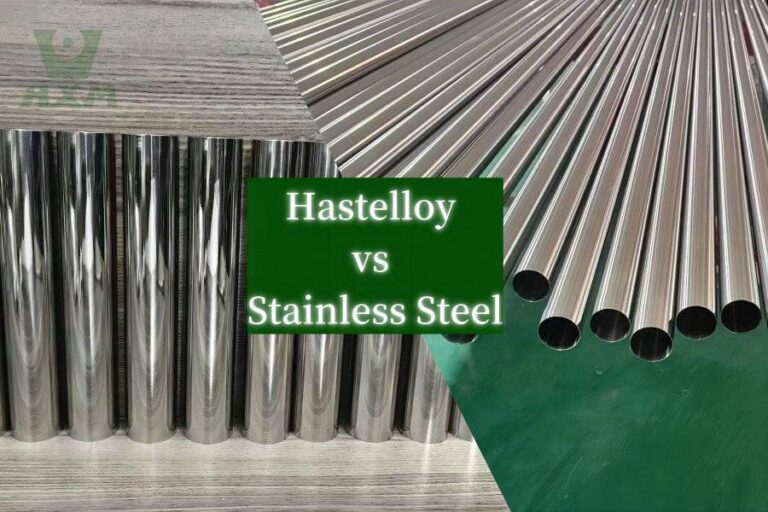
Hastelloy and stainless steel are two of the most commonly used materials in the fields of engineering and manufacturing, each offering distinct characteristics and benefits for a variety of applications. This article provides a comprehensive comparison between Hastelloy alloys and stainless steel, highlighting their chemical compositions, mechanical properties, applications, common forms, and differences in appearance.
Hastelloy vs Stainless Steel——chemical composition difference
Element | Hastelloy C-276 (%) | Stainless Steel 304 (%) | Stainless Steel 316 (%) |
---|---|---|---|
Nickel (Ni) | 50 – 63 | 8 – 10.5 | 10 – 14 |
Chromium (Cr) | 14.5 – 16.5 | 18 – 20 | 16 – 18 |
Molybdenum (Mo) | 15 – 17 | 0 – 0.75 | 2 – 3 |
Iron (Fe) | 4 – 7 | Balance | Balance |
Cobalt (Co) | 2.5 max | – | – |
Tungsten (W) | 3 – 4.5 | – | – |
Manganese (Mn) | 1 max | 2 max | 2 max |
Silicon (Si) | 0.08 max | 0.75 max | 0.75 max |
Carbon (C) | 0.01 max | 0.08 max | 0.08 max |
Vanadium (V) | 0.35 max | – | – |
Phosphorus (P) | 0.04 max | 0.045 max | 0.045 max |
Sulfur (S) | 0.03 max | 0.03 max | 0.03 max |
This table shows how the chemical compositions of Hastelloy and stainless steel are tailored to meet different environmental and mechanical demands, influencing their performance and suitability for various applications.
- Nickel (Ni): Higher in Hastelloy C-276, contributing to its outstanding corrosion resistance in reducing environments.
- Chromium (Cr): Present in all, but proportions vary; critical for oxidation resistance.
- Molybdenum (Mo) and Tungsten (W): Higher in Hastelloy, enhancing resistance to pitting and crevice corrosion.
- Iron (Fe): Predominantly in stainless steels, providing overall strength and durability.
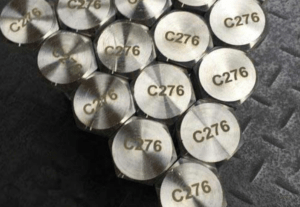
Hastelloy C-276 belongs to nickel-molybdenum-chromium-iron-tungsten nickel-based alloy, which is one of the most corrosion-resistant modern metal materials.
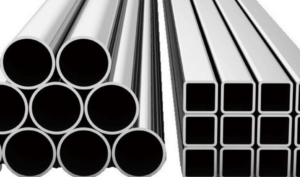
Hastelloy X is a nickel-based superalloy known for its exceptional high-temperature strength and oxidation resistance.
