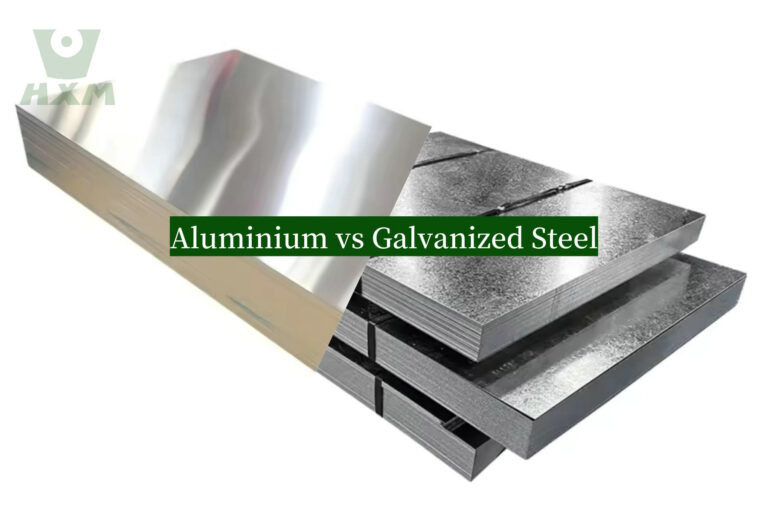
When talking about aluminium vs galvanized steel, aluminum is generally better suited for applications where corrosion resistance, lightweight properties, and ease of fabrication are crucial, despite its higher cost. Galvanized steel, on the other hand, is the better choice for applications requiring high strength, durability, and cost-effectiveness, especially in structural and large-scale projects.
Aluminium vs Galvanized Steel Table
Comparison Dimension | Aluminium | Galvanized Steel |
---|---|---|
Strength | Moderate, strong in certain alloys | High, very strong under load |
Corrosion Resistance | Excellent, naturally resistant | Good, zinc coating provides protection |
Weight | Lightweight (about 1/3 of steel) | Heavier, more stable structurally |
Cost | Higher | Lower |
Ease of Fabrication | High, easy to work with | Moderate, heavier and more challenging |
Aluminium vs Galvanized Steel——Strength
- Aluminium: While it is generally less strong than steel, certain aluminum alloys provide substantial strength, making them suitable for applications that require both lightness and durability.
- Galvanized Steel: Known for its high tensile strength, galvanized steel is ideal for heavy-duty applications, offering significant resistance to deformation under load.
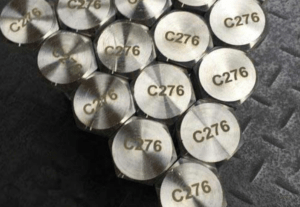
Hastelloy C-276 belongs to nickel-molybdenum-chromium-iron-tungsten nickel-based alloy, which is one of the most corrosion-resistant modern metal materials.
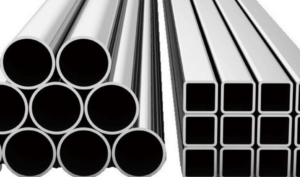
Hastelloy X is a nickel-based superalloy known for its exceptional high-temperature strength and oxidation resistance.
Aluminium vs Galvanized Steel——Corrosion Resistance
- Aluminium: Aluminum’s natural oxide layer provides excellent corrosion resistance, especially in marine and coastal environments, making it ideal for outdoor applications where exposure to moisture and salt is common.
- Galvanized Steel: The zinc coating offers good corrosion protection, particularly in less severe environments. However, over time, the coating can wear off, leading to potential rusting.
Aluminium vs Galvanized Steel——Weight
- Aluminium: Being much lighter, aluminum is preferred in industries where reducing weight is a priority, such as aerospace, automotive, and portable structures.
- Galvanized Steel: Heavier, which provides additional stability in structural applications but can be a disadvantage where weight is a concern.
Aluminium vs Galvanized Steel——Cost
- Aluminium: Typically more expensive due to its desirable properties. Its higher price is justified in applications where weight savings and corrosion resistance are essential.
- Galvanized Steel: More cost-effective, making it a better choice for budget-conscious projects, especially in construction and industrial applications.
Aluminium vs Galvanized Steel——Ease of Fabrication
- Aluminium: Easier to fabricate due to its malleability and lower density. It is well-suited for complex designs and applications requiring intricate shapes.
