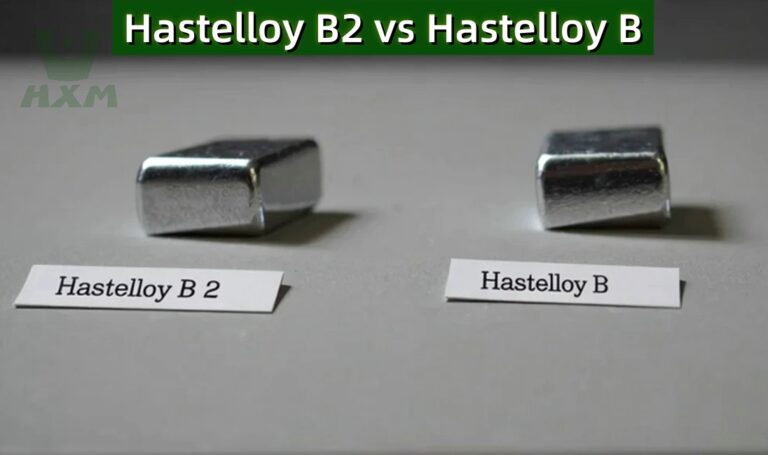
As a seasoned expert in metallic materials from Huaxiao Alloy, with years of experience specializing in Hastelloy and other alloys, I have a profound understanding of the subtleties and nuances that distinguish various metal compositions. In this article, I will delve into the differences between Hastelloy B2 vs Hastelloy B, two alloys that, despite their similarities, possess distinct characteristics that make them suitable for different applications.
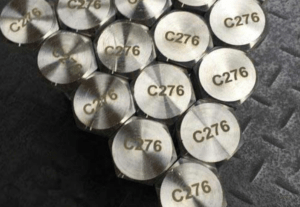
Hastelloy C-276 belongs to nickel-molybdenum-chromium-iron-tungsten nickel-based alloy, which is one of the most corrosion-resistant modern metal materials.
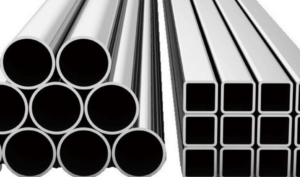
Hastelloy X is a nickel-based superalloy known for its exceptional high-temperature strength and oxidation resistance.
Hastelloy B2 vs Hastelloy B – What’s the Difference?
Hastelloy B2 vs Hastelloy B – Chemical Composition
Firstly, let’s explore the chemical composition of these two alloys. Hastelloy B2 is primarily composed of nickel, molybdenum, and chromium, with minor additions of iron and other elements. The high nickel content contributes to its excellent corrosion resistance, while the molybdenum enhances its resistance to oxidizing acids. On the other hand, Hastelloy B has a similar composition but with a higher iron content, which affects its mechanical properties and corrosion resistance characteristics.
Hastelloy B2 vs Hastelloy B – Corrosion Resistance Properties
The primary difference between these two alloys lies in their corrosion resistance properties. Hastelloy B2 exhibits superior resistance to reducing acids, particularly in high-temperature environments. Its unique composition allows it to withstand corrosive attack from a wide range of acids, including sulfuric acid, hydrochloric acid, and phosphoric acid. This makes Hastelloy B2 an ideal choice for applications in the chemical processing industry, where exposure to harsh chemicals is common.
Hastelloy B, while also exhibiting good corrosion resistance, is particularly known for its resistance to oxidizing acids and mixed acid environments. It performs well in oxidizing conditions, such as those encountered in nitric acid service. However, it may not perform as well as Hastelloy B2 in some reducing acid environments, especially at elevated temperatures.
Hastelloy B2 vs Hastelloy B – Mechanical Properties
When it comes to mechanical properties, both Hastelloy B2 and Hastelloy B offer excellent strength and ductility. However, the higher iron content in Hastelloy B can affect its mechanical properties, making it slightly less ductile than Hastelloy B2. This difference is generally not significant for most applications, but it can be a factor in choosing the right alloy for specific use cases.
Hastelloy B2 vs Hastelloy B – Fabrication and Welding Characteristics
The fabrication and welding characteristics of these alloys also deserve mention. Both Hastelloy B2 and Hastelloy B can be welded using conventional methods, such as gas tungsten arc welding (GTAW) and gas metal arc welding (GMAW). However, it is essential to follow the recommended welding procedures and use appropriate filler metals to ensure sound welds. The welding of Hastelloy alloys requires special attention to minimize the risk of cracking and ensure the desired corrosion resistance of the welded joint.
Hastelloy B2 vs Hastelloy B – Cost
Another critical aspect to consider is the cost of these alloys. Hastelloy B2, due to its superior corrosion resistance in certain environments, often commands a higher price than Hastelloy B. The choice between the two alloys often involves a cost-benefit analysis, considering the specific requirements of the application and the long-term durability and performance of the material.
