Among numerous alloys, Incoloy 800 vs Inconel 600 stand out as two highly regarded materials with similar applications but distinct characteristics. In this article, we will delve into the intricacies of Incoloy 800 vs Inconel 600 alloys, highlighting their differences in composition, physical properties, and industrial uses.
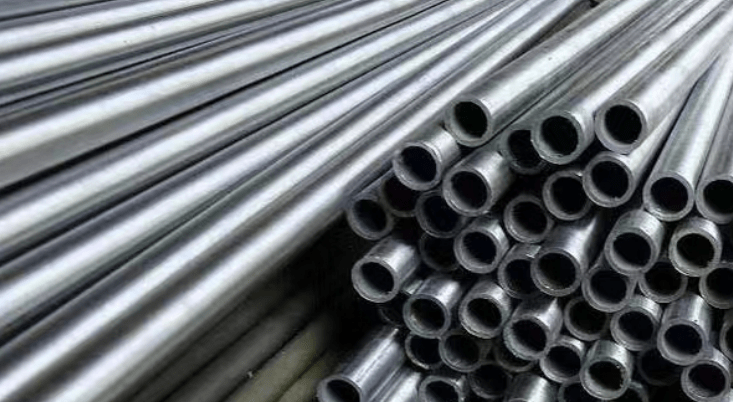
Incoloy 800 vs Inconel 600: What’s the Difference?
Incoloy 800 vs Inconel 600 – 1. Incoloy 800: A Brief Overview
Incoloy 800 is an austenitic nickel-iron-chromium alloy that offers excellent resistance to oxidation and corrosion, particularly in high-temperature environments. Its composition, which includes significant amounts of nickel, chromium, and iron, along with smaller amounts of carbon, silicon, manganese, sulfur, phosphorus, copper, and aluminum, gives it its unique properties. The alloy’s high nickel content contributes to its resistance to chloride-ion stress-corrosion cracking, while the chromium content enhances its corrosion resistance.
Incoloy 800 finds widespread use in a variety of industrial applications, particularly in the chemical processing industry, where it is used in heaters, heat exchangers, and other equipment that require resistance to corrosion and oxidation. Its excellent mechanical properties, including high ductility and toughness, make it suitable for use in complex and demanding industrial processes.
Incoloy 800 vs Inconel 600 – 2. Inconel 600: An Introduction
In contrast to Incoloy 800, Inconel 600 is a nickel-chromium alloy that offers similar corrosion resistance but with additional strength and toughness. Its composition, which is primarily nickel with significant amounts of chromium and iron, along with smaller amounts of carbon, silicon, manganese, sulfur, phosphorus, and aluminum, gives it its unique characteristics. The alloy’s high nickel content contributes to its resistance to oxidation and corrosion, while the chromium content enhances its resistance to corrosive environments.
Inconel 600 is widely used in high-temperature applications, particularly in the aerospace and nuclear industries. Its exceptional strength and creep resistance, along with its resistance to corrosion and oxidation, make it ideal for use in gas turbines, nuclear reactors, and other components that require durability and stability at elevated temperatures.
Incoloy 800 vs Inconel 600 – 3. Key Differences
- Composition: While both alloys are primarily composed of nickel, chromium, and iron, their exact compositions differ. Incoloy 800 has a higher iron content, while Inconel 600 has a higher nickel content. This difference in composition affects their physical properties and applications.
- Physical Properties: Incoloy 800 offers excellent resistance to oxidation and corrosion, particularly in high-temperature environments. It is also known for its good ductility and toughness. In contrast, Inconel 600 exhibits superior strength and creep resistance at elevated temperatures, making it ideal for high-stress applications.
- Applications: Due to its excellent corrosion resistance and ductility, Incoloy 800 is primarily used in the chemical processing industry, where it is exposed to corrosive environments. On the other hand, Inconel 600’s strength and creep resistance make it a preferred material for aerospace and nuclear applications, where components must withstand extreme temperatures and stresses.
- Cost: Generally speaking, Inconel 600 may be slightly more costly than Incoloy 800 due to its higher nickel content and the associated manufacturing processes. However, this cost difference is often offset by the alloy’s superior performance in high-temperature applications.
Conclusion
In summary, while both Incoloy 800 and Inconel 600 are nickel-based alloys with excellent corrosion resistance, they differ significantly in their composition, physical properties, and applications. Incoloy 800, with its higher iron content and excellent ductility, is ideal for use in chemical processing and other corrosive environments. In contrast, Inconel 600, with its higher nickel content and superior strength at elevated temperatures, is well-suited for aerospace and nuclear applications.
Thank you for reading our article and we hope it can help you to have a better understanding of the differences between Incoloy 800 vs Inconel 600. If you are looking for Incoloy 800 & Inconel 600 suppliers online now, please don’t hesitate to contact Huaxiao Alloy.
As a leading supplier of high-temperature alloys from Shanghai China, Huaxiao Alloy provides customers with high-quality Incoloy 800 & Inconel 600 alloys, Inconel 825, Inconel 602CA Alloy, Inconel 713LC alloy, Inconel Alloy 750, Inconel Alloy 718, Inconel 602 alloy, Inconel Alloy 601, Inconel 625 UNS N06625, and Incoloy Alloy 925 (UNS N08925) at a very competitive price.