Hastelloy alloys, a class of high-performance nickel-based alloys, play a pivotal role in numerous industries due to their exceptional corrosion resistance and high-temperature strength. To ensure the superior performance of Hastelloy alloys, the metallurgical processes, encompassing melting, casting, heat treatment, machining, cold working, and finishing, must be meticulously executed. In this article, we will take a closer look at the optimization of manufacturing processes for Hastelloy alloys.
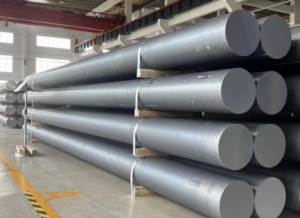
Optimization of Manufacturing Processes for Hastelloy Alloys:
Firstly, in the melting process, the utilization of electric arc furnaces, non-vacuum induction furnaces, or vacuum induction furnaces for melting Hastelloy alloys effectively eliminates impurities such as sulfur and phosphorus, while preventing oxidation of non-metallic inclusions in the alloy. This ensures the uniformity of the alloy’s microstructure and stability of its properties.
Secondly, the casting process involves pouring the molten alloy into casting cavities tailored to the shape of the component, allowing it to cool and solidify into an alloy ingot. This method is highly versatile, virtually unconstrained by the complexity of part geometry, enabling the production of various shapes and sizes of component blanks.
Furthermore, the heat treatment process is crucial in alloy manufacturing, as it significantly enhances the alloy’s properties, enabling it to better withstand diverse and challenging operating environments. One key heat treatment is quenching, which removes residual stresses within the Hastelloy alloy and enhances its strength and corrosion resistance.
Additionally, in the machining process, mechanical processing involves shaping and sizing workpieces through cutting, grinding, or other methods, applicable to various alloy materials. In the case of Hastelloy alloys, forging, rolling, and extrusion are among the mechanical processing techniques employed to adjust the alloy’s dimensions, shape, and properties, meeting specific application requirements.
Furthermore, in the cold working process, which is a common method in metal processing, it primarily aims to alter the microstructure and properties of metallic materials. Cold working of Hastelloy alloys encompasses cold rolling, cold drawing, cold forging, stamping, and cold extrusion. These processes not only achieve the desired dimensions and shapes but also enhance the workpiece’s hardness and strength.
Lastly, in the finishing process, it is an integral part of alloy processing. Further refining Hastelloy alloy materials post-cold working, through operations such as turning, milling, and drilling, not only elevates product quality and performance but also meets stricter application demands. Particularly in high-precision workpiece manufacturing, the role of finishing is paramount.
Summary
In summary, meticulous control over the melting, casting, heat treatment, machining, cold working, and finishing processes in the manufacturing of Hastelloy alloys ensures their superior performance and reliability. Moreover, subsequent treatments like spraying, coating, and passivation can further cater to heightened performance requirements.
Why Choose Huaxiao Alloy?
Thank you for reading our article and we hope it can help you to have a better understanding of the optimization of manufacturing processes for Hastelloy alloys. If you are looking for suppliers and manufacturers of Hastelloy alloys, we would advise you to visit Huaxiao Alloy.
As a leading supplier of Hastelloy alloys, Huaxia Alloy offers customers high-quality Hastelloy C22, Hastelloy C-276, and Hastelloy X at a very competitive price.