, a feature that is highly desirable in certain electronic and electromechanical systems. In addition to its magnetic properties, Alloy 59 also excels in corrosion resistance. It demonstrates remarkable resistance to various corrosive media, especially in acidic and alkaline environments. This resistance, coupled with its high mechanical strength and stability at elevated temperatures, makes Alloy 59 an ideal material for use in harsh and demanding environments.
Moreover, Alloy 59’s high-temperature stability and oxidation resistance are noteworthy. It maintains its strength and integrity even under extreme heat, resisting oxidation and thermal degradation. This characteristic is particularly valuable in applications such as high-temperature processing, where materials are exposed to extreme thermal conditions. The alloy’s composition, typically consisting of cobalt, chromium, and tungsten, among other elements, contributes to its excellent high-temperature performance.
On the other hand, C2000, also known as Hastelloy C-2000, is a nickel-based superalloy that possesses an array of exceptional properties. Its corrosion resistance is legendary, especially in environments that are corrosive due to acids, chlorides, and other chemicals. C2000 demonstrates remarkable resistance to stress corrosion cracking, a type of corrosion that can lead to material failure under tensile stress. This makes it an excellent choice for applications where materials are subject to both corrosive environments and mechanical stress.
The alloy’s composition, rich in nickel, chromium, molybdenum, and iron, accounts for its robust corrosion resistance. The presence of these elements creates a protective oxide layer on the alloy’s surface, effectively shielding it from the harmful effects of corrosive agents. Additionally, C2000 maintains its mechanical properties even at elevated temperatures, exhibiting excellent high-temperature strength and oxidation resistance. This allows it to perform reliably in high-temperature applications such as chemical processing and petrochemical operations.
Furthermore, C2000’s excellent weldability and machinability make it a highly versatile material. It can be easily fabricated into complex shapes and welded into structures without compromising its corrosion resistance or mechanical properties. This versatility, coupled with its superior corrosion resistance, makes C2000 a preferred material for use in a wide range of industries, including marine, chemical, and oil and gas.
In comparing Alloy 59 and C2000, it is evident that both alloys possess unique characteristics that make them suitable for different applications. Alloy 59 stands out for its low magnetic permeability and excellent corrosion resistance in acidic and alkaline environments, making it a prime choice for electronic and electromechanical systems. On the other hand, C2000’s unparalleled corrosion resistance, especially against acids and chlorides, combined with its high-temperature stability and weldability, render it ideal for chemical processing and high-temperature applications.
It is worth noting that the selection of an alloy for a specific application should always be based on a comprehensive evaluation of the operating conditions, environmental factors, and material requirements. While Alloy 59 and C2000 both offer excellent performance in their respective areas, the most suitable alloy for a given application will depend on the specific needs and challenges faced.
Conclusion
In conclusion, Alloy 59 and C2000 are two distinct alloys with unique properties and applications. Alloy 59 excels in low magnetic permeability and corrosion resistance in acidic and alkaline environments, while C2000 demonstrates unparalleled corrosion resistance against acids, chlorides, and other chemicals, coupled with high-temperature stability and weldability.
Thank you for reading our article and we hope it can help you to have a better understanding of the differences between alloy 59 and C2000. If you are looking for suppliers and manufacturers of alloy 59 and C2000, we would advise you to visit Huaxiao Alloy.
As a leading supplier of Hastelloy Alloys from Shanghai China, Huaxiao Alloy offers customers high-quality Hastelloy products such as Hastelloy C2000, Hastelloy C22, Hastelloy C276, Hastelloy C4, and Hastelloy B2 at a very competitive price.