Alloy 400 vs Hastelloy C – What’s the Difference?
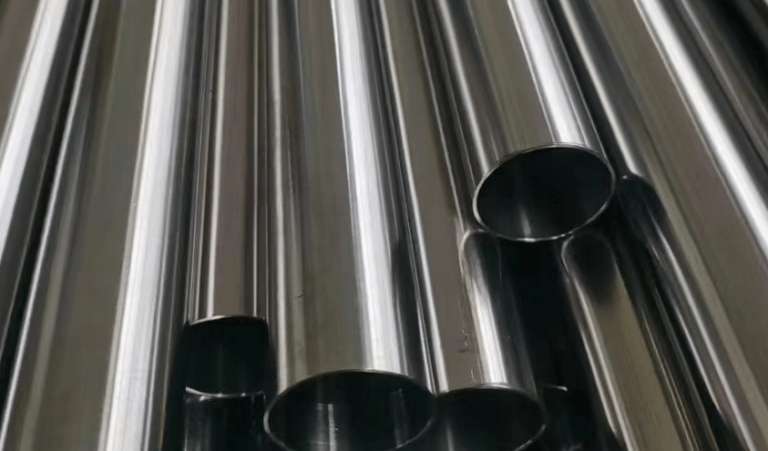
In the realm of metallurgy, alloys play a pivotal role in various industrial applications due to their enhanced properties compared to pure metals. Two such notable alloys are Alloy 400 vs Hastelloy C, each with its own set of unique characteristics and uses. This article aims to provide a comprehensive comparison between these two alloys, highlighting their compositions, properties, applications, and relative performance in different environments.
Alloy 400 vs Hastelloy C – 1. Alloy 400
Alloy 400, also known as Monel 400, is a nickel-copper alloy that has been in use for over a century. It is primarily composed of approximately 65-70% nickel and 25-30% copper, with small amounts of other elements such as iron, manganese, carbon, and silicon. This alloy is renowned for its excellent corrosion resistance, particularly in marine environments where it resists seawater and brine corrosion. It also exhibits good ductility and weldability, making it suitable for various fabrication processes.
One of the key strengths of Alloy 400 is its resistance to stress corrosion cracking in chloride-bearing environments. However, it should be noted that this alloy is not suitable for use at temperatures exceeding 550°F (288°C) as it can suffer from creep deformation and loss of strength. Additionally, Alloy 400 has a relatively low melting point and is subject to galvanic corrosion when coupled with dissimilar metals.
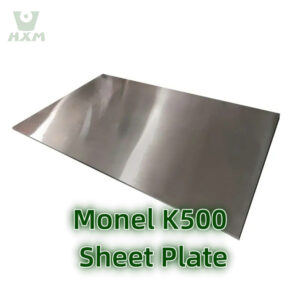
Monel K500 Sheet / Plate / Coil
Huaxiao-Alloy, a leading Monel K500 sheet manufacturer, supplies ASTM B865-certified sheets, plates & coils with unmatched strength and corrosion resistance. Fast delivery & OEM support.
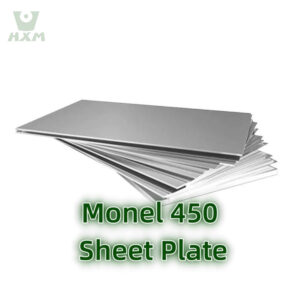
Monel 450 Sheet / Plate / Coil
Huaxiao-Alloy, a trusted Monel 450 sheet manufacturer, supplies ASTM B127-certified sheets, plates & coils with exceptional corrosion resistance. Competitive pricing & global shipping.
Alloy 400 vs Hastelloy C – 2. Hastelloy C
Hastelloy C, on the other hand, is a nickel-chromium-molybdenum alloy that belongs to the Hastelloy family of alloys. It contains significant amounts of nickel, chromium, and molybdenum, along with smaller quantities of iron, cobalt, manganese, carbon, and silicon. This alloy is well-known for its exceptional corrosion resistance, especially in severe environments involving strong acids, oxidizing media, and chloride-containing solutions.
Hastelloy C exhibits excellent resistance to pitting, crevice corrosion, and stress corrosion cracking. It also maintains its mechanical properties at high temperatures, making it suitable for use in high-temperature applications such as heat exchangers and furnaces. Additionally, Hastelloy C has good weldability and can be easily fabricated into complex shapes using various processes.
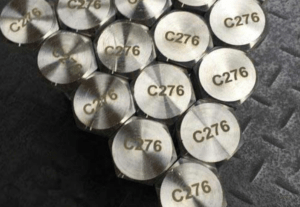
Hastelloy C-276 belongs to nickel-molybdenum-chromium-iron-tungsten nickel-based alloy, which is one of the most corrosion-resistant modern metal materials.
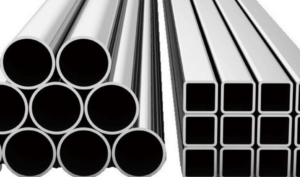
Hastelloy X is a nickel-based superalloy known for its exceptional high-temperature strength and oxidation resistance.
Alloy 400 vs Hastelloy C – 3. Comparison
When comparing Alloy 400 and Hastelloy C, several key differences become apparent:
- Composition: Alloy 400 is primarily a nickel-copper alloy, while Hastelloy C contains significant amounts of nickel, chromium, and molybdenum.
- Corrosion Resistance: Both alloys offer excellent corrosion resistance, but Hastelloy C is superior in severe environments due to its higher chromium and molybdenum content. Alloy 400 is more suitable for marine applications and resists seawater corrosion well.
- Temperature Resistance: Hastelloy C maintains its mechanical properties at higher temperatures compared to Alloy 400, making it more suitable for high-temperature applications.
