What is DP steel?
- July 15, 2024
- 9:39 pm
- 936
DP steel, also known as dual-phase steel, is a type of high-strength steel. It is made from low carbon or low alloy steel through heat treatment or controlled rolling. The structure of DP steel consists of a ferrite matrix with about 20% martensite located at the ferrite grain boundaries, which is why it’s also called martensitic duplex steel. The primary components of duplex steel are carbon (C) and manganese (Mn). To enhance hardenability, elements like chromium (Cr) and molybdenum (Mo) are sometimes added.
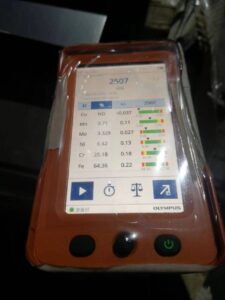
Common Grades of Dual-Phase Steel
DP600
- Carbon (C): Lower carbon content to enhance ductility.
- Manganese (Mn): Increased manganese content improves strength and hardness.
- Silicon (Si): Generally contains a small amount of silicon, which helps increase strength.
- Chromium (Cr) and Molybdenum (Mo): Sometimes added in small amounts to improve hardenability and corrosion resistance.
DP800
- Carbon (C): Slightly higher carbon content than DP600 to increase strength.
- Manganese (Mn): Higher content to enhance strength and toughness.
- Silicon (Si): Similar silicon content as DP600 to enhance material strength.
- Chromium (Cr) and Molybdenum (Mo): Typically contains more than DP600 to further improve strength and heat resistance.
DP1000
- Carbon (C): Higher carbon content than DP800 to maximize strength.
- Manganese (Mn): High manganese content provides extremely high strength and improves hardenability.
- Silicon (Si), Chromium (Cr), and Molybdenum (Mo): Higher levels to support extreme mechanical properties and heat resistance.
Summary
Different grades of dual-phase steel adjust the ratios of carbon, manganese, silicon, chromium, and molybdenum to achieve the desired mechanical and processing properties. The specific composition depends on the intended application requirements and processing techniques. High-strength dual-phase steels are suitable for demanding applications in automotive, construction, and industrial sectors where high strength and good formability are necessary.
DP steel Special performance
Duplex steel is a new material developed in the mid-1970s with low flexural strength ratio, high elongation and fast initial hardening rate.
DP steel applications
DP steel is widely used in automobile side beams, side members, cross members, pillars, chassis reinforcements, fuel tank supports and structural, reinforcing and crashworthiness parts of vehicle bodies.
DP steel Production process
During hot working of DP steel, the austenitized steel stays in the ferrite phase transition region for a long time by means of a reasonably designed cooling process, which ensures that 80% of the austenite phase is transformed into ferrite phase, and then cools below the Ms point by fast cooling, bypassing the bainite formation region, so as to form the organization of ferrite+martensite phases.
Here we take the more typical DP600 as a representative to discuss its production process.
Steel industry production of hot rolled DP steel strip process is divided into two kinds of low-temperature curling and medium-temperature curling.
Low-temperature curling process
One of the low-temperature curling process, low-temperature coiling hot-rolled duplex steel production principle is: in the cooling process after the final rolling to complete most of the A-F phase transition (about 80%), and in the rapid cooling stage thereafter will be quickly cooled to the M8 point of the strip below the coiling, to get the F plus M organization. The coiling temperature is generally below 300°C to avoid bainite formation, as well as aging of ferrite and self-tempering of martensite (as shown in the figure “Cooling Curve of Low Temperature Coiling Process”). It is characterized by a reduction in alloying element content, reducing costs, but the process parameters control requirements are stringent, especially the cooling process after the final rolling, control is more difficult, and requires the use of larger power coiling equipment. Only Japan’s Nippon Steel and Kawasaki Steel and other plants to apply this process, the domestic use of this process is less.
Medium temperature curling process
The second process is medium-temperature coiling, which utilizes alloying elements like chromium (Cr) and molybdenum (Mo) to enhance the stability of austenite within the standard temperature range used for coiling. During its continuous cooling, the steel transitions through a sub-stable phase between the A_ + F and A-B temperatures. After the final rolling, about 80% of the A_ + F phase transition is completed during cooling.
The steel is then coiled at a “coiling window” temperature, which falls between 500-600 ℃. This method ensures stability during the coiling process. As it cools to room temperature, the austenite in the steel transforms into martensite. This process ultimately yields a dual-phase microstructure consisting of ferrite (F) plus martensite (M).
If you found this article good, feel free to share it on your other social media platforms.