- Galvanized Steel: More difficult to work with due to its weight and hardness, though it remains widely used in construction due to its strength.
Advantages
Lightweight:
- Low Density: About one-third the weight of steel, making it ideal for applications where weight reduction is crucial.
- Energy Efficiency: Lower weight reduces energy consumption in transportation and use.
High Strength-to-Weight Ratio:
- Alloy Strengthening: Aluminum alloys can be strengthened for high-performance applications while remaining lightweight.
Corrosion Resistance:
- Oxide Layer: Forms a protective oxide layer that resists further corrosion.
- Chemical Resistance: Performs well in mild acidic and alkaline environments.
Good Conductivity:
- Electrical: Efficient for power lines due to its good conductivity per weight.
- Thermal: Excellent for heat exchangers and cooling components.
Ease of Processing:
- Formability: Easily processed into various shapes through rolling, extrusion, etc.
- Weldability: Can be joined through welding and other methods.
Recyclability:
- Environmental Impact: Highly recyclable, with only 5% of the energy needed to produce new aluminum.
Disadvantages
Relatively Low Strength:
- Pure Aluminum: Limited in high-stress applications unless alloyed.
Low Melting Point:
- Temperature Limitation: Melts at 660°C, limiting use in high-temperature applications.
- Creep: Prone to deformation under stress at high temperatures.
Welding Challenges:
- Oxide Layer: Requires special preparation to avoid welding defects.
- Thermal Expansion: High expansion can cause stress and deformation during welding.
Poor Wear Resistance:
- Low Hardness: Less resistant to wear, often needing surface treatments.
Corrosion Issues:
- Galvanic Corrosion: Susceptible in contact with dissimilar metals, especially in marine environments.
- Alkaline Corrosion: Poor resistance in high-pH environments.
Advantages
Corrosion Resistance:
- Zinc Coating: Protects steel from rust and corrosion, even when scratched.
- Long-Lasting: Extends the life of the steel, especially in outdoor environments.
Cost-Effective:
- Low Maintenance: Minimal upkeep required, leading to lower long-term costs.
- Affordable: Generally more cost-effective than stainless steel.
Durability:
- Long Service Life: Durable in various conditions, lasting for decades.
- Impact Resistance: Zinc coating adds protection against mechanical damage.
Versatility:
- Wide Applications: Used in construction, automotive, agriculture, and more.
Disadvantages
Aesthetic Limitations:
- Appearance: Dull, gray finish may not be visually appealing.
- Paint Adherence: Requires special preparation for painting.
Weldability Issues:
- Complex Welding: Requires special techniques and precautions.
- Health Risks: Zinc fumes from welding can be hazardous.
Environmental Impact:
- Galvanizing Process: Involves chemicals and energy-intensive methods.
- Recycling Challenges: Zinc coating complicates recycling.
Temperature Limitation:
- Zinc Melting Point: Not suitable for high-temperature applications due to the low melting point of zinc.
conclusion
In summary, aluminum is better for applications that demand lightweight, corrosion-resistant, and easily fabricated materials, despite the higher cost. Galvanized steel excels in scenarios where strength, durability, and cost efficiency are paramount, particularly in structural projects. The best choice depends on balancing these factors according to the specific requirements of the application.
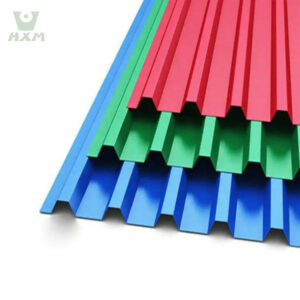
Pre-Painted Galvalume Steel Coil / Sheet / Plate
Huaxiao-Alloy’s Pre-Painted Galvalume® Steel combines 55% aluminum-zinc alloy substrate with precision-engineered polymer coatings – delivering 4-6x longer service life vs. standard PPGI.
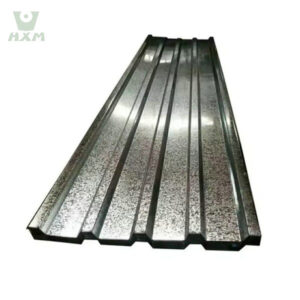
Pre-Painted Galvanized Steel Coil / Sheet / Plate
Huaxiao-Alloy’s Pre-Painted Galvanized Steel combines dual-layer protection: a zinc-based metallic substrate (GI or GL) with advanced polymer coatings – engineered to withstand UV degradation, chemical exposure, and mechanical stress while maintaining color integrity for 20-40 years.
