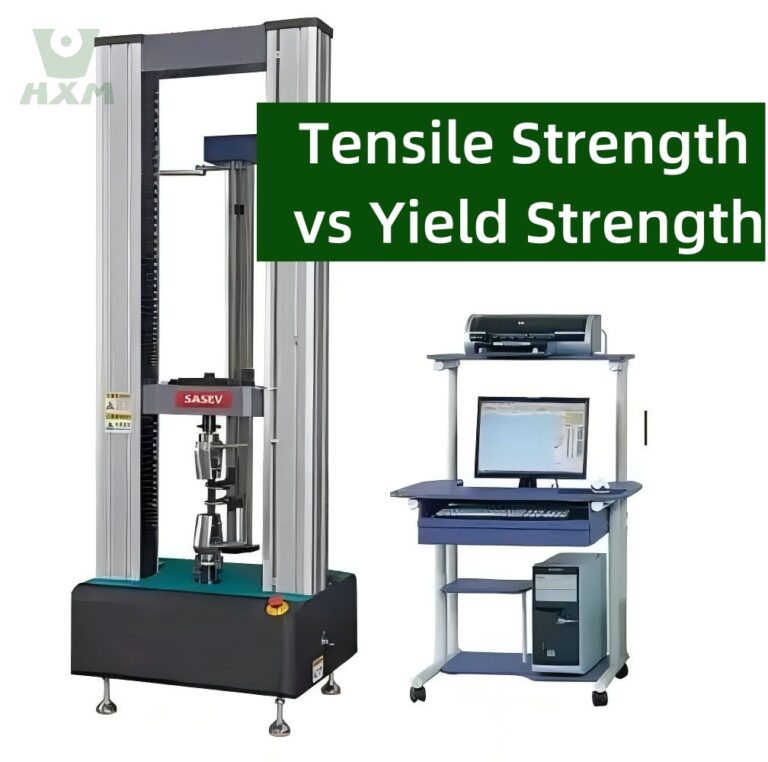
The mechanical properties of steel, such as tensile strength and yield strength, are essential in engineering and material science. These properties dictate how steel behaves under stress, influencing material selection for structural, industrial, and manufacturing applications. This guide provides a deep dive into yield strength and tensile strength, explains their differences, and demonstrates their importance in various steel applications.
Key terms: yield strength of steel, tensile vs yield strength, steel yield point, yield strength vs tensile strength.
Understanding Yield Strength
What is Yield Strength?
Yield strength refers to the stress at which steel transitions from elastic to plastic deformation. In simpler terms, it is the point where the material begins to deform permanently under load.
Key concepts:
- Yield stress of steel: Indicates the stress required to initiate permanent deformation.
- Steel yield strength psi: Commonly expressed in psi (pounds per square inch) or MPa (megapascals).
- Yield strain steel: The strain corresponding to the yield point, often identified on a stress-strain curve.
How is Yield Strength Measured?
- Yield strength is typically measured using a stress-strain curve during tensile testing.
- Engineers often use the 0.2% offset method to determine yield strength (common for materials without a clear yield point).
Yield Strength in Steel
The yield strength of steel varies based on composition and heat treatment:
- Structural steel: ~250 MPa (36,000 psi) for A36 steel.
- Mild steel: ~210 MPa (30,000 psi).
- Carbon steel: 260–400 MPa (38,000–58,000 psi).
- Stainless steel: ~200–290 MPa (29,000–42,000 psi) for austenitic grades like 304.
Applications:
- Yield strength is critical in determining whether a steel component will bend or deform under a given load, especially in construction and structural frameworks.
Exploring Tensile Strength
What is Tensile Strength?
Tensile strength is the maximum stress that steel can withstand while being stretched before breaking. It represents the material’s ultimate load-bearing capacity.
Key concepts:
- Ultimate tensile strength (UTS): The peak stress a material can handle.
- Tensile strength steel: For instance, UTS of mild steel is ~400–550 MPa (58,000–80,000 psi).
- Tensile modulus of steel: A measure of steel’s stiffness during tensile testing.
How is Tensile Strength Measured?
- Tensile strength is determined using a tensile test, where a steel sample is stretched until fracture.