Hastelloy B2 vs Hastelloy B – Applications
In terms of applications, Hastelloy B2 finds widespread use in the chemical processing industry, particularly in equipment that handles corrosive acids and other harsh chemicals. Its excellent corrosion resistance and high-temperature stability make it suitable for use in reactors, heat exchangers, and other equipment exposed to demanding environments.
Hastelloy B, on the other hand, is often used in applications where oxidizing acids are a concern. It is commonly found in nitric acid production facilities, waste treatment plants, and other industries where oxidizing conditions are prevalent. Its ability to resist corrosion in these environments makes it a reliable choice for critical components.
Can the naked eye distinguish between Hastelloy B2 and Hastelloy B?
It is generally difficult to distinguish Hastelloy B2 from Hastelloy B with the naked eye, especially if their surfaces are untreated or not visibly marked. Both alloys have very similar appearances, with a metallic sheen and a grey to silver-white color.
However, despite their similar appearance, the main differences between them lie in their composition and performance:
- Hastelloy B2 is an improved version of Hastelloy B. It differs in the content of iron and other trace elements, making B2 more stable and offering better oxidation resistance at high temperatures.
- Hastelloy B (often referring to the earlier B1 version) contains higher iron and lower carbon, and it may offer slightly less resistance to certain corrosive environments compared to B2.
To reliably distinguish between these two materials, the best approach is to use chemical composition analysis (such as X-ray fluorescence or spectrographic analysis) or refer to the material certification documents. These methods can precisely determine the alloy composition and clearly identify the difference between the two.
Why Choose Huaxiao Alloy?
In conclusion, Hastelloy B2 and Hastelloy B are both excellent alloys with distinct characteristics that make them suitable for different applications. Hastelloy B2 excels in resisting reducing acids and high-temperature environments, while Hastelloy B demonstrates superior resistance to oxidizing acids.
Thank you for reading our article and we hope it can help you to have a better understanding of the differences between Hastelloy B2 vs Hastelloy B. If you are looking for Hastelloy B2 & Hastelloy B suppliers and manufacturers online now, we would advise you to visit Huaxiao Alloy.
As a leading supplier of Hastelloy Alloy products from Shanghai China, Huaxiao Alloy provides customers with high-quality Hastelloy B2 & Hastelloy B, Hastelloy C276 alloy, Hastelloy C4 & C22, Hastelloy G50 Alloy, Hastelloy D205, Hastelloy G30 (UNS N06030), Hastelloy C-2000, and Hastelloy X alloy at a very competitive price.
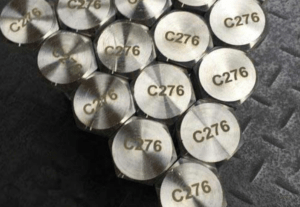
Hastelloy C-276 belongs to nickel-molybdenum-chromium-iron-tungsten nickel-based alloy, which is one of the most corrosion-resistant modern metal materials.
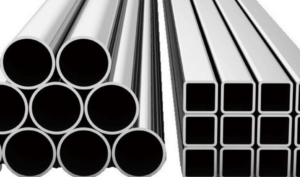
Hastelloy X is a nickel-based superalloy known for its exceptional high-temperature strength and oxidation resistance.
The main differences between Hastelloy B2 and B3 can be outlined as follows:
- Composition:
- Hastelloy B2 has a higher iron content (2-5%) and lower carbon content than B3. This composition contributes to its superior resistance to hydrochloric acid, especially in reducing environments.
- Hastelloy B3 has a lower iron content and higher carbon content, which improves its resistance to high-temperature oxidation and enhances its mechanical properties in high-temperature environments.
- Corrosion Resistance:
- B2 is specifically formulated for optimal performance in reducing acids, such as hydrochloric acid. However, its resistance to oxidizing acids is limited.
- B3 provides better resistance in both reducing and slightly oxidizing environments and is more versatile in applications requiring oxidation resistance at high temperatures.
- Weldability:
- B3 has better weldability compared to B2 due to its more stable composition, reducing the risk of forming detrimental phases during welding.
- High-Temperature Strength:
- B3 generally offers better mechanical strength at higher temperatures compared to B2, making it more suitable for high-temperature applications.
Hastelloy B is a group of nickel-molybdenum alloys known for their excellent resistance to hydrochloric acid and other highly corrosive, reducing environments. The primary alloy in the “Hastelloy B” family is Hastelloy B2, which is characterized by a high molybdenum content (about 30%) and low chromium content, providing outstanding resistance to pitting, crevice corrosion, and stress corrosion cracking in reducing acids. Hastelloy B alloys are widely used in chemical processing industries, particularly where handling of aggressive chemicals such as hydrochloric acid is required.
