Incoloy 825
Incoloy 825 is a titanium stabilised, fully austenitic nickel-iron-chromium alloy with additions of copper and molybdenum.Incoloy 825 is a versatile engineering alloy with resistance to corrosion by acids and alkali metals in both oxidising and reducing environments. The high nickel content gives the alloy effective resistance to stress corrosion cracking.
Applicable Standards for Incoloy 825
Alloy 825(UNS N08825)
Product Form | Standard | Description |
---|---|---|
Plate, Sheet, and Strip | ASTM B424 | This standard specifies requirements for nickel-iron-chromium-molybdenum-copper alloy (UNS N08825, N08221, and N06845) plate, sheet, and strip. |
Seamless Pipe and Tube | ASTM B423 | This standard covers nickel-iron-chromium-molybdenum-copper alloys (UNS N08825 and N08221)* seamless pipe and tube. |
Welded Pipe | ASTM B705 | This standard specifies welded pipe from the nickel-iron-chromium alloy (UNS N08825). |
Welded Tube | ASTM B704 | This standard is for welded tube made from nickel-iron-chromium alloy (UNS N08825). |
Bar, Rod, and Wire | ASTM B425 | Specifies the requirements for nickel-iron-chromium-molybdenum-copper alloy (UNS N08825, N08221) rods and bars. |
Forgings | ASTM B564 | This standard covers nickel alloy forgings, including Incoloy 825. |
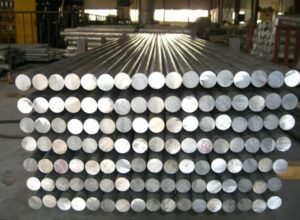
Content
Applications of Incoloy 825
Alloy 825(UNS N08825)
Incoloy 825 is a versatile nickel-iron-chromium alloy with good resistance to oxidation, corrosion, and a broad range of chemicals, thanks to its composition which includes molybdenum, copper, and titanium. The unique properties of Incoloy 825, such as its resistance to sulfuric and phosphoric acids and its ability to avoid pitting in chloride environments, make it suitable for specific applications across various industries. Here are some key applications that leverage the unique properties of Incoloy 825:
Oil and Gas Industry: Incoloy 825 is widely used in the oil and gas industry for piping, valves, pumps, and other components exposed to corrosive substances, especially those containing sulfuric and phosphoric acids.
Chemical Processing: The alloy’s resistance to a wide range of chemicals makes it ideal for reactor vessels, heat exchangers, and piping systems in chemical processing plants, especially where acidic environments are common.
Pollution Control Equipment: Incoloy 825 is used in flue-gas desulfurization systems and other pollution control equipment due to its resistance to oxidizing and reducing agents.
Marine Applications: Its resistance to pitting and crevice corrosion in seawater and marine environments makes it suitable for parts in shipbuilding and repair, such as propeller shafts, oil rig components, and seawater-cooled heat exchangers.
Nuclear Applications: Incoloy 825 is used in nuclear fuel reprocessing and waste handling systems due to its resistance to nuclear acids.
Acid Production: Its resistance to sulfuric and phosphoric acids is valuable in equipment used in acid production, such as piping, tanks, and heat exchangers.
Power Generation: Incoloy 825 is used in superheaters, re-heaters, and other components in power plants due to its ability to withstand high temperatures and corrosive environments.
The alloy’s combination of high nickel content with molybdenum and copper provides excellent resistance to a variety of corrosive environments, while the addition of chromium contributes to its oxidation resistance. These properties make Incoloy 825 a preferred material for demanding applications where both corrosion resistance and high strength are required.
Chemical composition of Incoloy 825(%)
Alloy 825(UNS N08825)
Element | Percentage (%) |
---|---|
Nickel (Ni) | 38.0 – 46.0 |
Chromium (Cr) | 19.5 – 23.5 |
Iron (Fe) | 22.0 min |
Molybdenum (Mo) | 2.5 – 3.5 |
Copper (Cu) | 1.5 – 3.0 |
Titanium (Ti) | 0.6 – 1.2 |
Carbon (C) | Max 0.05 |
Manganese (Mn) | Max 1.0 |
Silicon (Si) | Max 0.5 |
Sulphur (S) | Max 0.03 |
Aluminum (Al) | Max 0.2 |
Physical properties of Incoloy 825
Alloy 825(UNS N08825)
Physical Property | Value | Unit |
---|---|---|
Density | 8.14 | g/cm³ |
Melting Point | 1370 – 1400 | °C |
Specific Heat Capacity | 440 | J/kg·K |
Thermal Conductivity | 11.1 | W/m·K |
Coefficient of Expansion | 14.0 (20-100°C) / 15.7 (20-300°C) | µm/m·K |
Electrical Resistivity | 1.13 | µΩ·m |
Modulus of Elasticity | 196 | GPa |
Poisson’s Ratio | 0.3 | Unitless |
Mechanical properties of Incoloy 825
Alloy 825(UNS N08825)
Mechanical Property | Value | Unit |
---|---|---|
Tensile Strength | 550 – 690 | MPa |
Yield Strength (0.2% Offset) | 220 – 310 | MPa |
Elongation | 30 – 45 | % |
Hardness | 85 – 95 | Rockwell B |
FAQs about Incoloy 825
Alloy 825(UNS N08825)
The density of Incoloy 825 is approximately 8.14 grams per cubic centimeter (g/cm³). This measure indicates the alloy’s mass per unit volume, providing essential information for various engineering and design calculations, especially when weight and material volume considerations are critical in application design and materials selection.