- Stress values are recorded, showing how the material performs under increasing loads.
Tensile Strength in Steel
Tensile strength depends on the steel’s grade and treatment:
- Mild steel: 400–550 MPa (58,000–80,000 psi).
- Carbon steel: Up to 1,200 MPa (174,000 psi).
- Stainless steel: 515–740 MPa (75,000–108,000 psi) for 304 grade.
Applications:
- High tensile strength steels are used in cables, cranes, and load-bearing structures.
Comparing Yield Strength and Tensile Strength
Key Differences
Property | Yield Strength | Tensile Strength |
---|---|---|
Definition | Stress where permanent deformation begins. | Maximum stress steel can withstand before fracture. |
Behavior | Indicates elastic-to-plastic transition. | Indicates ultimate breaking strength. |
Units | MPa or psi. | MPa or psi. |
Relevance | Design safety and structural integrity. | Failure analysis and load capacity. |
Stress-Strain Curve Analysis
The stress-strain curve illustrates:
- Yield point: The start of permanent deformation.
- Ultimate tensile stress: The peak of the curve before fracture.
Yield Stress vs. Tensile Stress
Yield stress reflects material resilience, while tensile stress highlights strength under maximum load. Both are crucial for material selection.
Practical Applications in Steel
Where Yield Strength Matters
- Structural applications: Beams, columns, and supports.
- Mild steel frameworks where deformation limits must not be exceeded.
Where Tensile Strength Matters
- High-stress environments: Suspension cables, bridges, and pressure vessels.
- Situations requiring materials to withstand extreme loads.
Examples of Steel Yield Strength and Tensile Strength
Steel Type | Yield Strength (MPa) | Tensile Strength (MPa) |
---|---|---|
Structural Steel (A36) | 250 | 400–550 |
Carbon Steel | 260–400 | 500–800 |
Stainless Steel (304) | 200–290 | 515–740 |
Conclusion
Understanding yield strength and tensile strength is vital for designing safe and efficient structures. Yield strength ensures steel doesn’t deform under stress, while tensile strength determines the maximum load it can handle.
For high-quality steel and alloy products with precise mechanical properties, trust Huaxiao-Alloy, a professional supplier of alloy metals. We specialize in delivering reliable materials to meet your structural and industrial needs.
Yield strength and tensile strength are two fundamental mechanical properties of materials, especially metals like steel. While both describe how a material behaves under stress, they represent different stages in the material’s response to force.
1. Definition
- Yield Strength: The stress at which a material begins to deform plastically. Below this stress, the material will return to its original shape when the force is removed.
- Tensile Strength: The maximum stress a material can withstand before breaking or failing.
2. Key Characteristics
Property | Yield Strength | Tensile Strength |
---|---|---|
Stress Point | Marks the end of elastic behavior and the start of plastic deformation. | Represents the ultimate load-bearing capacity before fracture. |
Significance | Determines the material’s ability to withstand deformation without permanent damage. | Determines the maximum force a material can endure before breaking. |
Measurement | Found at the yield point on the stress-strain curve. | Found at the peak of the stress-strain curve. |
Behavior | Focuses on the material’s elastic-to-plastic transition. | Focuses on the material’s overall strength and fracture point. |
3. Units
Both yield strength and tensile strength are measured in:
- Megapascals (MPa) in the metric system.
- Pounds per square inch (psi) in the imperial system.
4. Examples in Steel
Steel Type | Yield Strength (MPa) | Tensile Strength (MPa) |
---|---|---|
Structural Steel (A36) | 250 | 400–550 |
Carbon Steel | 260–400 | 500–800 |
Stainless Steel (304) | 200–290 | 515–740 |
5. Practical Implications
Yield Strength:
- Used for designing components that must not permanently deform under load.
- Critical for structural elements like beams, columns, and frames.
Tensile Strength:
- Important for applications requiring materials to withstand maximum stress before failure.
- Relevant in high-stress environments like cables, pressure vessels, and cranes.
6. Stress-Strain Curve
On the stress-strain curve:
- Yield Strength is the point where the curve transitions from linear (elastic) to nonlinear (plastic) behavior.
- Tensile Strength is the peak point of the curve before fracture.
