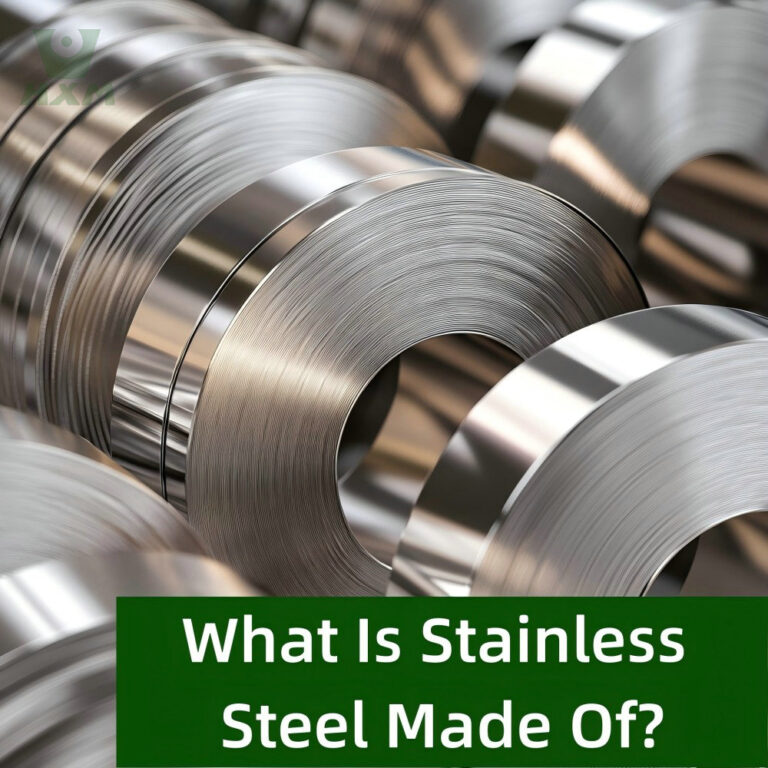
Stainless steel is one of the most widely used materials in industries ranging from construction to healthcare. Its unique blend of strength, corrosion resistance, and aesthetic appeal makes it indispensable. But what exactly is stainless steel made of, and how does it achieve these properties? In this article, we dive deep into its composition, manufacturing process, types, and applications.
The Basic Composition of Stainless Steel
Stainless steel is an iron-based alloy containing a minimum of 10.5% chromium, along with other elements like carbon, nickel, molybdenum, and nitrogen. These components work synergistically to deliver its signature corrosion resistance and durability.
Key Elements in Stainless Steel:
Iron (Fe)
- The base metal (50–85% of the alloy), providing structural integrity.
Chromium (Cr)
- 10.5–30%: Forms a passive oxide layer (Cr₂O₃) that prevents rust and corrosion. Higher chromium content enhances resistance.
Carbon (C)
- 0.03–1.2%: Increases hardness and strength but reduces ductility. Low-carbon grades (e.g., 304L) resist sensitization (chromium carbide formation).
Nickel (Ni)
- 0–20%: Stabilizes austenitic structures, improves formability, and enhances resistance to acids and high temperatures.
Molybdenum (Mo)
- 0–7%: Boosts resistance to pitting and crevice corrosion in chloride-rich environments (e.g., marine applications).
Other Alloying Elements
- Manganese (Mn): Enhances workability.
- Nitrogen (N): Strengthens austenitic steels.
- Silicon (Si): Improves oxidation resistance.
How Stainless Steel Is Made: The Manufacturing Process
Step 1: Raw Material Preparation
- Scrap recycling: Up to 90% of stainless steel is recycled, reducing environmental impact.
- Iron ore processing: Iron is extracted and refined into molten iron.
Step 2: Melting and Alloying
- Electric Arc Furnace (EAF): Scrap and raw materials are melted at 1,600–1,700°C.
- Argon Oxygen Decarburization (AOD): Reduces carbon content and adjusts alloy ratios.
Step 3: Forming
- Casting: Molten steel is poured into slabs, billets, or blooms.
- Hot Rolling: Heated to 1,200°C and rolled into sheets, bars, or coils.
- Cold Rolling: Thinner gauges are achieved at room temperature for precision.
Step 4: Heat Treatment
- Annealing: Heated and rapidly cooled to relieve stress and enhance corrosion resistance.
- Quenching and Tempering: Used for martensitic steels to optimize hardness.
Step 5: Surface Finishing
- Pickling: Acid bath removes oxide scales.
- Polishing/Buffing: Enhances aesthetics and smoothness.
Types of Stainless Steel and Their Compositions
Stainless steel is categorized into five families based on microstructure:
3.1 Austenitic Stainless Steel (e.g., 304, 316)
- Composition: 16–26% Cr, 6–22% Ni, low carbon.
- Properties: Non-magnetic, excellent formability, and corrosion resistance.
- Applications: Kitchenware, chemical tanks, architecture.
3.2 Ferritic Stainless Steel (e.g., 430, 446)
- Composition: 10.5–30% Cr, low/no Ni, higher carbon.
