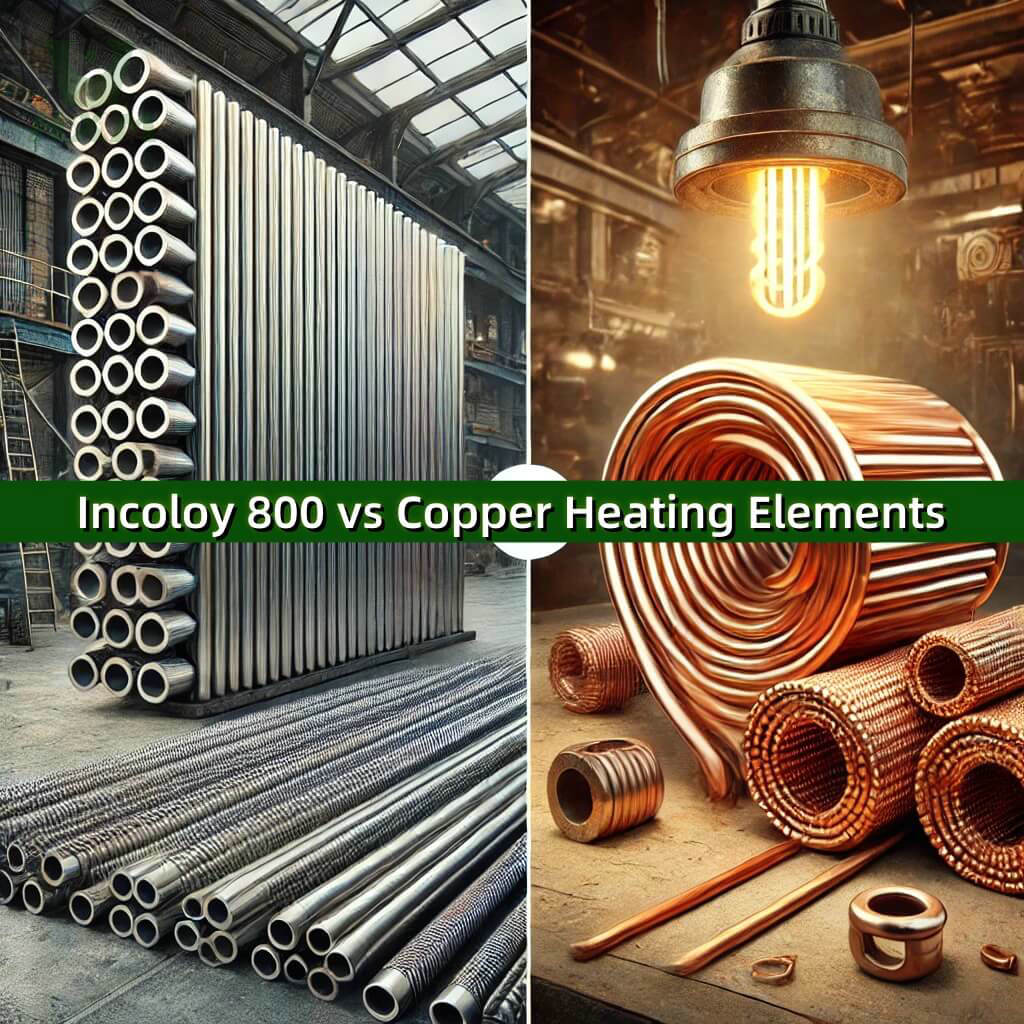
In the realm of industrial heating elements, two materials that often find their way into critical applications are Incoloy 800 vs copper heating elements. Both materials possess unique properties that make them suitable for specific heating requirements. Understanding the differences between these two materials is crucial for ensuring the right choice is made for a given application. In this blog post, let’s take a closer look at the differences between the Incoloy 800 and copper heating elements.
Incoloy 800 vs Copper Heating Elements – What’s the Difference?
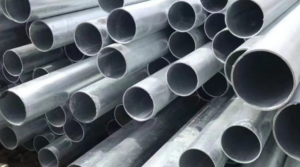
Incoloy 925 (N08925) alloy is a nickel base alloy containing molybdenum and copper with excellent hot and cold work properties.
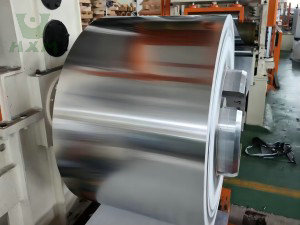
Incoloy 800/800H/800HT the chemical composition of these three are very similar, so all have a very good resistance to reduction, oxidation, nitriding medium corrosion and resistance to redox alternating medium corrosion performance, and in the long term application of high temperature has a high metallurgical stability.
