Incoloy
Incoloy alloy is a special high temperature alloy known for its excellent high temperature strength and oxidation resistance.
The alloy contains high levels of chromium and aluminum, which form a dense oxide film on the surface of the alloy, effectively resisting oxidation and corrosion at high temperatures.
Inconel alloys are widely used in aerospace, energy and automotive applications because of their ability to maintain their mechanical properties at high temperatures over long periods of time.
The good machinability and weldability of Inkroy alloys also allow for a high degree of flexibility in the manufacturing process. In short, Incoloy alloy is an excellent high-temperature material that provides important support for the development of modern industry.
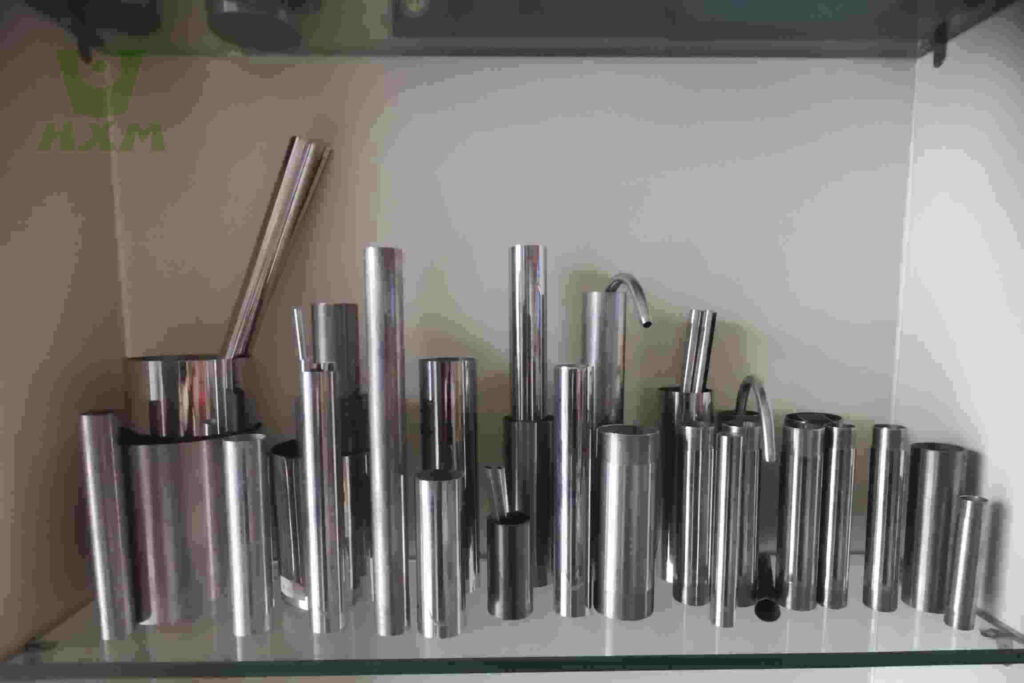
Grades of Incoloy
incoloy Product standards datasheet
Brand | Plate/Strip Material | Seamless Pipe | Welded Pipe | Bar/Wire/Round Rod | Forging/Flange |
---|---|---|---|---|---|
Incoloy 800 | ASTM B409 | ASTM B407/B163 | ASTM B514/B515 | ASTM B408 | ASTM B564 |
Incoloy 800H | ASTM B409 | ASTM B407/B163 | ASTM B514/B515 | ASTM B408 | ASTM B564 |
Incoloy 800HT | ASTM B409 | ASTM B407/B163 | ASTM B514/B515 | ASTM B408 | ASTM B564 |
Incoloy 825 | ASTM B424 | ASTM B423/B163 | ASTM B516/B517/B705 | ASTM B425 | ASTM B564 |
Incoloy 925 | ASTM B625 | ASTM B677 | ASTM B673/B674 | ASTM B649 | ASTM B564 |
Incoloy 926 (AL-6XN) | ASTM B625 | ASTM B677 | ASTM B673/B674 | ASTM B649 | ASTM B564 |
Advantages of Incoloy alloys
The unique benefits of Inkroy alloys are mainly in the following areas:
1. High temperature strength:
Incoloy alloys have excellent high-temperature strength and can maintain stable mechanical properties at extremely high temperatures. The chromium and aluminum elements in its composition effectively increase the alloy’s high temperature strength and heat resistance.
2. Antioxidant performance:
Incoloy alloy has excellent antioxidant performance, can effectively resist oxidation in high temperature environment. The dense oxide film formed on the surface protects the interior of the alloy from corrosion and oxidation.
