In the realm of high-performance alloys, Incoloy 800 vs Alloy 800 occupy a unique place, each with its own set of advantages and applications. Both alloys are iron-nickel–chromium based and are renowned for their resistance to oxidation and corrosion, making them ideal for use in harsh environments. However, there are several key differences between the two that set them apart in terms of composition, mechanical properties, and end-use scenarios.
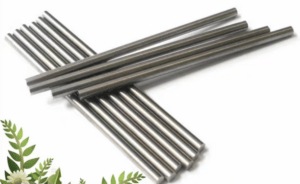
Incoloy 800 vs Alloy 800 – What’s the Difference?
Incoloy 800 vs Alloy 800 – 1. Composition
The fundamental difference between Incoloy 800 vs Alloy 800 lies in their composition.
Incoloy 800 is an austenitic nickel-iron-chromium alloy that contains additions of titanium and aluminum for stabilization. It typically has a higher chromium content than Alloy 800, ranging from 19.0 to 23.0% by weight. The higher chromium content in Incoloy 800 provides better resistance to oxidizing environments and some forms of corrosion.
On the other hand, Alloy 800 is an austenitic nickel-iron-chromium alloy with additions of titanium for stabilization. It has a chromium content ranging from 19.0 to 21.0% by weight, slightly lower than that of Incoloy 800. Alloy 800 also contains carbon, manganese, silicon, phosphorus, sulfur, and iron in addition to nickel and chromium.
Incoloy 800 vs Alloy 800 – 2. Mechanical Properties
Both alloys exhibit excellent mechanical properties, but there are some notable differences. Incoloy 800 offers higher tensile strength and yield strength compared to Alloy 800. This makes Incoloy 800 a more suitable choice for applications that require superior strength, such as pressure vessels and heat exchangers. However, Alloy 800 has better ductility and toughness, making it more suitable for applications that require flexibility and impact resistance.
Incoloy 800 vs Alloy 800 – 3. Corrosion Resistance
Both alloys are highly resistant to corrosion, but Incoloy 800 offers slightly better resistance in oxidizing environments due to its higher chromium content. This makes it an ideal choice for applications in chemical processing, petroleum refining, and power generation, where exposure to oxidizing agents is common. Alloy 800, on the other hand, exhibits better resistance to reducing environments and is commonly used in sulfuric acid service.
Incoloy 800 vs Alloy 800 – 4. Fabrication and Weldability
Both alloys can be easily fabricated and welded, but Alloy 800 is generally considered easier to work with due to its lower strength and better ductility. Incoloy 800, with its higher strength, may require more care during fabrication to avoid distortion or cracking. Both alloys can be welded using standard techniques and do not require any special pre- or post-weld heat treatment.
Incoloy 800 vs Alloy 800 – 5. Cost
The cost of Incoloy 800 and Alloy 800 can vary depending on the size, shape, and quantity of the material required. Generally speaking, Incoloy 800 may cost slightly more due to its higher chromium content and superior mechanical properties. However, the cost difference is often outweighed by the specific properties required for a given application.
Why Choose Huaxiao Alloy?
In summary, Incoloy 800 and Alloy 800 are both excellent choices for high-performance applications in harsh environments. The choice between the two depends on the specific requirements of the application, such as the need for strength, corrosion resistance, and fabrication ease. Incoloy 800 offers higher strength and better resistance to oxidizing environments, while Alloy 800 excels in ductility, toughness, and reducing environments.
Thank you for reading our article and we hope it can help you to have a better understanding of the differences between Incoloy 800 vs Alloy 800. If you are looking for Incoloy 800 & Alloy 800 suppliers online now, please don’t hesitate to contact Huaxiao Alloy.
As a leading supplier of Incoloy products from Shanghai, China, Huaxiao Alloy provides customers with high-quality products such as Incoloy 800 and Incoloy Alloy 925 (UNS N08925) at a very competitive price.