The choice between aluminum and a galvanized iron (GI) sheet depends on the application:
- Aluminium: Better for applications requiring corrosion resistance, lightweight properties, and ease of fabrication. It is preferred in environments exposed to moisture, such as coastal areas, and in industries where weight reduction is critical (e.g., aerospace, automotive).
- GI Sheet: Better for applications requiring higher strength and durability, particularly in structural or heavy-duty applications. GI sheets are more cost-effective and offer sufficient corrosion protection for less harsh environments.
Conclusion: Aluminum is better for lightweight, corrosion-resistant applications, while GI sheets are better for cost-effective, strong, and durable applications.
The better material between aluminum and steel depends on the specific requirements:
- Aluminium: Preferred for its lightweight, corrosion resistance, and ease of fabrication. It is ideal for transportation, aerospace, and applications where weight savings are critical.
- Steel: Known for its high strength, durability, and cost-effectiveness. Steel is better suited for structural applications and heavy-duty uses where high tensile strength is necessary.
Conclusion: Aluminum is better for lightweight and corrosion-resistant needs, while steel is superior for strength and structural applications.
The main downsides of galvanized steel include:
- Limited Corrosion Resistance: Over time, the zinc coating can wear off, especially in harsh environments, exposing the steel to rust.
- Weight: Galvanized steel is heavier than aluminum, making it less suitable for applications where weight is a concern.
- Aesthetic Degradation: The appearance of galvanized steel can degrade over time as the zinc coating weathers, leading to a dull, mottled surface.
Conclusion: The primary downsides of galvanized steel are its potential for rusting after the zinc coating wears off, its weight, and the degradation of its appearance over time.
Galvanized steel is better in several aspects:
- Strength: It offers higher tensile strength and durability, making it ideal for structural applications.
- Cost-Effective: It is generally more affordable than other corrosion-resistant materials like stainless steel or aluminum.
- Protection: The zinc coating provides a good level of corrosion resistance, protecting the steel from rust in moderate environments.
Conclusion: Galvanized steel is better for applications requiring high strength, durability, and cost-effectiveness, with moderate corrosion protection.
The lifespan of galvanized steel depends on the environment:
- Moderate Environments: In environments with low to moderate moisture and pollutants, galvanized steel can last 20 to 50 years.
- Harsh Environments: In coastal or industrial environments with high moisture, salt, or chemicals, the lifespan may be reduced to 10 to 20 years as the zinc coating wears off faster.
Conclusion: Galvanized steel typically lasts 20 to 50 years in moderate environments but may have a shorter lifespan in harsher conditions.
Aluminum is preferred to steel in certain applications due to:
- Corrosion Resistance: Aluminum naturally forms a protective oxide layer, making it highly resistant to corrosion, especially in marine and coastal environments.
- Lightweight: Aluminum is about one-third the weight of steel, making it ideal for applications where weight savings are critical, such as in aerospace and transportation.
- Ease of Fabrication: Aluminum is easier to work with, being more malleable and easier to shape, cut, and weld.
Conclusion: Aluminum is preferred over steel in applications where corrosion resistance, lightweight properties, and ease of fabrication are crucial.
The longevity of aluminum vs. steel depends on the environment and application:
- Aluminium: Generally lasts longer in corrosive environments due to its natural corrosion resistance. It is particularly durable in marine or coastal settings.
- Steel: Steel, especially if not galvanized or treated, is more prone to rusting in corrosive environments. However, in non-corrosive environments, steel can last a long time due to its strength.
Conclusion: Aluminum typically lasts longer than steel in environments where corrosion is a concern, while steel can last longer in non-corrosive settings due to its inherent strength.
Steel is more popular than aluminum due to several factors:
- Strength: Steel offers superior strength, making it the material of choice for structural and heavy-duty applications.
- Cost: Steel is generally more affordable than aluminum, making it more accessible for large-scale construction and industrial projects.
- Versatility: Steel’s wide range of grades and alloys allows it to be used in various applications, from construction to manufacturing.
Conclusion: Steel’s popularity is driven by its strength, cost-effectiveness, and versatility, making it the preferred material for many industrial and construction applications.