Friction and wear are ubiquitous phenomena, and in practical applications, factors such as the selection of spray materials, the hardness of the coating, the compatibility of coating materials, and the preparation methods significantly impact the wear resistance of alloys. Consequently, to prolong the service life of Incoloy alloys in environments subject to wear and corrosion, implementing necessary wear-resistant coating treatments is imperative. In this article, let’s take a closer look at the wear-resistant coating technologies for Incoloy alloys.
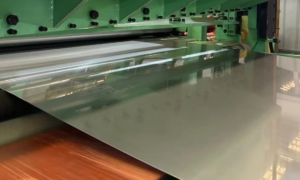
Analysis of Wear-Resistant Coating Technologies for Incoloy Alloys:
Firstly, regarding the selection of spray materials, since Incoloy alloys find extensive applications in fields such as petroleum, chemicals, and marine engineering, the chosen spray materials must not only exhibit excellent wear resistance but also robust corrosion resistance. This necessitates the selection of different spray materials based on the specific wear-resistant coating application environments. For instance, in marine engineering, coatings containing chromium carbide are commonly used on Incoloy alloys to enhance both wear and corrosion resistance.
Secondly, the hardness of the coating plays a pivotal role in enhancing the wear resistance of Incoloy alloys. Especially in high-load operating scenarios, a sufficiently hard wear-resistant coating ensures that the supporting layer on the Incoloy alloy surface resists wear deformation upon external impact and friction, thereby providing effective protection.
Furthermore, the compatibility between coating materials is crucial. Incoloy alloys inherently possess outstanding wear and corrosion resistance, necessitating that the matching coating exhibit similar properties to the substrate material. Only by ensuring compatibility can sufficient bond strength be achieved between the wear-resistant coating and the Incoloy alloy, preventing the coating from detaching due to increased tensile stress within, thus preserving the alloy’s service life.
Additionally, in terms of coating preparation methods, Incoloy alloys commonly employ thermal spraying, physical vapor deposition (PVD), and chemical vapor deposition (CVD). While PVD and CVD methods can produce thinner, more uniform coatings with stronger adhesion, they involve higher equipment and process costs. In contrast, thermal spraying is relatively simple to operate and cost-effective, demonstrating good adhesion between the coating and the metal, making it the most commonly used coating preparation method for Incoloy alloys.
Summary
In summary, wear-resistant coating technologies for Incoloy alloys, by effectively enhancing their corrosion and wear resistance, hold vast potential for industrial applications. Given that factors such as temperature, load, and friction media can impact coating performance, a comprehensive consideration of multiple factors during the application process is essential to achieve optimal wear resistance outcomes.
Why Choose Huaxiao Alloy?
Thank you for reading our article and we hope it can help you to have a better understanding of the wear-resistant coating technologies for Incoloy alloys. If you are looking for suppliers and manufacturers of Incoloy alloys, we would advise you to visit Huaxiao Alloy.
As a leading supplier of Incoloy alloys from Shanghai China, Huaxiao Alloy offers customers high-quality Incoloy 800/800H/800HT, Incoloy 825, and Incoloy 925/926(AL-6XN) at a very competitive price.