Incoloy 825’s relatively high density is attributed to its rich composition of nickel, iron, and chromium, along with the presence of molybdenum, copper, and titanium. This density plays a crucial role in the alloy’s overall mechanical and physical properties, influencing its strength, durability, and suitability for specific industrial applications, especially in environments where resistance to corrosion and high temperatures is required. Understanding the density of Incoloy 825 is vital for assessing the alloy’s behavior and performance under different conditions and in various applications, including chemical processing, oil and gas exploration, and marine environments.
The hardness of Incoloy 825 typically falls within the range of 85 to 95 on the Rockwell B scale. This metric provides a measure of the material’s resistance to indentation and gives an indication of its strength and wear resistance.
In the context of Incoloy 825, a nickel-iron-chromium alloy known for its excellent corrosion resistance and durability, the Rockwell B hardness value signifies that while the alloy is relatively hard and can sustain moderate wear and tear, it remains less hard than materials rated at higher values on the Rockwell C scale, which is used for harder materials.
The hardness of Incoloy 825 contributes to its suitability for various industrial applications where the material must resist surface wear while offering excellent mechanical strength and corrosion resistance. This balance of properties is crucial for components exposed to harsh environments, such as those found in chemical processing, oil and gas extraction, and marine engineering.
Incoloy 800 and Incoloy 825 are both nickel-iron-chromium alloys designed to offer superior corrosion resistance, but they have different compositions that confer distinct properties, making them suitable for various applications. Here’s a comparison of the two:
Chemical Composition:
- Incoloy 800: Primarily composed of nickel, chromium, and iron. It typically contains 30-35% nickel, 19-23% chromium, and a significant amount of iron. It may include small amounts of aluminum and titanium to enhance its high-temperature properties.
- Incoloy 825: In addition to nickel, chromium, and iron, it contains significant amounts of molybdenum, copper, and titanium. Typically, it has about 38-46% nickel, 19.5-23.5% chromium, 2.5-3.5% molybdenum, and 1.5-3% copper.
Corrosion Resistance:
- Incoloy 800: Offers good resistance to oxidation and carburization at high temperatures and is moderately resistant to sulfuric and nitric acids.
- Incoloy 825: Provides enhanced resistance to a broader range of corrosive environments compared to Incoloy 800, including resistance to both reducing and oxidizing acids, pitting, stress-corrosion cracking, and intergranular corrosion. This is due to the addition of molybdenum, copper, and increased nickel content.
Applications:
- Incoloy 800: Often used in high-temperature industrial applications, such as heat-treating equipment, chemical and petrochemical processing, and super-heater and re-heaters in power plants.
- Incoloy 825: Its enhanced corrosion resistance makes it suitable for more aggressive environments, like those in the oil and gas extraction, chemical processing, and marine industries. It is particularly useful in handling sulfuric and phosphoric acids.
Mechanical Properties:
- Both alloys have excellent mechanical properties at high temperatures, but Incoloy 825’s additional elements provide it with a higher strength and better resistance to localized corrosion than Incoloy 800.
In summary, while both Incoloy 800 and 825 are used for their strength and corrosion resistance at high temperatures, Incoloy 825’s composition offers broader chemical resistance, making it more suitable for corrosive environments where Incoloy 800 might not perform as well.
Chemical Composition:
- Incoloy 825: It’s a nickel-iron-chromium alloy with additions of molybdenum, copper, and titanium. Typically, Incoloy 825 contains around 38-46% nickel, 19.5-23.5% chromium, 2.5-3.5% molybdenum, 1.5-3% copper, and 0.6-1.2% titanium.
- Inconel 625: This is a nickel-chromium-molybdenum alloy with a significant addition of niobium. Inconel 625 typically consists of 58% nickel, 20-23% chromium, 8-10% molybdenum, and 3.15-4.15% niobium.
Corrosion Resistance:
- Incoloy 825: Offers excellent resistance to both oxidizing and reducing acids, such as sulfuric and phosphoric acids, and is very resistant to pitting, crevice corrosion, and stress-corrosion cracking. The copper content enhances its resistance to sulfuric acid.