Alloys that are similar or equivalent to Hastelloy B (typically Hastelloy B2) include:
- Monel 400: This nickel-copper alloy is used in some applications where hydrochloric acid resistance is needed, though it has lower performance in highly reducing environments.
- Incoloy 800: A nickel-iron-chromium alloy with good resistance to oxidation and corrosion in moderately aggressive environments, but not as effective as Hastelloy B in reducing acids.
- Alloy 20: A high-nickel alloy similar to Hastelloy B in its resistance to sulfuric acid and other acids, though it lacks the same resistance to hydrochloric acid as Hastelloy B2.
Hastelloy B3 and Hastelloy C276 are both high-performance alloys, but they differ significantly in their composition and applications:
- Composition:
- Hastelloy B3 is primarily composed of nickel (around 60-70%) and molybdenum (28-30%), with minimal iron content. Its composition is optimized for resistance to hydrochloric acid and other reducing acids.
- Hastelloy C276, on the other hand, has a more complex composition, including nickel (approximately 50-70%), molybdenum (15-17%), chromium (14-16%), and iron (4-7%). The addition of chromium significantly enhances its resistance to oxidizing environments.
- Corrosion Resistance:
- Hastelloy B3 excels in reducing acids like hydrochloric acid but is less resistant to oxidizing acids and high-temperature applications.
- Hastelloy C276 offers excellent resistance to both reducing and oxidizing acids, making it more versatile across a wider range of industrial applications.
- Applications:
- B3 is used primarily in highly corrosive, reducing environments such as hydrochloric acid and sulfuric acid handling.
- C276 is used in a wide variety of applications, including chemical processing, pollution control, and power generation, where both reducing and oxidizing environments are present.
Hastelloy B3 has a few equivalents, but it is a specialized alloy known for its resistance to hydrochloric acid in reducing environments. Some equivalents include:
- Monel 400: Suitable for less aggressive reducing environments but not as resistant to hydrochloric acid as Hastelloy B3.
- Incoloy 800: Offers good high-temperature oxidation resistance but is less effective in reducing acids like hydrochloric acid.
- Alloy 20: Similar to Hastelloy B3 in some applications, particularly for sulfuric acid resistance, but not as strong in hydrochloric acid environments.
Both Hastelloy C22 and Hastelloy C276 are highly resistant to a wide range of corrosive environments, but C22 offers slightly better performance in some areas:
- Hastelloy C22: Contains more chromium and tungsten, making it superior in highly oxidizing environments and capable of withstanding high concentrations of chlorine, wet chlorine gas, and other aggressive environments. It also has better resistance to pitting and crevice corrosion in certain environments.
- Hastelloy C276: More commonly used than C22 and offers excellent resistance to a wide range of acids, including hydrochloric acid, sulfuric acid, and phosphoric acid, along with resistance to oxidizing and reducing environments. However, it is slightly less resistant than C22 in highly oxidizing environments.
In general, C22 may be the better choice for environments with strong oxidizing agents, while C276 is widely used for applications requiring versatility in both reducing and oxidizing conditions.
The advantages of Hastelloy C276 include:
- Excellent corrosion resistance: It is highly resistant to pitting, crevice corrosion, and stress corrosion cracking in both reducing and oxidizing environments, particularly in strong acids like sulfuric, hydrochloric, and phosphoric acids.
- High-temperature performance: C276 maintains its strength and corrosion resistance even at elevated temperatures, making it suitable for use in high-temperature applications.
- Versatility: Due to its resistance to a wide range of chemicals, Hastelloy C276 is used across various industries, including chemical processing, pollution control, power generation, and petrochemical industries.
- Weldability: It has good weldability, and the material retains its properties after welding, making it suitable for complex fabrication.
No, Hastelloy C276 and Inconel C276 are not the same. While they share similar applications due to their corrosion resistance, they belong to different families of alloys:
- Hastelloy C276: A nickel-molybdenum-chromium alloy that provides excellent resistance to a broad range of aggressive chemicals and is particularly effective in both reducing and oxidizing environments.
- Inconel C276: There is no alloy called “Inconel C276.” The Inconel brand includes alloys like Inconel 625 and Inconel 718, which are designed for high-temperature environments and oxidation resistance, but Inconel C276 does not exist. If you meant Hastelloy C276, it is not part of the Inconel series.
The ASTM standard for Hastelloy C276 is ASTM B575. This standard covers the specifications for wrought and cast forms of nickel-molybdenum-chromium alloys, including Hastelloy C276, for use in corrosive environments. The alloy is available in various forms, including plate, sheet, pipe, and bar, and is used in industries where resistance to chemical corrosion is critical.
These answers provide a clear, structured, and scientifically accurate comparison and explanation of the various Hastelloy alloys, their equivalents, advantages, and applications.