- Cost: Alloy 400 is generally more cost-effective than Hastelloy C due to its simpler composition and wider availability.
- Applications: Alloy 400 is commonly used in marine hardware, chemical processing equipment, and heat exchangers. Hastelloy C, on the other hand, finds its applications in more severe environments such as chemical processing, power generation, and pollution control.
Conclusion
In conclusion, both Alloy 400 vs Hastelloy C are highly regarded alloys with unique properties and applications. The choice between them depends on the specific requirements of the application, such as corrosion resistance, temperature resistance, cost, and fabricability.
Thank you for reading our article. We hope it can help you to have a better understanding of the differences between Alloy 400 vs Hastelloy C. If you are looking for Alloy 400 and Hastelloy C suppliers online now, please don’t hesitate to contact Huaxiao Alloy.
As a leading supplier of Hastelloy Alloys from Shanghai China, Huaxiao Alloy provides customers with high-quality Hastelloy C2000, Hastelloy B3 (UNS N10675), Hastelloy D205, Hastelloy G30 (UNS N06030), Hastelloy B2, Hastelloy X alloy, Hastelloy C4, Hastelloy C-276, and Hastelloy C22 at a very competitive price.
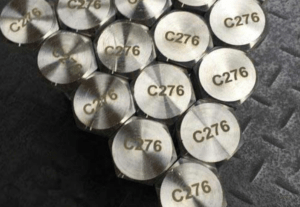
Hastelloy C-276 belongs to nickel-molybdenum-chromium-iron-tungsten nickel-based alloy, which is one of the most corrosion-resistant modern metal materials.
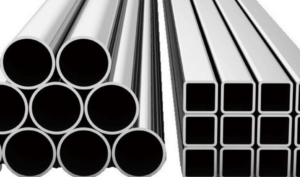
Hastelloy X is a nickel-based superalloy known for its exceptional high-temperature strength and oxidation resistance.
The term “alloy” is a broad category, while “Hastelloy” refers to a specific group of corrosion-resistant alloys.
-
Alloy:
- A metallic material made by combining two or more elements, often to enhance properties such as strength, corrosion resistance, or heat resistance. Examples include stainless steel, brass, and aluminum alloys.
- Can be tailored for specific applications by varying the composition.
-
Hastelloy:
- A trademarked family of corrosion-resistant alloys primarily made of nickel with molybdenum, chromium, and iron.
- Known for exceptional performance in highly corrosive environments, particularly with acids, oxidizing, and reducing agents.
In short, Hastelloy is a subset of alloys specifically designed for extreme chemical and thermal environments.
Alloy 400 and Alloy 625 differ in composition, corrosion resistance, and mechanical properties:
-
Chemical Composition:
- Alloy 400: A nickel-copper alloy (commonly called Monel 400) with approximately 63% nickel and 28-34% copper.
- Alloy 625: A nickel-chromium-molybdenum alloy with added niobium for strength and corrosion resistance.
-
Corrosion Resistance:
- Alloy 400 excels in seawater and environments with hydrofluoric acid or sulfuric acid but has limited resistance to oxidizing agents.
- Alloy 625 offers superior corrosion resistance to both oxidizing and reducing agents, including chloride-induced pitting and crevice corrosion.
-
Applications:
- Alloy 400: Used in marine environments, chemical processing, and oil/gas industries.
- Alloy 625: Preferred in aerospace, marine, and pollution control systems due to its high strength and thermal stability.
Hastelloy C4 and C276 are nickel-molybdenum-chromium alloys, but they differ in performance and application scope:
-
Chemical Composition:
- C4: Contains lower iron and higher nickel content, optimized for thermal stability.
- C276: Includes tungsten for enhanced corrosion resistance, especially in reducing conditions.
-
Corrosion Resistance:
- C4: Performs exceptionally well in reducing environments and hot acids at elevated temperatures.
- C276: Offers broader chemical resistance, excelling in both oxidizing and reducing environments and chloride-induced pitting.
-
Applications:
- C4: Used in chemical processing with high temperatures and concentrated acids.
- C276: Versatile, found in marine, chemical processing, and pollution control industries.
Alloy 400 (Monel 400) equivalents vary by region or standard:
-
Standards and Equivalents:
- UNS N04400
- DIN 2.4360
- BS NA 12
- ASTM B127, B164, B165
-
Similar Alloys:
- Incoloy 825 and Alloy K-500 (depending on the application, as K-500 offers higher strength).
The specific choice depends on the required mechanical and corrosion resistance properties.
Alloy 400 and Alloy C276 differ significantly in terms of composition and application:
-
Chemical Composition:
- Alloy 400: Nickel-copper alloy.
- Alloy C276: Nickel-molybdenum-chromium alloy with tungsten.
-
Corrosion Resistance:
- Alloy 400: Excels in marine environments and environments containing hydrofluoric acid.
- Alloy C276: Provides superior resistance to a wide range of oxidizing and reducing chemicals, including chlorides and strong acids.
-
Applications:
- Alloy 400: Common in marine, oil/gas, and chemical industries.
- Alloy C276: Suitable for harsh chemical processing, pollution control, and marine applications requiring resistance to both oxidizing and reducing agents.
Yes, Alloy 400 is commonly referred to as Monel 400, a trademarked name.
-
Features:
- It is a nickel-copper alloy with exceptional corrosion resistance, particularly in marine and chemical environments.
- Monel is a brand name, but “Alloy 400” is used to describe the same material in generic terms.
-
Applications:
- Heat exchangers, pumps, and marine engineering.
While Monel 400 is the same as Alloy 400, other Monel alloys (like K-500) have distinct properties.