In the realm of metallurgy, the names Inconel 600 and Inconel 601 are synonymous with excellence in corrosion resistance and high-temperature performance. Both alloys belong to the family of nickel-chromium alloys, widely used in various industries due to their unique properties. However, despite their similarities, there are distinct differences between Inconel 600 and Inconel 601 that make each alloy suitable for specific applications.
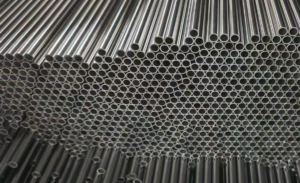
What is the difference between Inconel 600 and Inconel 601?
Let’s delve into the nuances of Inconel 600 and Inconel 601 to understand their individual characteristics and the reasons for their choice in various industrial settings.
Inconel 600, with its primary composition of approximately 77% nickel, 16% chromium, and 6% iron, exhibits remarkable resistance to chloride stress corrosion cracking and corrosion in alkaline solutions. This alloy maintains its high corrosion resistance even in reducing conditions. Its high nickel content contributes significantly to its excellent corrosion resistance, while the chromium content enhances its resistance to oxidation in oxidizing environments. Inconel 600 is renowned for its good hot and cold workability, welding characteristics, and satisfactory thermal strength below 700°C. Its combination of properties makes it a prime choice for applications such as aerospace engine components and the production and handling of corrosive alkalis, especially in sulfide-containing environments.
On the other hand, Inconel 601, with its composition centered around nickel, chromium, and iron, offers a unique set of properties. Its chromium content ranges from 21% to 25%, while iron content is between 10% and 15%. This alloy stands out for its exceptional resistance to oxidation at high temperatures, reaching up to 2200°F. Its ability to form a protective oxide film that resists peeling even under severe thermal cycling conditions makes it a favorite in applications involving repeated heating and cooling cycles. Additionally, Inconel 601 exhibits good mechanical properties at both room and elevated temperatures, making it suitable for a wide range of high-temperature applications.
The difference in chromium content between the two alloys is a key factor in their performance. Inconel 601, with its higher chromium content, exhibits superior oxidation resistance, particularly in sulfur-containing atmospheres. This property, coupled with its good mechanical properties and resistance to stress corrosion cracking, makes it a preferred choice in heat treatment, chemical processing, and other high-temperature environments.
Another notable difference lies in their use in welding and processing. Both alloys can be welded and processed using standard techniques, but Inconel 600 cannot be hardened through heat treatment and relies primarily on cold working for shaping. This characteristic limits its applications to those that do not require hardening through heat treatment.
When it comes to selecting between Inconel 600 and Inconel 601, the choice is often dictated by the specific operating conditions and the nature of the corrosion challenges faced. For instance, in environments where high resistance to chloride stress corrosion cracking and alkaline solutions is paramount, Inconel 600 is often the preferred choice. Its ability to maintain corrosion resistance even in reducing conditions makes it a reliable material for applications involving corrosive alkalis.
On the other hand, Inconel 601’s exceptional oxidation resistance at high temperatures and its ability to withstand severe thermal cycling make it an excellent choice for applications such as heat treatment furnaces, chemical reactors, and other equipment that operates under extreme thermal conditions. Its high chromium content also enhances its resistance to sulfur-containing atmospheres, further expanding its potential use in industries like petrochemical processing.
Conclusion
In summary, both Inconel 600 and Inconel 601 are exceptional alloys with unique properties that make them suitable for different applications. Inconel 600 excels in corrosion resistance, particularly in reducing environments and alkaline solutions, while Inconel 601 stands out for its oxidation resistance at high temperatures and its ability to withstand severe thermal cycling.
Thank you for reading our article and we hope it can help you to have a better understanding of the differences between Inconel 600 and Inconel 601. If you are looking for Inconel suppliers and manufacturers online now, we would advise you to visit Huaxiao Alloy.
As a leading supplier of Inconel Alloys from Shanghai China, Huaxiao Alloy offers customers high-quality Inconel 600, Inconel 601, Inconel 625, and Inconel 718 at a very competitive price.