7. Summary
- Yield Strength: Defines the limit for elastic deformation and permanent deformation.
- Tensile Strength: Defines the maximum stress a material can endure before breaking.
Tensile and yield strength are key mechanical properties that are determined through standardized material testing methods. These tests measure a material’s response to tensile (pulling) forces and provide critical data for engineering and design purposes.
1. Tensile Testing Overview
Tensile and yield strength are measured using a tensile test, a fundamental procedure performed on a universal testing machine (UTM). The test involves applying a uniaxial tensile load to a specimen until it fractures.
Key Steps in a Tensile Test:
- Preparation of Test Specimen:
- The specimen is shaped according to standard specifications (e.g., ASTM, ISO) with a uniform gauge section.
- Mounting:
- The specimen is clamped in the machine’s grips.
- Application of Tensile Load:
- A gradually increasing tensile force is applied to stretch the material.
- Data Collection:
- A load cell measures the applied force, while an extensometer measures the elongation of the specimen.
- Stress-Strain Curve:
- Data is used to plot a stress-strain curve, which reveals the material’s mechanical behavior.
2. Measuring Yield Strength
Yield strength is determined from the stress-strain curve as the point where the material transitions from elastic deformation (returns to its original shape) to plastic deformation (permanent change).
Methods to Identify Yield Strength:
Yield Point (Clear Yielding):
- Some materials (e.g., mild steel) show a distinct yield point on the stress-strain curve, where deformation becomes permanent.
0.2% Offset Method:
- For materials without a clear yield point (e.g., stainless steel), the 0.2% offset method is used.
- A line is drawn parallel to the elastic region of the stress-strain curve at 0.2% strain, and the intersection with the curve marks the yield strength.
Units:
- Measured in megapascals (MPa) or pounds per square inch (psi).
3. Measuring Tensile Strength
Tensile strength, also known as ultimate tensile strength (UTS), is determined from the same stress-strain curve. It is the maximum stress a material can withstand before breaking.
How to Determine Tensile Strength:
- Peak Point on the Curve: The highest point on the stress-strain curve represents the tensile strength.
- The material fractures shortly after reaching this point.
Units:
- Measured in megapascals (MPa) or pounds per square inch (psi).
4. Stress-Strain Curve Features
Point | Description |
---|---|
Elastic Region | Linear part of the curve where deformation is reversible. |
Yield Point | Start of plastic deformation; defines yield strength. |
Ultimate Point | Maximum stress before fracture; defines tensile strength. |
Fracture Point | End of the curve where the material breaks. |
5. Testing Standards
Tensile and yield strength measurements follow internationally accepted standards, such as:
- ASTM E8/E8M: Standard Test Methods for Tension Testing of Metallic Materials.
- ISO 6892: Metallic Materials – Tensile Testing.
- JIS Z2241: Method of Tensile Testing for Metallic Materials.
6. Summary
- Yield Strength: Found at the elastic-to-plastic transition, often using the 0.2% offset method.
- Tensile Strength: Determined as the peak stress before the material breaks.
- Both properties are measured through a tensile test and are critical for material selection and engineering design.
Yield strength is a fundamental material property that plays a critical role in engineering and structural design. It determines the maximum stress a material can endure without undergoing permanent deformation. By incorporating yield strength into design calculations, engineers ensure safety, functionality, and long-term reliability of structures and components.
1. Preventing Permanent Deformation
- Definition of Yield Strength: The point at which a material transitions from elastic (temporary deformation) to plastic deformation (permanent deformation).
- In design, yield strength serves as a limit to ensure that components return to their original shape after being subjected to stress, avoiding permanent damage or failure.
Example:
In a steel beam supporting a building, exceeding the yield strength could lead to bending, which compromises structural integrity and safety.
2. Ensuring Structural Safety
- Yield strength acts as a threshold for safe operation under expected loads. It helps designers ensure that structures can handle daily stresses without succumbing to deformation or collapse.
- Safety factors are applied to yield strength to account for uncertainties in material properties, load variations, and environmental conditions.
Applications:
- Bridges: Must support dynamic loads, such as vehicles and wind, without deforming.
- Aircraft: Structural components are designed to resist yielding under extreme flight conditions.
