Hastelloy forgings, as high-performance nickel-based alloy materials, are renowned for their exceptional high-temperature strength and corrosion resistance, making them widely applicable in chemical, petroleum, energy, and other industries. To ensure superior performance and quality of Hastelloy forgings, meticulous attention must be paid to material selection, temperature control, deformation management, and heat treatment during the forging process. In this article, let’s take a closer look at the forging process of corrosion-resistant alloys in Hastelloy.
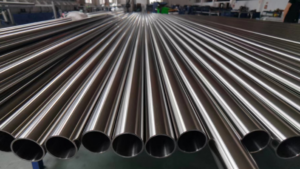
Forging Process of Corrosion-Resistant Alloys in Hastelloy:
Firstly, regarding material selection, Hastelloy boasts a unique chemical composition comprising nickel, chromium, iron, molybdenum, and other alloying elements, which endow it with remarkable corrosion resistance, wear resistance, and oxidation resistance. Given the numerous grades of Hastelloy, each with distinct chemical compositions and performance characteristics, adhering strictly to the technical data and recommendations provided by suppliers is crucial to ensuring the stability and reliability of forging performance.
Secondly, temperature control is a pivotal factor in the forging process. Excessively high temperatures may lead to insufficient metal flow, potentially causing porosity and shrinkage cavities within the metal, resulting in cracks and deformations in the forging. Conversely, insufficient temperatures hinder deformation, causing residual stresses to surge, thereby diminishing the metal’s properties. Therefore, appropriately setting the heating and forging temperature ranges during Hastelloy forging facilitates the achievement of dense forging structures and uniform microstructures, enhancing the forging’s hardness, strength, and wear resistance.
Thirdly, deformation control is essential. Excessive deformation during forging can induce internal defects in the forging, significantly impacting its service life. Conversely, rational deformation control improves the internal microstructure and enhances the forging’s mechanical properties and corrosion resistance. Hastelloy’s excellent workability allows for easy shaping into various forms and sizes. To avoid defects caused by overprocessing, deformation should be carefully controlled based on specific alloy grades and forging requirements.
Furthermore, heat treatment is a crucial step in the Hastelloy forging process. Residual stresses and uneven grain structures often exist within Hastelloy forgings post-forging. Heat treatment eliminates these residual stresses, promotes a more uniform distribution of alloying elements, and refines the grain structure to achieve desired properties. Additionally, it enhances the forging’s hardness, strength, and corrosion resistance, extending its service life.
Conclusion
In conclusion, the importance of the forging process for Hastelloy cannot be overstated. As an economically viable method for material modification, it significantly upgrades alloy performance to meet diverse application demands. Consequently, to ensure optimal quality and performance of Hastelloy forgings, rigorous attention to material selection, temperature control, deformation management, and heat treatment is imperative.
Why Choose Huaxiao Alloy?
Thank you for reading our article and we hope it can help you to have a better understanding of the forging process of corrosion-resistant alloys in Hastelloy. If you are looking for suppliers and manufacturers of Hastelloy alloys, we would advise you to visit Huaxiao Alloy for more information.
As a leading supplier of Hastelloy alloys from Shanghai China, Huaxiao Alloy provides customers with high-quality Hastelloy alloys such as Hastelloy C22, and Hastelloy X at a very competitive price.