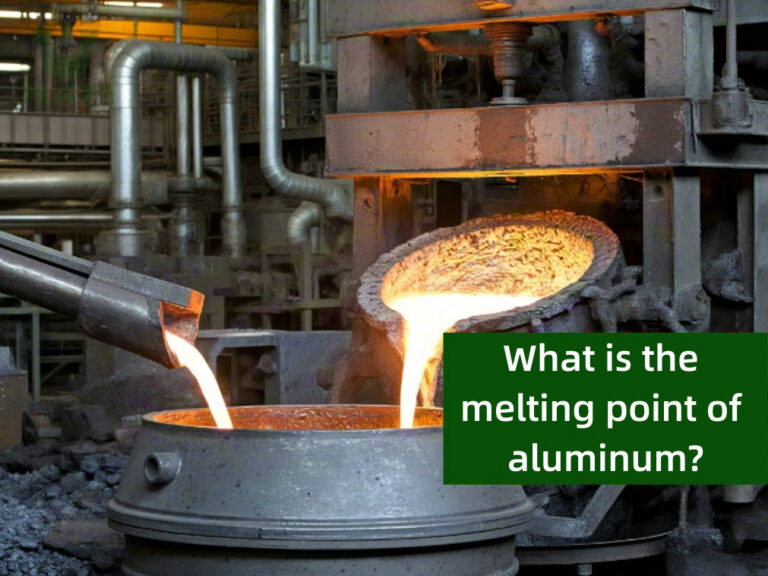
Aluminum is a cornerstone of modern manufacturing, but its usability often depends on understanding its thermal properties. A critical question arises: What is the melting point of aluminum? This article breaks down the science behind aluminum’s melting point, explores how alloying affects it, and explains why Huaxiao-Alloy—a premier aluminum alloy supplier and manufacturer—is the ideal partner for high-temperature applications.
1. The Melting Point of Pure Aluminum - the melting point of aluminum
Defining Melting Point
The melting point is the temperature at which a solid metal transitions to a liquid state. For pure aluminum, this occurs at 660.3°C (1220.5°F) under standard atmospheric pressure. This relatively low melting point (compared to steel or copper) makes aluminum energy-efficient to process while retaining strength in its solid form.
Key Factors Influencing Aluminum’s Melting Behavior
- Purity: 99.996% pure aluminum melts at 660.3°C, but impurities can slightly lower this temperature.
- Pressure: Increased pressure marginally raises the melting point.
- Thermal Conductivity: Aluminum’s high thermal conductivity ensures even heat distribution during melting.
2. How Alloying Elements Affect Aluminum’s Melting Point - the melting point of aluminum
Aluminum alloys—engineered by adding elements like copper, silicon, or magnesium—modify melting behavior to suit specific applications. Below is a comparison of common aluminum alloys and their melting ranges:
Alloy Series | Primary Alloying Elements | Melting Range (°C) | Common Uses |
---|---|---|---|
1xxx | 99%+ Pure Aluminum | 640–660 | Electrical conductors, packaging |
2xxx | Copper | 500–640 | Aerospace structures, automotive parts |
3xxx | Manganese | 630–655 | Heat exchangers, roofing |
5xxx | Magnesium | 570–635 | Marine components, pressure vessels |
6xxx | Magnesium + Silicon | 580–650 | Architectural extrusions, automotive frames |
7xxx | Zinc | 475–640 | Aircraft components, defense systems |
Note: Huaxiao-Alloy specializes in customizing 2xxx, 5xxx, and 7xxx series alloys for high-stress, high-temperature environments.
3. Why Melting Point Matters in Industrial Applications - the melting point of aluminum
Key Industries Leveraging Aluminum’s Thermal Properties
Casting & Foundry:
- Low melting point reduces energy costs for die casting automotive parts or consumer electronics.
- Huaxiao-Alloy supplies A356 (6xxx series) alloys optimized for precision casting.
Aerospace:
- High-strength 2xxx and 7xxx alloys withstand extreme temperatures in jet engines and fuselages.
Welding & Fabrication:
- Aluminum’s narrow melting range requires precise control to avoid defects. Pre-treated alloys from aluminum manufacturers like Huaxiao-Alloy simplify welding processes.
Heat Treatment:
- Solution heat treatment (e.g., T6 temper) enhances strength but demands precise temperature control near the melting point.
Additive Manufacturing:
- Powdered aluminum alloys with tailored melting points enable 3D printing of complex components.
4. Huaxiao-Alloy: Your Expert Partner for Aluminum Solutions
As a global aluminum alloy supplier and manufacturer, Huaxiao-Alloy delivers tailored solutions for industries requiring precise thermal performance. Our capabilities include:
Service | Description |
---|---|
Alloy Customization | Modify melting points and mechanical properties using advanced metallurgy. |
High-Temp Alloys | Develop alloys stable up to 300°C+ for automotive and aerospace sectors. |
Precision Casting | Produce low-porosity components with strict temperature controls. |
Bulk Material Supply | Provide sheets, rods, and extruded profiles in 1xxx to 7xxx series alloys. |
Why Choose Huaxiao-Alloy?
- ISO-Certified Production: Ensure consistency and quality from raw material to final product.
- R&D Expertise: Collaborate with engineers to design alloys for unique thermal challenges.
- Global Reach: Serve OEMs, foundries, and fabricators with fast logistics and technical support.
Yes. House fires typically reach 600–800°C, exceeding aluminum’s melting point (660°C). However, aluminum alloys used in construction (e.g., 6061) have higher thermal resistance.
Adding elements disrupts the atomic lattice structure, reducing the energy required to transition to liquid. For example, 7xxx series (zinc) melts at 475–640°C.
Aluminum’s boiling point is 2519°C (4566°F)—far higher than its melting point. Melting is solid-to-liquid; boiling is liquid-to-gas.
Techniques include differential scanning calorimetry (DSC) and optical pyrometry. Huaxiao-Alloy uses ASTM-certified methods to verify alloy properties.
Huaxiao-Alloy, a leading aluminum supplier, offers alloys engineered for extreme thermal stability. for technical specs and pricing.