Today, we will focus on the comparison between Alloy 400 vs Inconel 625, two alloys that, despite their shared applications in diverse industries, possess distinct properties and characteristics that make them suitable for different sets of operating conditions.
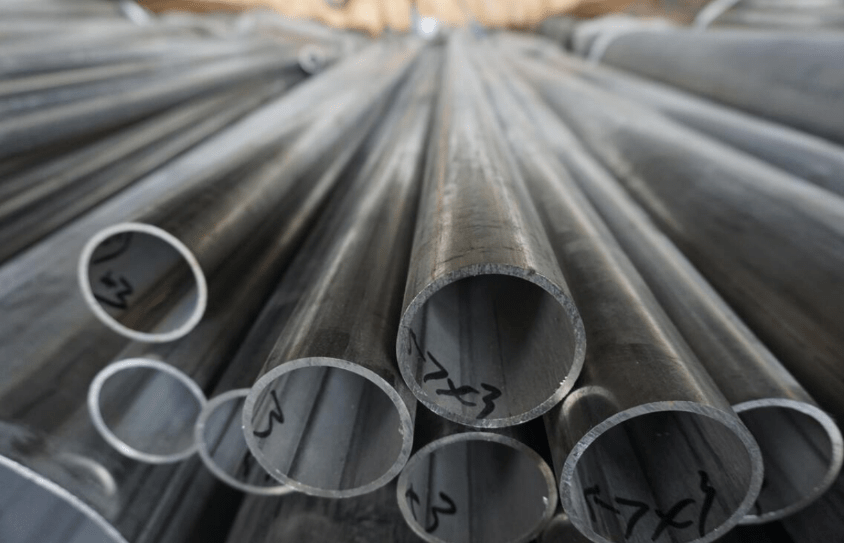
Alloy 400 vs Inconel 625 – What’s the Difference?
Alloy 400 vs Inconel 625 – Composition
Let’s start with a brief overview of their compositions. Alloy 400, also known as Monel 400, is a nickel-copper alloy with high corrosion resistance in a wide range of media, including seawater, saltwater, and various acids. Its composition allows it to retain strength and ductility even under extreme conditions. In contrast, Inconel 625 is a nickel-chromium-molybdenum alloy that is prized for its excellent resistance to oxidation and corrosion, as well as its high strength and toughness at elevated temperatures.
Alloy 400 vs Inconel 625 – Corrosion Resistance
One of the primary differences between these two alloys lies in their corrosion resistance. Alloy 400 excels in marine environments and is often used in seawater applications due to its outstanding resistance to chloride stress corrosion cracking. Its corrosion resistance is also notable in acidic environments. Inconel 625, on the other hand, demonstrates remarkable corrosion resistance in oxidizing and reducing environments, including sulfuric and phosphoric acids. Its high chromium content contributes to its excellent resistance to oxidizing media.
Alloy 400 vs Inconel 625 – Mechanical Properties
In terms of mechanical properties, Inconel 625 outperforms Alloy 400 at higher temperatures. Inconel 625 maintains its strength and ductility even at temperatures exceeding 1000°C, making it a preferred choice for high-temperature applications such as turbine engines and exhaust systems. Alloy 400, while strong and ductile at room temperature, may not perform as well at elevated temperatures.
Alloy 400 vs Inconel 625 – Fabrication Characteristics
Fabrication characteristics are another area where these alloys differ. Alloy 400 is relatively easy to work with and can be welded, forged, and machined using standard metallurgical practices. Its good formability and weldability make it a popular choice for a wide range of applications. Inconel 625, while also weldable and machinable, may require special welding techniques and post-weld heat treatment to ensure optimal performance.
Alloy 400 vs Inconel 625 – Cost
Cost is another factor that often plays a role in material selection. Generally speaking, Alloy 400 is more cost-effective than Inconel 625, making it a more attractive option for budget-conscious projects. However, the superior performance of Inconel 625 in high-temperature and corrosive environments often justifies its higher cost in critical applications.
Alloy 400 vs Inconel 625 – Application
Finally, the choice between Alloy 400 and Inconel 625 ultimately depends on the specific requirements of the application. Alloy 400 is ideal for applications that involve exposure to seawater or acidic environments where corrosion resistance is paramount. Its good formability and weldability also make it suitable for a wide range of fabrication processes. Inconel 625, on the other hand, is the preferred choice for high-temperature applications that require exceptional strength and corrosion resistance.
Conclusion
In conclusion, while both Alloy 400 and Inconel 625 are excellent materials with unique properties, their differences in composition, corrosion resistance, mechanical properties, fabricability, and cost make them suitable for different applications.
Thank you for reading our article and we hope it can help you to have a better understanding of the differences between Alloy 400 vs Inconel 625. If you are looking for Alloy 400 & Inconel 625 suppliers online now, we would advise you to visit Huaxiao Alloy.
As a leading supplier of Inconel Alloys from Shanghai China, Huaxiao Alloy offers high-quality Alloy 400 & Inconel 625, Inconel 600, Inconel 601, and Inconel 718 at a very competitive price.