Hastelloy vs Stainless Steel——mechanical property difference
Property | Hastelloy C-276 | Stainless Steel 304 | Stainless Steel 316 |
---|---|---|---|
Tensile Strength | 690 MPa (100 ksi) | 505 MPa (73 ksi) | 515 MPa (75 ksi) |
Yield Strength | 283 MPa (41 ksi) | 215 MPa (31 ksi) | 205 MPa (30 ksi) |
Elongation | 40% | 40% | 40% |
Hardness | Rb 100 | Rb 80-90 | Rb 80-90 |
Melting Point | 1325-1370 °C (2415-2500 °F) | 1400-1450 °C (2552-2642 °F) | 1375-1400 °C (2507-2552 °F) |
Thermal Conductivity | 9.3 W/m·K | 16.2 W/m·K | 16.3 W/m·K |
Coefficient of Thermal Expansion | 11.2 µm/m·°C (20-100°C) | 17.2 µm/m·°C (20-100°C) | 15.9 µm/m·°C (20-100°C) |
- Tensile and Yield Strength: Hastelloy C-276 exhibits higher tensile strength compared to both grades of stainless steel, indicating its ability to withstand greater stress before deforming or failing.
- Elongation: Similar elongation across all materials suggests comparable ductility, meaning they can all withstand similar levels of deformation before fracture.
- Hardness: Hastelloy tends to be harder than the stainless steel grades, implying better resistance to surface wear and scratching.
- Melting Point: Stainless steel generally has a higher melting point, indicating potential for higher temperature applications.
- Thermal Conductivity: Stainless steel has higher thermal conductivity than Hastelloy, making it more effective in applications requiring heat transfer.
- Coefficient of Thermal Expansion: Hastelloy has a lower coefficient, meaning it expands less in response to temperature changes, which is advantageous in high-temperature applications where dimensional stability is critical.
This comparison table provides a clear view of how the mechanical properties of Hastelloy C-276 and stainless steel differ, influencing their performance in various engineering and industrial applications.
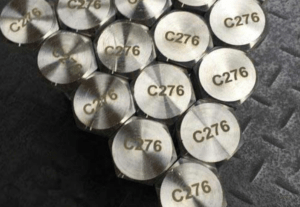
Hastelloy C-276 belongs to nickel-molybdenum-chromium-iron-tungsten nickel-based alloy, which is one of the most corrosion-resistant modern metal materials.
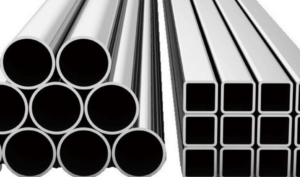
Hastelloy X is a nickel-based superalloy known for its exceptional high-temperature strength and oxidation resistance.
Hastelloy vs Stainless Steel——application difference
Hastelloy
Hastelloy is a nickel-based superalloy known for its outstanding resistance to severe corrosion and high-temperature environments. It is commonly used in chemical processing, aerospace, and industrial gas turbine and marine industries.
Typical Applications:
- Chemical Processing: Hastelloy excels in environments with hot contaminated mineral acids, solvents, chlorine, and chlorine contaminated media. It is commonly used in reactors, pipes, and pumps where acid resistance is critical.
- Pollution Control: Used in waste treatment and flue gas desulfurization systems.
- Aerospace: Components such as turbine exhausts, combustion cans, and spray bars that must resist high temperatures and corrosion.
- Nuclear Reactors: Due to its resistance to corrosion in high-temperature water and steam, Hastelloy is used in nuclear reactors, especially in heat exchanger tubing.
Classic Grades:
- Hastelloy C-276: Known for its excellent corrosion resistance in a wide range of aggressive media.
- Hastelloy B-3: Exceptional resistance to hydrochloric acid at all concentrations and temperatures.
Stainless Steel
Stainless Steel is an iron-based alloy with a minimum of 10.5% chromium content, which imparts significant corrosion resistance. It is widely used in construction, automotive, and food processing due to its strength and resistance to oxidation.
Typical Applications:
- Construction: Used in major building support materials due to its strength and flexibility.
- Automotive: Components that require durability and corrosion resistance like exhaust systems and grills.
- Food Processing: Equipment and tools that must resist acids found in meats, milk, fruits, and vegetables. Stainless steel is also prized for its ease of cleaning and minimal contamination risk.
- Medical Instruments: Stainless steel is used extensively in medical settings for surgical instruments, surgical implants, and MRI scanners.
