What is GH3039?
- July 23, 2024
- 12:30 am
- 51
GH3039 high temperature alloy is a single-phase austenitic solid solution strengthened deformed high temperature alloy with nickel as the main element. The alloy has excellent high-temperature strength, oxidation resistance and corrosion resistance, and is able to work stably for a long time in extreme high-temperature environments.
Below 800°C, GH3039 alloy exhibits moderate thermal strength and good resistance to hot and cold fatigue, while below 1000°C it has good oxidation resistance. After long-term use, its organizational structure remains stable and it has good cold forming and welding properties.
GH3039 high temperature alloy is widely used in aerospace, petrochemical, energy and chemical industries. Specific applications include aero-engine combustion chamber and charge combustion chamber components, turbine blades, flame cylinders and other high-temperature structural components. It is also used in the manufacture of key components in petrochemical equipment, such as oil pipelines and chemical equipment, where there are stringent requirements for the corrosion resistance of the material.
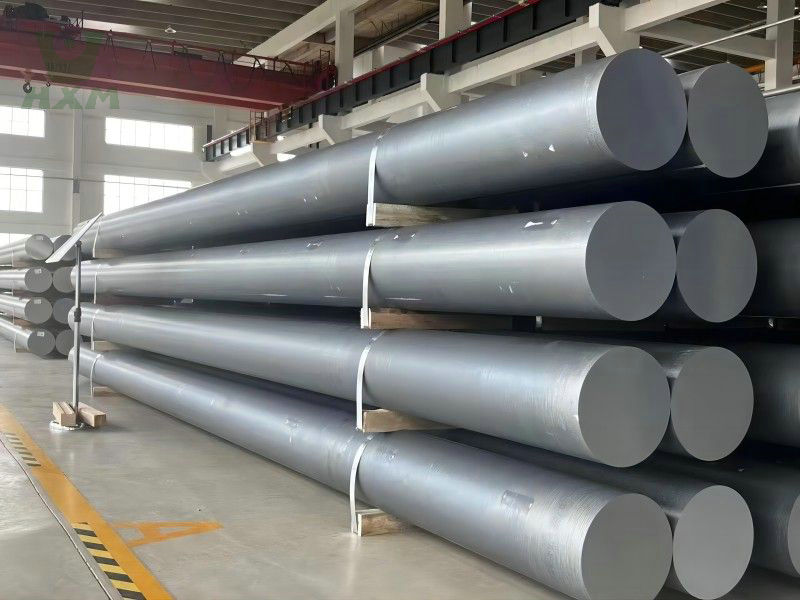
Chemical Composition of GH3039
GH3039 high temperature alloy is a solid solution strengthened nickel-based high temperature alloy with nickel, chromium and cobalt as main components, which has excellent high temperature strength and oxidation resistance. The following are its specific chemical composition and ratio:
- Nickel (Ni): about 50%~57%, providing the basic stability and corrosion resistance of the alloy.
- Chromium (Cr): about 19% ~ 22%, enhance the oxidation and corrosion resistance of the alloy.
- Cobalt (Co): about 10%, helps to improve the high temperature strength and creep resistance of the alloy.
- Molybdenum (Mo): about 8%, to further enhance the oxidation and corrosion resistance of the alloy.
- Tungsten (W): a small amount, used to improve the stability of the alloy under extreme conditions.
In addition, GH3039 high-temperature alloy may also contain other elements such as aluminum (Al), silicon (Si), manganese (Mn), etc., but the specific content of these elements is relatively small, usually below 0.1%.