3. Optimizing Material Selection
- Yield strength guides engineers in choosing materials that balance strength and ductility. A material with inadequate yield strength might deform, while one with excessively high yield strength may be brittle and prone to cracking.
- For example:
- Low carbon steel is chosen for applications requiring moderate strength and high ductility.
- High-strength alloy steel is used where higher yield strength is essential.
4. Load-Bearing Capacity
- Yield strength determines the maximum allowable load a structure or component can bear without plastic deformation.
- Designers calculate load capacity based on yield strength, ensuring that the structure performs reliably under operational stresses.
Example:
For a pressure vessel, the yield strength of the steel defines its ability to contain pressurized gases or liquids safely without deformation.
5. Influence on Safety Factors
- Yield strength is used to define safety factors in engineering design. Safety factors are applied to ensure the structure remains well below the yield limit, even under unexpected or extreme loads.
Common Safety Factors:
- Civil engineering: Safety factors of 1.5–3.0.
- Aerospace engineering: Safety factors of 1.2–1.5 due to weight constraints.
6. Long-Term Durability
- Yield strength impacts the material’s resistance to creep, fatigue, and other long-term deformations under sustained or cyclic loading.
- Materials with adequate yield strength ensure the structure performs as intended throughout its service life.
7. Example in Common Materials
Material | Yield Strength (MPa) | Applications |
---|---|---|
Mild Steel | ~210 | Building frameworks, pipelines. |
Stainless Steel (304) | ~200–290 | Kitchen equipment, architectural elements. |
High Carbon Steel | ~500 | Springs, cutting tools. |
Structural Steel (A36) | ~250 | Bridges, buildings, and machinery. |
8. Summary
- Yield strength is critical for ensuring that components and structures can handle applied stresses without permanent deformation.
- It serves as a benchmark for selecting materials, determining load limits, and applying safety factors.
- Incorporating yield strength into design calculations enhances safety, functionality, and longevity of engineering systems.
The tensile strength of steel is the maximum stress it can withstand while being stretched or pulled before breaking. It represents the material’s ultimate load-bearing capacity and is measured in megapascals (MPa) or pounds per square inch (psi).
Typical Tensile Strength Values:
- Mild Steel: 400–550 MPa (58,000–80,000 psi)
- Stainless Steel (304): 515–740 MPa (75,000–108,000 psi)
- High Carbon Steel: 800–1,200 MPa (116,000–174,000 psi)
This property is crucial for applications requiring materials to endure high stress without failing, such as bridges, cranes, and pressure vessels.
The yield strength of steel is the maximum stress it can withstand without permanent deformation. It marks the point where steel transitions from elastic (temporary deformation) to plastic (permanent deformation) behavior.
Typical Yield Strength Values:
- Mild Steel: ~210 MPa (30,000 psi)
- Structural Steel (A36): ~250 MPa (36,000 psi)
- Stainless Steel (304): ~200–290 MPa (29,000–42,000 psi)
Yield strength is crucial in design to ensure structures and components do not deform under expected loads, making it a critical factor in engineering and construction applications.
Yield strength is determined through a tensile test, where a material is subjected to increasing tension until it deforms plastically. The key steps are as follows:
1. Stress-Strain Curve
- A stress-strain curve is generated during the tensile test.
- Stress (force per unit area) and strain (elongation per unit length) are recorded.
2. Identifying Yield Strength
- Clear Yield Point: For materials like mild steel, the yield point is a distinct drop in the curve where plastic deformation begins.
- 0.2% Offset Method: For materials without a clear yield point (e.g., stainless steel), a line is drawn parallel to the elastic region at 0.2% strain. The intersection of this line with the stress-strain curve defines the yield strength.
3. Formula
Yield strength (σyσy) is calculated as:
σy=FAσy=AF
Where:
- FF: Force applied at the yield point (N or lbs).
- AA: Original cross-sectional area of the specimen (m² or in²).
4. Units
- Metric: Megapascals (MPa).
- Imperial: Pounds per square inch (psi).
Summary
Yield strength is calculated using tensile test data and is crucial for determining a material’s ability to resist permanent deformation under load. Let me know if you’d like more detailed examples!