Classic Grades:
- 304 Stainless Steel: The most common form of stainless steel used due to its excellent rust and corrosion resistance. Ideal for kitchen equipment, some chemical equipment, and architectural facades.
- 316 Stainless Steel: Contains molybdenum, enhancing corrosion resistance against chlorides such as sea water and deicing salts. Ideal for marine environments.
Conclusion
While Hastelloy is typically used in more extreme conditions where corrosion resistance at high temperatures is necessary, Stainless Steel is more versatile and commonly used across a variety of everyday applications. Hastelloy is significantly more costly than Stainless Steel, which makes Stainless Steel a more practical choice for less demanding environments. The decision between Hastelloy and Stainless Steel will depend on the specific environmental conditions and economic considerations of the application.
Hastelloy vs Stainless Steel——common form difference
Hastelloy
Hastelloy, a high-performance alloy, primarily comes in the following forms:
- Hastelloy Sheet and Plate: These are commonly used for chemical equipment that requires significant corrosion resistance.
- Hastelloy Pipe and Tubing: Hastelloy pipes and tubes are essential in industries like chemical processing where fluids that corrode lesser materials are handled.
- Hastelloy Bar and Rod: Used to manufacture fasteners and construction components that must withstand acidic environments.
- Hastelloy Wire: Often used in welding applications to join pieces of metal in corrosive environments.
Stainless Steel
Stainless Steel, known for its versatility and strength, is typically available in a wider range of forms suitable for various applications:
- Stainless Steel Sheet and Plate: Widely used in construction, automotive, and appliances for both structural and aesthetic purposes.
- Stainless Steel Pipe and Tube: Essential in both industrial applications (like fluid transport) and in residential settings (like plumbing).
- Stainless Steel Bar, Rod, and Structural Shapes: These forms are used in construction, manufacturing machinery, and automotive frameworks.
- Stainless Steel Wire: Common in everything from cooking utensils to surgical instruments.
Conclusion
While both materials are available in similar forms such as sheets, plates, pipes, and bars, Hastelloy is often specified when corrosion resistance in extreme environments is required, whereas Stainless Steel is chosen for its strength, flexibility, and broader range of applications. Hastelloy’s use in specialized industries such as aerospace and nuclear reactors contrasts with Stainless Steel’s widespread use in construction, automotive, and household applications.
Hastelloy vs Stainless Steel——the difference in appearance
Hastelloy and Stainless Steel, while both are metallic in appearance, have subtle differences in their aesthetic qualities that can be important depending on the application.
Hastelloy
- Color: Hastelloy generally has a duller, grayish hue compared to stainless steel. This coloration can vary slightly depending on the specific alloy and surface finish.
- Finish: It typically has a matte finish when left in its natural state. However, it can be polished to achieve a shinier appearance, although this is less common due to its industrial applications where aesthetics are often secondary.
- Surface Consistency: Hastelloy may exhibit more surface irregularities due to its high nickel content and the specific conditions under which it is processed and used.
Stainless Steel
1. No.1 Finish
- Process: This surface is achieved through hot rolling, followed by annealing and pickling.
- Characteristics: It appears rough and matte. It is the basic surface finish obtained after initial processing, generally used in industrial settings and not suitable for decorative applications.
- Applications: Typically used in areas where aesthetics are not a concern, such as chemical equipment and pressure vessels.
2. 2B Finish
- Process: After hot rolling and annealing, the steel is lightly cold rolled using polished rolls and then pickled.
- Characteristics: Smoother than No.1 with a certain level of gloss, but not mirror-like. The 2B surface is the most common cold-rolled product finish.
- Applications: Widely used for general stainless steel products such as kitchen equipment, furniture, and architectural decorations.
3. BA (Bright Annealed)
- Process: Annealed under controlled atmosphere to achieve a highly bright and reflective surface.
- Characteristics: BA surfaces are brighter and smoother than 2B, almost mirror-like in their reflectivity.
- Applications: Suitable for applications requiring excellent visual effects, such as cookware, decorative panels, and casings for electronic devices.
4. 8K Mirror
- Process: The surface is polished repeatedly to achieve an extremely high level of finish and reflectivity.
- Characteristics: Also known as mirror polish, it can reflect images very clearly and is the highest grade of stainless steel surface finish.
