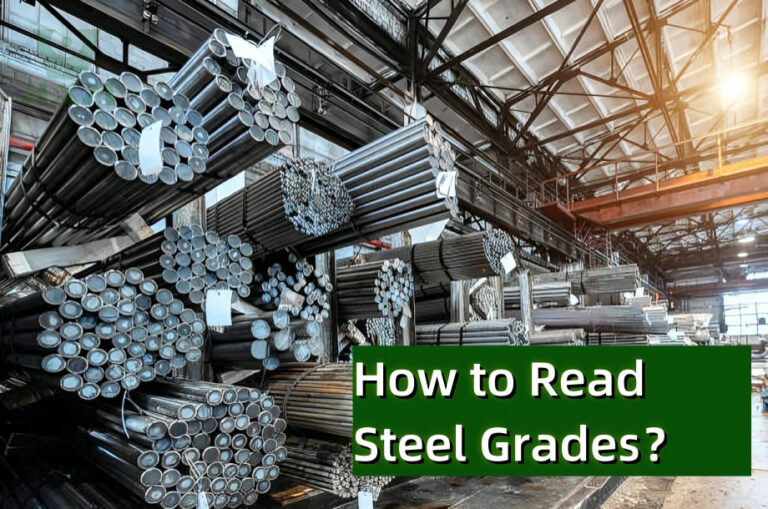
Steel grades are the backbone of material selection in engineering, construction, and manufacturing. Understanding how steel is graded allows businesses to make informed decisions regarding quality, performance, and cost efficiency.
In this article, we will explore:
- What steel grading systems are and why they exist
- The four main types of steel
- Steel classifications and numbering systems
- How major systems like ASTM, AISI/SAE work
Why Do Steel Grade Standards Exist?
Steel grade standards ensure consistency, quality, and suitability for specific applications. Without these standards, manufacturers and industries could face significant variability in performance, leading to failure in critical operations.
The Four Types of Steel
Steel is classified into four primary categories based on composition and properties:
Carbon Steel: The most common, containing carbon as the primary alloying element.
- Examples: Mild steel, medium-carbon steel, high-carbon steel.
Alloy Steel: Includes other elements like chromium, molybdenum, or nickel for enhanced performance.
- Application: Automotive, pipelines.
Stainless Steel: Contains chromium (≥10.5%) for corrosion resistance.
- Types: Austenitic, ferritic, martensitic.
Tool Steel: Designed for high hardness and durability.
- Applications: Cutting tools, molds.
Steel Classifications and Numbering Systems
A. ASTM Steel Grading System
The ASTM (American Society for Testing and Materials) system classifies steel by its application and characteristics.
- Example: ASTM A36 – Standard for structural steel.
B. AISI/SAE Numbering System
The AISI (American Iron and Steel Institute) and SAE (Society of Automotive Engineers) use a numeric code to denote the steel type.
- Structure: Four digits.
- Example: 1018 (Plain carbon steel).
- 10: Carbon steel; 18: Carbon content (0.18%).
C. Carbon Steel Numbering
Carbon steels are often categorized based on their carbon content:
- Low-carbon steel: 0.05–0.25% carbon (e.g., AISI 1018).
- Medium-carbon steel: 0.25–0.6% carbon (e.g., AISI 1045).
- High-carbon steel: 0.6–1.0% carbon.
D. Other International Standards
- EN Standards (Europe): EN 10025 for structural steel.
- JIS (Japan): JIS G3101 for general-purpose steel.
- GB (China): GB/T standards.
Understanding the Steel Numbering System
The AISI numbering system uses four key digits:
- The first two digits indicate the steel type.
- The last two digits indicate carbon content percentage.
Steel Number | Type | Carbon Content |
---|---|---|
1018 | Plain Carbon Steel | 0.18% |
4140 | Alloy Steel | 0.40% |
304 | Stainless Steel | 18% Chromium |
How the ASTM Grading System Works
ASTM categorizes steel based on its intended use:
- A: Structural steel (e.g., ASTM A36).
- F: Fasteners and bolts (e.g., ASTM F1554).
- C: Castings (e.g., ASTM C131).
Each category has unique performance benchmarks like tensile strength, yield strength, and corrosion resistance.
Tips to Easily Identify Steel Grades
- Use Steel Grade Charts: Refer to standardized charts to understand numbering systems.
- Check Markings: Manufacturers mark steel plates and sheets with relevant grade codes.
- Chemical Analysis: Use spectrometry tools for accurate grade identification.
- Verify Documentation: Material certificates provide essential details.
Conclusion
Understanding steel grading systems like ASTM, AISI/SAE, and others is critical for material selection. By decoding steel numbers, classifications, and chemical compositions, businesses can ensure they select the best steel for their needs.