- Properties: Magnetic, moderate corrosion resistance, affordable.
- Applications: Automotive exhausts, industrial machinery.
3.3 Martensitic Stainless Steel (e.g., 410, 420)
- Composition: 11–17% Cr, 0.1–1.2% C, no Ni.
- Properties: High strength, wear resistance, magnetic.
- Applications: Cutlery, turbine blades, surgical tools.
3.4 Duplex Stainless Steel (e.g., 2205)
- Composition: 19–28% Cr, 4–7% Ni, 2–3% Mo.
- Properties: Combines austenitic and ferritic strengths; high chloride resistance.
- Applications: Oil pipelines, desalination plants.
3.5 Precipitation-Hardening (PH) Stainless Steel (e.g., 17-4PH)
- Composition: 15–17% Cr, 3–5% Ni, added Cu/Nb.
- Properties: Ultra-high strength via heat aging.
- Applications: Aerospace components, nuclear reactors.
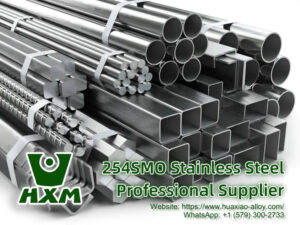
Huaxiao-Alloy: Premium 254SMO stainless steel manufacturer offering sheets, tubes, bars, and custom solutions. Explore specs, applications, and FAQs.
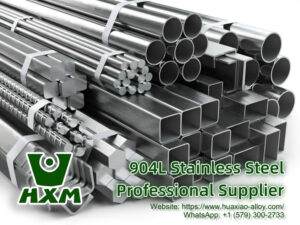
Huaxiao-Alloy: Premium 904L stainless steel manufacturer offering sheets, tubes, bars, and custom solutions. Explore specs, applications, and FAQs.
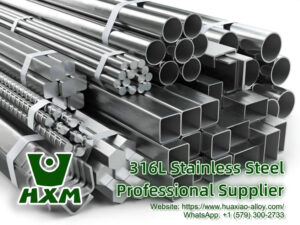
Huaxiao-Alloy: Premium 316L stainless steel manufacturer offering sheets, tubes, bars, and custom fabrication. Explore specs, applications, and FAQs.
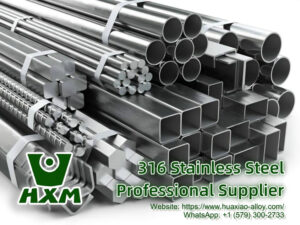
Huaxiao-Alloy: Premium 316 stainless steel manufacturer offering sheets, tubes, bars, and custom fabrication. Explore specs, applications, and FAQs.
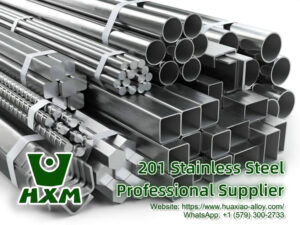
Huaxiao-Alloy: Trusted 201 stainless steel manufacturer offering sheets, coils, bars, and custom fabrication. Explore specs, applications, and FAQs.
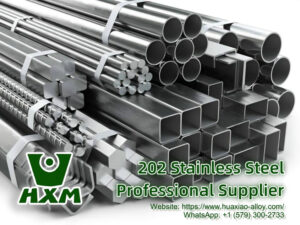
Huaxiao-Alloy: Trusted 202 stainless steel manufacturer offering sheets, coils, bars, and custom solutions. Explore specs, applications, and FAQs.
Why Stainless Steel Is Corrosion-Resistant
The chromium oxide layer is self-healing and forms when chromium reacts with oxygen. This barrier:
- Prevents oxidation (rust) in water and humid environments.
- Resists acids, alkalis, and organic chemicals.
- Repairs itself if scratched, provided sufficient chromium is present.
Factors affecting corrosion resistance:
- Low carbon content (prevents carbide precipitation).
- Molybdenum addition (for chloride resistance).
- Proper surface finish and maintenance.
Applications of Stainless Steel
- Construction: Structural beams, roofing, and facades.
- Medical: Surgical tools, implants (biocompatible grades like 316L).
- Food Industry: Processing equipment (easy to sterilize).
- Energy: Heat exchangers, nuclear reactors.
Pros and Cons of Stainless Steel
Advantages:
- Corrosion resistance.
- High strength-to-weight ratio.
- 100% recyclable.
- Hygienic and easy to clean.
Disadvantages:
- Higher cost than carbon steel.
- Complex welding requirements for some grades.
While highly resistant, it can corrode in extreme conditions (e.g., prolonged exposure to saltwater or acids). Grades with molybdenum (e.g., 316) perform better.
Austenitic grades (304, 316) are generally non-magnetic. Ferritic and martensitic steels are magnetic.
Yes! It’s 100% recyclable without quality loss, making it a sustainable choice.
316 contains 2–3% molybdenum, offering superior chloride resistance.
What Is Stainless Steel Made Of?
Call Us Now!!!