- Applications: Commonly used in places requiring very high decorative effects, such as luxury hotel lobbies, building decorations, and some high-end furniture or art pieces.
conclusion
Hastelloy and Stainless Steel each offer unique benefits, tailored for specific environmental and application needs:
Chemical Composition and Properties: Hastelloy is superior in resisting corrosion in harsh environments, especially where chemicals are involved, due to its nickel-based composition. Stainless Steel, with its iron and chromium base, offers a good balance of durability and resistance for broader applications.
Applications: Hastelloy is the go-to for extreme conditions such as chemical processing and aerospace due to its robustness against corrosion and high temperatures. Stainless Steel, being more cost-effective, is widely used in construction, automotive, and culinary fields.
Form and Appearance: Both materials come in various forms, but Stainless Steel is often chosen for visible applications due to its aesthetically pleasing finish.
In essence, the choice between Hastelloy and Stainless Steel depends on the specific requirements of corrosion resistance, mechanical properties, cost, and aesthetics. Stainless Steel serves a broader range of less demanding environments, making it a versatile and economical choice, while Hastelloy is tailored for high-performance in aggressive environments.
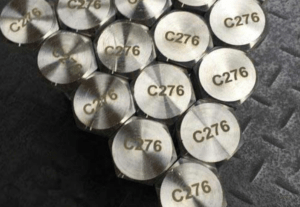
Hastelloy C-276 belongs to nickel-molybdenum-chromium-iron-tungsten nickel-based alloy, which is one of the most corrosion-resistant modern metal materials.
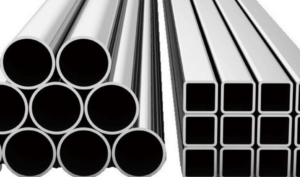
Hastelloy X is a nickel-based superalloy known for its exceptional high-temperature strength and oxidation resistance.
Inconel is a family of nickel-chromium-based superalloys known for their exceptional resistance to oxidation, corrosion, and high temperatures. These alloys maintain their strength and stability at temperatures where most metals would degrade. Common grades include Inconel 600, 625, 718, and X750, each tailored for specific high-performance applications.
Yes, Inconel is generally stronger than many types of steel, especially at elevated temperatures. Inconel alloys maintain their mechanical strength and resistance to thermal creep deformation far better than most steels. This makes Inconel ideal for high-temperature and high-stress environments where steel would weaken and fail.
Inconel is a superalloy primarily composed of nickel and chromium. It belongs to a category of materials known as high-performance alloys, which are engineered to withstand extreme conditions, including high temperatures, corrosion, and oxidation. Inconel alloys also contain other elements such as molybdenum, iron, cobalt, and niobium, which enhance their specific properties.
Inconel is used in a variety of applications that demand high strength and resistance to extreme environments:
- Aerospace: Jet engines, turbine blades, and spacecraft components.
- Chemical Processing: Heat exchangers, reactors, and piping systems.
- Power Generation: Nuclear reactors, superheater and reheater tubes.
- Marine Engineering: Offshore oil and gas extraction, shipbuilding.
- Automotive: High-performance exhaust systems and turbochargers.
- Environmental Control: Pollution control equipment, desalination plants.
- Medical: Certain medical devices and surgical instruments.
Inconel is expensive due to several factors:
- Material Composition: The primary elements, nickel and chromium, are costly, and additional alloying elements like molybdenum and niobium further increase the cost.
- Manufacturing Complexity: Inconel requires specialized manufacturing processes, including advanced melting, casting, and machining techniques, which are more complex and expensive than those for common metals.
- Performance Characteristics: Its exceptional properties, such as high-temperature strength, corrosion resistance, and durability, justify the higher cost for critical applications.
Inconel and titanium each have strengths in different areas:
- High-Temperature Performance: Inconel is stronger and more stable at high temperatures, making it superior for applications involving extreme heat.
- Weight: Titanium is much lighter than Inconel, which is advantageous in aerospace and automotive applications where weight savings are crucial.
- Corrosion Resistance: Both materials offer excellent corrosion resistance, but Inconel is often preferred in highly corrosive environments and at higher temperatures.
- Strength-to-Weight Ratio: Titanium has a better strength-to-weight ratio, making it suitable for applications where both strength and lightness are required.