Need expert advice on selecting the right steel grade? Contact us today to find tailored solutions for your projects.
Steel classification uses standardized systems to identify the composition, strength, and application of steel. The most common systems are:
SAE/AISI (U.S.):
- A 4-digit code (e.g., 1018, 4140).
- First two digits: Type of steel and alloying elements.
- Last two digits: Carbon content in hundredths of a percent.
- Example: 4140 → Alloy steel with 0.40% carbon content.
- A 4-digit code (e.g., 1018, 4140).
EN (European Standard):
- Uses descriptive symbols (e.g., S235, X5CrNi18-10).
- S: Structural steel; the number refers to yield strength (S235 = 235 MPa).
- X: Stainless steel; chemical composition is included.
- Uses descriptive symbols (e.g., S235, X5CrNi18-10).
GB (Chinese Standard):
- Designates steel with codes like Q235 (Q = yield strength, 235 MPa).
JIS (Japanese Standard):
- Codes like SUS304, where SUS indicates stainless steel.
Steel ratings describe the material’s performance based on mechanical and chemical properties:
Mechanical Ratings:
- Tensile Strength: Maximum stress steel can endure.
- Yield Strength: Stress at which permanent deformation occurs.
- Example: ASTM A36 → Yield strength 250 MPa.
Chemical Ratings:
- Describes alloy composition, such as carbon, manganese, chromium, or nickel content.
Classification Codes:
- AISI/SAE: 1020, 4140, etc.
- EN Standard: S275JR (structural), X5CrNi18-10 (stainless).
Ratings are often found in product datasheets or specifications for comparison.
To identify the grade of steel:
Check Markings:
- Most steel products have stamped markings with their grade (e.g., 304, 4140, S355).
Conduct Tests:
- Spark Test: Sparks differ for carbon and alloy steels.
- Chemical Analysis: Use spectroscopy or XRF (X-ray fluorescence) devices to determine the composition.
- Magnetic Test: Helps differentiate between stainless and carbon steels.
Review Documentation:
- Check mill certificates, product datasheets, or purchase orders that specify the grade.
Steel is commonly divided into three primary grades based on composition and use:
Carbon Steel:
- Contains primarily carbon with trace elements.
- Subtypes:
- Low Carbon Steel (Mild Steel): Up to 0.3% carbon (e.g., A36).
- Medium Carbon Steel: 0.3–0.6% carbon (e.g., 1045).
- High Carbon Steel: Above 0.6% carbon (e.g., 1095).
Alloy Steel:
- Contains additional alloying elements like chromium, molybdenum, and nickel to enhance strength or corrosion resistance.
- Example: 4140 (chromium-molybdenum steel).
Stainless Steel:
- Contains at least 10.5% chromium for corrosion resistance.
- Subtypes: Austenitic (e.g., 304), Ferritic (e.g., 430), Martensitic (e.g., 420).
Steel is classified into four main types based on composition:
Carbon Steel:
- Contains carbon as the main alloying element.
- Used in construction, pipelines, and automotive parts.
Alloy Steel:
- Contains elements like manganese, silicon, nickel, and molybdenum to improve mechanical properties.
- Example: 4340 (nickel-chromium-molybdenum steel).
Stainless Steel:
- High chromium content for corrosion resistance.
- Applications: Food processing, medical equipment, and construction.
Tool Steel:
- Designed for hardness and wear resistance.
- Applications: Cutting tools, dies, and molds.
4140 steel is a versatile, chromium-molybdenum alloy steel known for its strength, toughness, and wear resistance.
Key Properties:
- Chemical Composition:
- Carbon (0.38–0.43%), Chromium (0.8–1.1%), Molybdenum (0.15–0.25%).
- Mechanical Properties:
- Tensile Strength: 655–850 MPa.
- Yield Strength: 415–600 MPa.
- Applications:
- Gears, shafts, axles, tooling, and industrial machinery.
4140 steel combines hardness and toughness, making it ideal for high-stress applications.
Recent Blog
If you found this article good, feel free to share it on your other social media platforms.
Due to its excellent resistance to sulfuric acid and other acidic environments, Alloy 20 is commonly used in chemical processing equipment, such as heat exchangers, condensers, and piping systems. It is also employed in the production of sulfuric acid, fertilizer manufacturing, and waste treatment plants. Alloy 20’s versatility and durability make it a popular choice for various industrial applications.
Hastelloy alloys, on the other hand, are frequently used in more demanding applications where extreme corrosion resistance is required. They are commonly found in chemical processing plants, petrochemical facilities, and power generation stations. Hastelloy alloys are also used in the production of pharmaceuticals, where their resistance to aggressive chemicals is crucial. Additionally, they are employed in marine environments due to their excellent resistance to seawater corrosion.