- Inconel 625: Provides outstanding resistance to a wide range of highly corrosive environments, including seawater, pitting, crevice corrosion, and chloride-ion stress-corrosion cracking. It’s particularly noted for its resistance to high-temperature oxidation.
Applications:
- Incoloy 825: Commonly used in oil and gas extraction, chemical processing, pollution control equipment, and sulfuric acid piping and vessels.
- Inconel 625: Widely used in aerospace applications, chemical processing, marine engineering, and nuclear reactors due to its high strength and excellent corrosion resistance, particularly at extreme temperatures.
Mechanical Properties:
- Both alloys exhibit excellent mechanical properties at elevated temperatures, but Inconel 625 is generally stronger and more ductile, with better fatigue and thermal-fatigue strength, largely due to the strengthening effects of niobium.
Temperature Resistance:
- While both alloys perform well at elevated temperatures, Inconel 625 typically offers superior strength and stability at higher temperatures compared to Incoloy 825.
In summary, while both Incoloy 825 and Inconel 625 offer excellent corrosion resistance, the choice between them depends on the specific environmental conditions and mechanical requirements of the application. Inconel 625 is often preferred for applications requiring higher strength and resistance to extreme temperatures, while Incoloy 825 is favored in environments where its specific chemical resistance, especially to acids and oxidizing agents, is needed.
It appears there’s a bit of confusion in the comparison you’re asking for—Incoloy 825 versus Inconel 825. In fact, Inconel 825 doesn’t exist as a separate or distinct material. The confusion likely arises from mixing the names of two different alloy families: Incoloy and Inconel.
Incoloy 825: This is a well-known alloy, part of the Incoloy family, which is primarily designed for excellent corrosion resistance in both oxidizing and reducing environments. It contains nickel, iron, and chromium, along with molybdenum, copper, and titanium, which contribute to its resistance to a wide range of corrosive conditions.
Inconel Alloys: These are part of a different family of nickel-chromium-based superalloys known for their ability to withstand high temperatures, corrosion, and pressure. Common alloys in this family include Inconel 600, 625, 718, etc., but there is no Inconel 825.
If you’re comparing Incoloy 825 with an Inconel alloy, the comparison should be with a specific Inconel alloy (like Inconel 625, as previously discussed). Each Inconel alloy has unique properties tailored to specific environments, often characterized by extreme temperatures or corrosive conditions, where they exhibit superior strength and corrosion resistance.
Understanding these distinctions is crucial when selecting materials for specific applications, ensuring that the chosen alloy will perform optimally in the intended service environment. If you have a specific Inconel alloy in mind for comparison with Incoloy 825, please let me know, and I can provide a detailed comparison for those materials.
Welding Incoloy 825, a nickel-iron-chromium alloy with additions of molybdenum, copper, and titanium, requires careful attention to ensure the integrity and corrosion resistance of the weld. Here’s a general guide to the welding procedure for Incoloy 825:
1. Material Preparation:
- Ensure that the surfaces to be welded are clean, free of any contaminants, oils, or greases. Use a stainless steel brush or appropriate solvent for cleaning.
- Preheat is not typically required for Incoloy 825, but the base material and the filler should be at room temperature.
2. Filler Material:
- Use a matching filler material, commonly ERNiCrMo-3 (for Inconel 625) or ERNiFeCr-1, which is specifically designed for welding Incoloy 825 and similar alloys. The choice of filler ensures compatibility and maintains corrosion resistance.
3. Welding Process:
- TIG (Tungsten Inert Gas) welding is often preferred for Incoloy 825 due to its ability to produce high-quality, clean welds. MIG (Metal Inert Gas) and SMAW (Shielded Metal Arc Welding) can also be used depending on the application and thickness of the material.
- Use argon or a mixture of argon and helium as shielding gas to protect the weld pool from atmospheric contamination.
4. Welding Parameters:
- Adjust the welding parameters (current, voltage, and travel speed) based on the thickness of the material and the type of welding process used.
- Avoid excessive heat input, as this can lead to hot cracking and may affect the alloy’s corrosion resistance.
5. Post-Weld Treatment:
- Post-weld heat treatment is not typically required for Incoloy 825 unless there’s a specific concern for stress relief.
- Inspect the weld for any defects such as cracks, porosity, or undercut. Non-destructive testing methods can be employed to ensure weld integrity.
6. Safety Precautions:
- Follow all relevant safety guidelines for welding, including the use of proper personal protective equipment (PPE), adequate ventilation, and eye protection.
It’s important to note that this is a general guide, and specific applications may require additional considerations or adjustments to the welding procedure. Consulting with a welding engineer or a metallurgist and following the recommendations from the material and filler manufacturers are crucial steps in ensuring the success of welding Incoloy 825.