What is GH903?
- August 16, 2024
- 1:13 am
- 1188
GH903 is a high temperature alloy with a base composition containing nickel, iron and cobalt, strengthened by precipitation of titanium, niobium and aluminium. The alloy has a low coefficient of thermal expansion over a wide temperature range and an almost constant modulus of elasticity.
GH903 alloy possesses high strength, good thermal fatigue properties, excellent weldability, and resistance to high pressure hydrogen embrittlement. It is suitable for the manufacture of a wide range of components such as turbine magazines and sealing rings for aviation and aerospace engines operating below 650°C, and is one of the most important materials for the realisation of engine gap control technology. The main products offered by this alloy include rods and rings.
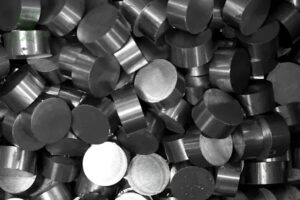
Advantages of GH903
1.Low Coefficient of Thermal Expansion and Constant Modulus of Elasticity
- GH903 has a low coefficient of thermal expansion and nearly constant modulus of elasticity over a wide temperature range, which allows it to remain dimensionally stable in high temperature environments.
2.High strength and fatigue resistance
- GH903 alloy has high strength and excellent resistance to hot and cold fatigue, which makes it suitable for application scenarios where it is required to withstand prolonged periods of high temperatures and cyclical stress changes.
3.Good weldability and resistance to high-pressure hydrogen embrittlement
- GH903 alloy has good weldability and strong resistance to high-pressure hydrogen embrittlement, which is particularly important in the manufacture of aero-engine components, gas turbine components and so on.
4.Corrosion resistance
- GH903 alloy also exhibits good resistance to seawater corrosion, which makes it ideal for fasteners.
Applications of GH903
- Turbine magazines, turbine outer rings, guide inner and outer rings, and sealing rings are made for aviation and aerospace engines. These components operate at extremely high temperatures and therefore require high strength, thermal fatigue and resistance to high-pressure hydrogen embrittlement, which GH903 alloy not only meets, but also has good weldability, making it one of the most important materials for the implementation of engine gap control technology.
- In addition, GH903 alloy is also used in the manufacture of rods and rings, which are mainly used in aero-engine turbine magazines and sealing rings and other components. These applications ensure the stability and reliability of engines in operating environments below 650°C.
What is the future development trend of GH903 alloy?
- With the increasing demand for high-performance materials in modern industry, especially the rising demand for high-temperature alloys in military aviation engines and other fields, GH903 alloy, as one of the important materials, has a broad market prospect. In addition, the continuous emergence of new high-temperature alloy materials will also promote the further development and application of GH903 alloy.
- However, it should be noted that the mechanical properties of GH903 alloy in practical application are not only affected by the material itself, but also by the processing technology, heat treatment state and other factors. Therefore, the future development trend also includes optimising these factors to improve the overall performance and applicability of the alloy.
Alloy 903 is a nickel-based superalloy known for its excellent high-temperature strength and corrosion resistance. It is primarily composed of nickel, cobalt, and iron, with additions of niobium, titanium, and aluminum. Alloy 903 is commonly used in aerospace applications, particularly in gas turbine engines, due to its ability to maintain mechanical properties at elevated temperatures.
The toughest alloy in the world is often considered to be tungsten carbide, a composite material made of tungsten and carbon atoms. It has an extremely high hardness and can withstand very high temperatures, making it ideal for cutting tools, mining equipment, and other applications requiring exceptional toughness.
The strongest superalloy is typically considered to be Inconel 718. This nickel-chromium alloy is renowned for its high strength, toughness, and resistance to corrosion and oxidation at elevated temperatures. It is widely used in aerospace, especially in jet engines, gas turbines, and other high-temperature, high-stress environments.
The strongest fictional alloy is often considered to be Adamantium. In the Marvel Comics universe, Adamantium is an indestructible metal alloy famously bonded to Wolverine’s skeleton. While fictional, it is depicted as one of the hardest substances known, capable of withstanding immense force and damage.
The closest real-life equivalent to Adamantium might be titanium alloys. While not indestructible, titanium alloys offer an excellent combination of high strength, light weight, and corrosion resistance. They are widely used in aerospace, military, and medical applications where these properties are crucial.
The closest real-life metal to Vibranium might be graphene. While not a metal, graphene is a single layer of carbon atoms arranged in a hexagonal lattice, and it possesses incredible strength, electrical conductivity, and flexibility. Although it doesn’t absorb vibrations like Vibranium in the Marvel universe, graphene is one of the strongest materials known and has potential for a wide range of advanced technological applications.
Recent Blog
If you found this article good, feel free to share it on your other social media platforms.