Element | Composition (%) | Role/Benefits in Alloy |
---|---|---|
Nickel | 40-45 | Provides corrosion resistance, toughness, and strength at high temperatures. |
Chromium | 20-25 | Enhances oxidation and corrosion resistance, improves strength at high temperatures. |
Cobalt | Max 2.5 | Improves strength at high temperatures and enhances oxidation resistance. |
Tungsten | 12-14 | Increases high-temperature strength and hardness, improves creep resistance. |
Molybdenum | 1.8-2.3 | Enhances strength, hardenability, and resistance to creep and corrosion. |
Aluminum | 1.3-1.8 | Increases oxidation resistance, strength at high temperatures through formation of a protective oxide layer. |
Titanium | 0.4-1.1 | Strengthens the alloy through formation of stable carbides and nitrides, improves creep resistance. |
Carbon | Max 0.12 | Enhances strength by forming carbides, improves wear resistance. |
Boron | 0.005-0.015 | Refines grain boundaries, improves ductility and stress rupture strength. |
Silicon | Max 0.30 | Enhances oxidation resistance and strength, acts as a deoxidizer. |
Manganese | Max 0.40 | Acts as a deoxidizer, enhances hardness and strength. |
Phosphorus | Max 0.015 | Improves strength and corrosion resistance. |
Sulfur | Max 0.010 | Improves machinability (though generally kept low to avoid embrittlement). |
Iron | Balance | Provides structural support, enhances mechanical properties. |
mechanical property of GH3039
Property | Value |
---|---|
Density | Approximately 8.24 g/cm³ |
Tensile Strength | 980-1180 MPa |
Yield Strength | 470-730 MPa |
Elongation | About 30-35% |
Hardness | 321-352 HB (Brinell Hardness) |
Thermal Conductivity | About 11.5 W/m·K at 20 °C |
Specific Heat Capacity | About 400 J/kg·K at 20 °C |
Melting Point | Roughly 1260-1320 °C |
Application of GH3039
The application cases of GH3039 high temperature alloy in aerospace field are mainly focused on the manufacturing of aviation engines. Specifically, this alloy is widely used in the following types of key components:
- Turbine blades: GH3039 high-temperature alloy is commonly used in the manufacture of turbine blades due to its excellent high-temperature strength and oxidation resistance, which can withstand the extreme high-temperature environment of aero-engine operation.
- Combustion chamber: the combustion chamber is an important part of the aero-engine, need to have good high temperature stability and corrosion resistance, GH3039 high temperature alloy in this field ensures the reliability and durability of the combustion chamber in the high temperature and high pressure environment.
- Guide vanes: guide vanes also need to have good high-temperature mechanical properties and oxidation resistance to ensure their normal operation in the aero-engine, the application of GH3039 high-temperature alloy in these components further enhances the overall performance and reliability of the engine.
In addition, GH3039 high-temperature alloy also has good creep resistance and chemical stability, so that it also performs well in other high-temperature and high-pressure environments, such as gas turbines and nuclear power equipment.
Advantages of GH3039
GH3039 high-temperature alloy offers several significant advantages, making it suitable for demanding applications, especially in environments subject to extreme heat and corrosive conditions. Here are some of the key benefits of using GH3039:
High-Temperature Strength: GH3039 retains excellent mechanical strength and stability at elevated temperatures. This makes it ideal for components in jet engines, gas turbines, and other high-temperature applications.
Excellent Corrosion Resistance: The alloy is highly resistant to oxidation and corrosion, particularly in high-temperature environments. This resistance ensures longevity and reliability of components in harsh conditions.
Good Creep Resistance: Creep resistance is critical for materials used at high temperatures under stress. GH3039 maintains its structural integrity over long periods, resisting deformation under mechanical stress at high temperatures.
Thermal Stability: The alloy shows remarkable stability under thermal cycling conditions, resisting the effects of rapid temperature changes which can lead to material failure in many engineering applications.
Weldability: Despite its high-strength and corrosion-resistant properties, GH3039 can be welded with suitable techniques, which is beneficial for manufacturing complex assemblies.
Versatility in Applications: Due to its robust properties, GH3039 is used in a variety of aerospace applications, including turbine blades, exhaust systems, and combustion chambers, as well as in the chemical industry for processing equipment.
These attributes make GH3039 a preferred material in industries where performance and durability at high temperatures are mandatory, ensuring both safety and efficiency in critical applications.
The best stainless steel for high temperature applications depends on the specific requirements, but 310 Stainless Steel is often considered the top choice. It has excellent oxidation resistance up to 2000°F and also resists carburization at high temperatures. This makes it ideal for furnace parts and heat treatment equipment.
High temperature alloys, also known as super alloys, are materials that are designed to withstand extremely high temperatures and maintain structural integrity under stress and heat. These materials typically have a strong resistance to thermal creep deformation, good surface stability, and resistance to corrosion or oxidation. Common examples include nickel-based, cobalt-based, and iron-nickel-based alloys.
The “best” high temperature alloy often depends on the application, but Inconel 625 and Inconel 718 are frequently cited as among the top due to their ability to withstand extreme environmental conditions, including high temperatures and corrosive environments. They are commonly used in aerospace, chemical processing, and power plants.