Incoloy 800 vs Copper Heating Elements – 1. Incoloy 800: An Overview
Incoloy 800 is a nickel-iron-chromium alloy that offers exceptional resistance to corrosion and oxidation at elevated temperatures. This material was developed specifically to handle high-temperature applications without sacrificing its mechanical properties. Its composition, which includes nickel, chromium, and iron, among other elements, gives it high ductility and toughness even under severe thermal conditions.
One of the key features of Incoloy 800 is its ability to maintain its mechanical properties at temperatures up to 1300°F (704°C). This allows it to be used in high-temperature heating elements without experiencing significant degradation in performance. Additionally, its resistance to corrosion in oxidizing atmospheres makes it suitable for use in environments where other materials would quickly fail.
Incoloy 800 vs Copper Heating Elements – 2. Copper Heating Elements: An Overview
Copper, on the other hand, is a widely used material for heating elements due to its excellent conductivity. Copper’s high electrical conductivity allows it to transfer heat efficiently, making it a popular choice for applications that require rapid heating. Additionally, copper is relatively inexpensive and easy to work with, further adding to its popularity.
However, copper’s use in high-temperature applications is limited by its relatively low melting point of 1981°F (1083°C). Above this temperature, copper begins to lose its structural integrity, making it unsuitable for sustained use in extreme thermal conditions. Additionally, copper’s susceptibility to oxidation at higher temperatures can lead to corrosion and premature failure.
Comparing Incoloy 800 vs Copper Heating Elements
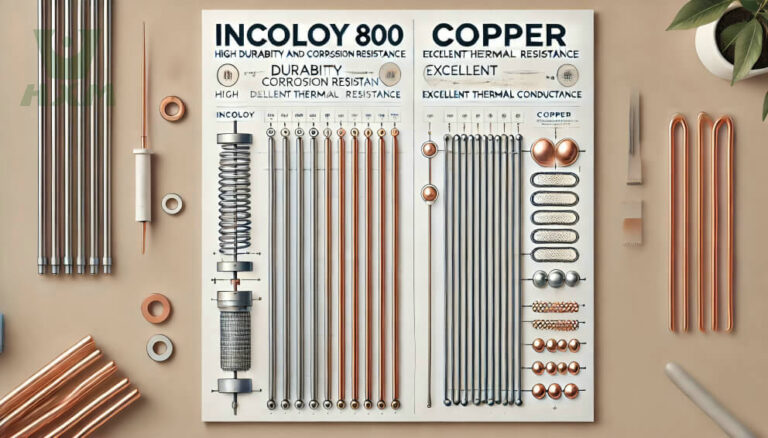
When comparing Incoloy 800 and copper heating elements, several key differences become apparent:
- Temperature Resistance: Incoloy 800 can maintain its mechanical properties at temperatures well above those at which copper would melt. This makes Incoloy 800 the preferred choice for high-temperature applications.
- Corrosion Resistance: Incoloy 800’s resistance to corrosion in oxidizing atmospheres is superior to copper’s. This allows it to withstand exposure to corrosive environments without premature failure.
- Cost: Copper is generally more cost-effective than Incoloy 800 due to its abundance and ease of processing. However, the longer lifespan and superior performance of Incoloy 800 often justify its higher initial cost.
- Heat Transfer Efficiency: Copper’s high conductivity makes it more efficient at transferring heat than Incoloy 800. This can be advantageous in applications that require rapid heating.
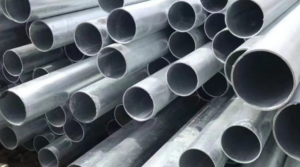
Incoloy 925 (N08925) alloy is a nickel base alloy containing molybdenum and copper with excellent hot and cold work properties.
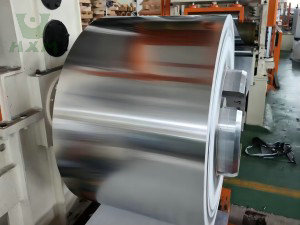
Incoloy 800/800H/800HT the chemical composition of these three are very similar, so all have a very good resistance to reduction, oxidation, nitriding medium corrosion and resistance to redox alternating medium corrosion performance, and in the long term application of high temperature has a high metallurgical stability.
In summary, the choice between Incoloy 800 vs copper heating elements depends on the specific requirements of the application. For high-temperature applications or those that involve exposure to corrosive environments, Incoloy 800 offers superior performance. On the other hand, copper’s cost-effectiveness and excellent heat transfer properties make it a suitable choice for lower-temperature applications that require rapid heating.