3. Corrosion resistance:
Incoloy alloy has excellent corrosion resistance, can resist corrosion in a variety of harsh environments. The chromium element in its composition provides excellent corrosion resistance, while the aluminum element also provides excellent corrosion resistance.
4. Processing performance:
Because of the good processing performance of Kolloy alloy, it can be easily cut, bent, drilled and other processing operations. The surface quality after machining is relatively high.
5. Welding performance:
Incoloy alloy has good welding performance, can be connected through a variety of welding processes. This allows for more flexible application of Inkroy alloys in the manufacturing process, improving productivity.
In summary, the unique benefits of Inkroy alloys make them a superior high-temperature material, distinguishing them from other specialty alloys. Its excellent performance in high-temperature strength, oxidation resistance, corrosion resistance, machinability and weldability has led to a wide range of applications for Incoloy alloys in aerospace, energy and automotive fields, providing an important support for the development of modern industry.
Applications of Incoloy alloys
Incoloy alloys are a group of nickel-based superalloys known for their excellent corrosion resistance, high-temperature strength, and durability. These alloys are widely used in various industries due to their unique combination of properties. Below are some common applications of Incoloy alloys along with the most commonly used grades for each application:
Chemical Processing
- Incoloy 800 (UNS N08800): Used in sulfuric acid pickling tanks, heat exchangers, and process piping due to its corrosion resistance in acidic environments.
Aerospace
- Incoloy 909 (UNS N19909): Employed in aircraft engine components, including turbine blades and high-temperature fasteners, due to its high-temperature strength and oxidation resistance.
Oil and Gas Industry
- Incoloy 825 (UNS N08825): Used in downhole equipment, oil well components, and piping systems due to its excellent resistance to corrosion and oxidation in sour gas environments.
Nuclear Power Plants
- Incoloy 800H (UNS N08810): Utilized in nuclear reactor components, such as steam generator tubing and reactor core components, due to its high-temperature strength and resistance to radiation-induced embrittlement.
Heat Treatment Furnaces
- Incoloy 800HT (UNS N08811): Employed in heat treatment furnaces, radiant tubes, and furnace fixtures due to its high-temperature strength and resistance to oxidation and carburization.
Marine Applications
- Incoloy 825 (UNS N08825): Used in marine environments for seawater piping systems, heat exchangers, and boat shafts due to its superior corrosion resistance to seawater and marine atmospheres.
Petrochemical Industry
- Incoloy 800 (UNS N08800): Used in petrochemical plants for reactor vessels, heat exchangers, and piping systems due to its corrosion resistance in high-temperature sulfur-containing environments.
These are just a few examples of the diverse applications of Incoloy alloys, and there are other grades available tailored for specific requirements in different industries. It’s essential to select the appropriate Incoloy alloy grade based on the specific application and environmental conditions to ensure optimal performance and longevity.
FAQs about Incoloy alloy
- INCONEL and INCOLOY are both nickel-based alloys known for their excellent corrosion resistance and high-temperature strength.
- INCONEL alloys are primarily composed of nickel-chromium and are designed for high-temperature applications. They exhibit excellent resistance to oxidation and corrosion.
- INCOLOY alloys are also nickel-chromium-based but contain additional elements like molybdenum, copper, and iron, enhancing their corrosion resistance and mechanical properties.
- In summary, while both INCONEL and INCOLOY are nickel-based alloys with similar base compositions, INCOLOY alloys often contain additional elements for improved corrosion resistance and mechanical properties.
- INCOLOY is a family of nickel-based superalloys known for their excellent corrosion resistance, high-temperature strength, and durability.
- Titanium is a chemical element (Ti) known for its low density, high strength, and excellent corrosion resistance.
- INCOLOY alloys are primarily composed of nickel, whereas titanium is a standalone metallic element.
- INCOLOY alloys are used in various industries due to their unique combination of properties, whereas titanium is utilized in aerospace, medical implants, and chemical processing industries due to its lightweight and corrosion-resistant properties.
- In summary, INCOLOY is a type of nickel-based alloy, while titanium is a standalone metallic element with distinct properties and applications.
- Alloy 800 and INCOLOY 800 refer to the same nickel-iron-chromium alloy with the designation UNS N08800.
- The term INCOLOY 800 is a trademark of Special Metals Corporation, which manufactures and markets this alloy.
- Alloy 800/INCOLOY 800 is a widely used material for high-temperature applications due to its excellent resistance to oxidation, carburization, and nitridation.
- In summary, there is no difference between alloy 800 and INCOLOY 800; they refer to the same nickel-iron-chromium alloy with the designation UNS N08800, with INCOLOY 800 being a trademarked name for the alloy.