Ceramics such as silicon carbide and tungsten carbide are known for their ability to withstand very high temperatures. These materials maintain strength and stability even at temperatures where most metals would melt or degrade, making them ideal for applications such as furnace linings, turbine components, and thermal barriers.
For environments reaching up to 3000 degrees Fahrenheit, zirconium diboride (ZrB2) is highly effective. It’s a type of ultra-high-temperature ceramic that excels in heat resistance and is often used in extreme aerospace environments and hypersonic vehicles where high thermal shock resistance is required.
At temperatures as high as 4000 degrees Fahrenheit, hafnium carbide (HfC) and tantalum carbide (TaC) are among the highest temperature-resistant materials known. These ultra-high-temperature ceramics are considered for applications in thermal protection systems in high-speed aerospace vehicles and as coatings for atmospheric reentry.
For metals capable of withstanding temperatures around 2000 degrees Fahrenheit, molybdenum and alloys like Tungsten are top choices. Molybdenum, in particular, maintains good mechanical stability at these high temperatures and is commonly used in furnace construction, aerospace engineering, and electrical contacts.
If you found this article good, feel free to share it on your other social media platforms.
What is GH3039?
Call Us Now!!!
May be of interest
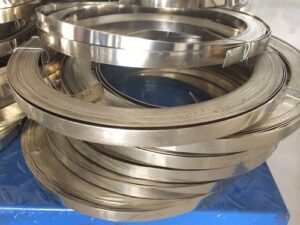
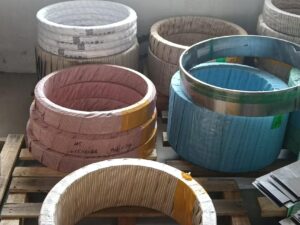
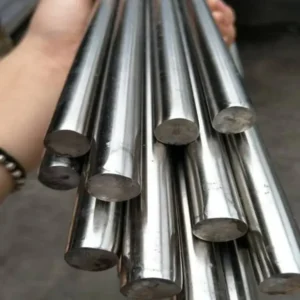
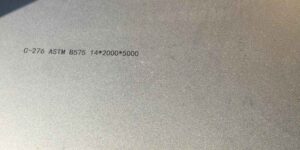
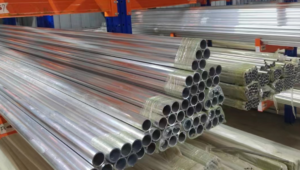
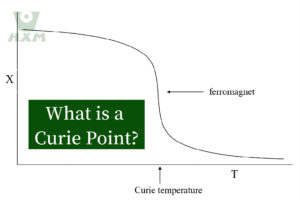
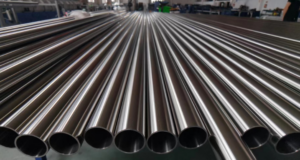
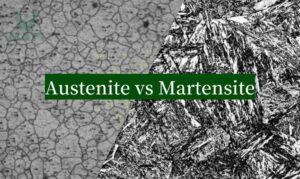
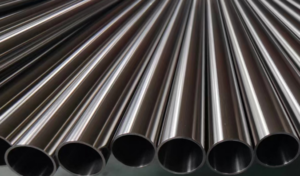
Factors Affecting the Corrosion Resistance Duration of Monel Alloy
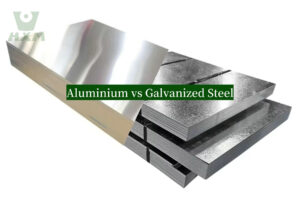
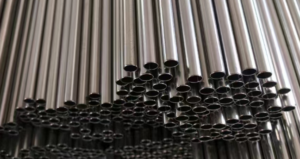
Incoloy Alloy’s Exceptional Processability: Manifestations Across Various Processing Techniques
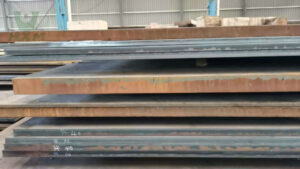
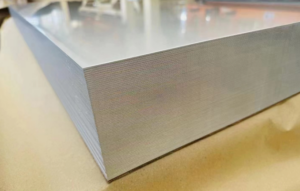
Chemical Composition and Performance Advantages of Hastelloy B-2 Alloy
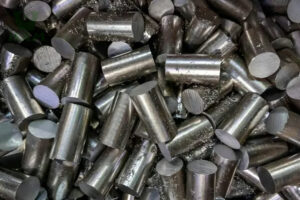