Thank you for reading our article and we hope it can help you to have a better understanding of the differences between Incoloy 800 vs copper heating elements. If you are looking for Incoloy 800 suppliers online now, please don’t hesitate to contact Huaxiao Alloy.
As a leading supplier of Incoloy Alloys from Shanghai China, Huaxiao Alloy provides customers with high-quality Incoloy Alloy 925, Incoloy Alloy 800, Incoloy Alloy 825, Inconel 602 alloy, Hastelloy S Alloy, Inconel Alloy 600, Inconel Alloy 601, Inconel 625 UNS N06625, Hastelloy B3 (UNS N10675), Hastelloy D205, and Hastelloy G30 (UNS N06030) at a very competitive price.
Aspect | INCOLOY Heating Element | Copper Heating Element |
---|---|---|
Material | Nickel-based alloy (e.g., INCOLOY 800, 825). | Pure copper or copper alloys. |
Corrosion Resistance | Excellent, especially in high-temperature and corrosive environments. | Moderate, susceptible to corrosion in acidic or harsh environments. |
Thermal Conductivity | Lower than copper. | Very high, providing efficient heat transfer. |
Durability | High; withstands extreme heat and corrosive chemicals. | Moderate; prone to oxidation and pitting over time. |
Cost | Higher due to its superior performance. | Lower, making it cost-effective for general uses. |
Applications | Industrial heaters, boilers, and chemical environments. | Domestic water heaters and low-corrosion settings. |
Key Difference: INCOLOY is better for high-temperature and corrosive environments, while copper is suitable for cost-effective and non-corrosive settings.
Standard | Equivalent Material |
---|---|
UNS | N08800 |
DIN | 1.4876 |
ISO | Alloy 800 |
Trade Names | Nickel Alloy 800, Alloy 800, VDM Alloy 800 |
Key Characteristics:
- High resistance to oxidation and carburization.
- Excellent strength at elevated temperatures.
Applications: Often compared with Hastelloy, Inconel, or other nickel-based alloys depending on performance requirements.
Copper heating elements can be considered “better” depending on the context:
Advantages of Copper:
- High Thermal Conductivity: Transfers heat quickly and efficiently.
- Cost-Effective: More affordable than advanced alloys like INCOLOY.
- Domestic Applications: Suitable for water heaters, kettles, and low-corrosion environments.
Limitations:
- Corrosion Susceptibility: Fails quickly in acidic or hard water conditions.
- Lower Durability: Less effective at handling high temperatures and chemical exposure.
Conclusion: Copper is better for cost-sensitive, non-corrosive applications, but INCOLOY is superior for industrial and corrosive conditions.
The “best” metal depends on the application:
Material | Best For |
---|---|
Nichrome (Nickel-Chromium) | General heating applications (e.g., toasters, ovens) due to high resistivity and oxidation resistance. |
INCOLOY | High-temperature industrial applications, corrosive environments. |
Copper | Domestic water heaters and efficient heat transfer in non-corrosive conditions. |
Kanthal (Iron-Chromium-Aluminum) | High-temperature furnaces due to superior oxidation resistance. |
Conclusion: INCOLOY is ideal for industrial and chemical environments, while Nichrome and Kanthal are better for general heating applications.
An INCOLOY 800 heating element is a nickel-iron-chromium alloy heating element designed for high-temperature and corrosive applications.
Key Features:
- Temperature Resistance: Performs up to 1100°C without significant degradation.
- Corrosion Resistance: Excels in oxidizing, carburizing, and high-temperature chemical environments.
- Durability: Long-lasting even in harsh conditions.
Applications:
- Boilers, industrial heaters, and heat exchangers.
- Chemical and petrochemical industries.
- Power generation plants.
Advantage: Combines durability and resistance to chemical corrosion, outperforming most other materials in demanding applications.
Aspect | INCOLOY 800 | INCOLOY 825 |
---|---|---|
Composition | Nickel-iron-chromium alloy. | Nickel-iron-chromium alloy with molybdenum, copper, and titanium. |
Corrosion Resistance | High resistance to oxidation and carburization. | Superior resistance to acids (e.g., sulfuric, phosphoric). |
Temperature Resistance | Excellent at elevated temperatures. | Performs better in environments below 540°C. |
Applications | Heat exchangers, chemical processing, and industrial heaters. | Acid-handling equipment, pollution control systems, and marine environments. |
Key Difference: INCOLOY 800 is optimized for high temperatures, while INCOLOY 825 is better suited for environments involving strong acids and marine conditions.