Inconel alloys have long been a staple in the materials science world, with their unique combinations of corrosion resistance, strength, and high-temperature stability making them invaluable for a wide range of industrial applications. Among these alloys, Inconel 182 vs Inconel 625 stand out as two of the most popular choices. In this article, we will delve into the key differences between Inconel 182 and Inconel 625, highlighting their composition, properties, and specific uses.
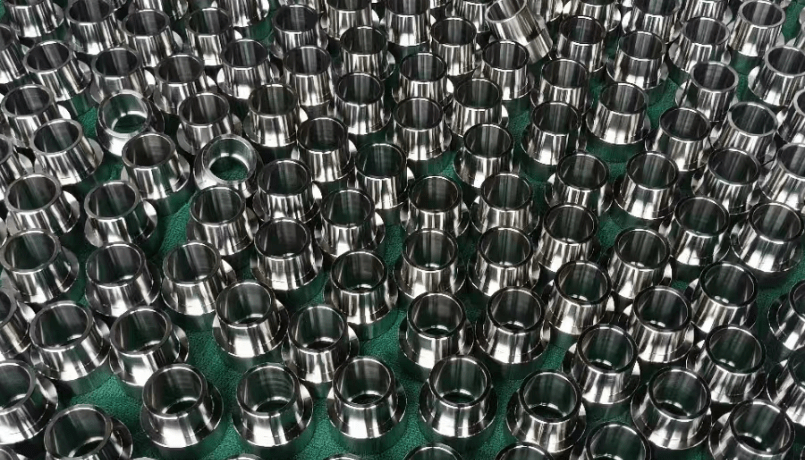
Inconel 182 vs Inconel 625 – What’s the Difference?
Inconel 182 vs Inconel 625 – 1. Compositional Distinctions
The primary difference between Inconel 182 and Inconel 625 lies in their chemical composition. Inconel 182 is a nickel-chromium-iron alloy that contains significant amounts of chromium and iron, along with molybdenum and titanium for added corrosion resistance and strength. This composition gives Inconel 182 excellent resistance to oxidizing and reducing environments, making it suitable for welding applications in high-temperature, corrosive settings.
On the other hand, Inconel 625 is a nickel-chromium alloy with added molybdenum and niobium. The higher nickel content in Inconel 625, along with the presence of niobium, contributes to its superior corrosion resistance, especially in chloride-containing environments. Additionally, the alloy’s composition enables it to maintain its mechanical properties even at elevated temperatures, making it ideal for use in extreme heat conditions.
Inconel 182 vs Inconel 625 – 2. Properties Comparison
Both Inconel 182 and Inconel 625 exhibit excellent strength and ductility, allowing them to withstand significant loads and deformation. However, Inconel 625 offers slightly superior tensile strength and yield strength compared to Inconel 182. This makes Inconel 625 a preferred choice for applications that require maximum mechanical performance.
Moreover, Inconel 625 demonstrates greater resistance to crevice and pitting corrosion, especially in marine and other chloride-rich environments. This property is particularly important in applications such as offshore oil and gas exploration, where equipment is constantly exposed to corrosive seawater.
Inconel 182 vs Inconel 625 – 3. Applications and Uses
The choice between Inconel 182 and Inconel 625 often depends on the specific requirements of the application. Inconel 182 is commonly used in welding applications that involve the joining of dissimilar metals, particularly in the nuclear and chemical processing industries. Its resistance to oxidation and reducing agents makes it suitable for these demanding environments.
In contrast, Inconel 625 is widely used in high-temperature applications such as furnace parts, gas turbines, and heat treatment equipment. Its excellent corrosion resistance, combined with its ability to retain mechanical properties at high temperatures, makes it an ideal material for these applications.
Conclusion
In summary, Inconel 182 and Inconel 625 are both outstanding alloys with unique properties and applications. Inconel 182 excels in welding applications that require resistance to oxidizing and reducing agents, while Inconel 625 stands out in high-temperature, corrosive environments due to its superior corrosion resistance and mechanical properties.
Thank you for reading our article and we hope it can help you to have a better understanding of the differences between Inconel 182 vs Inconel 625. If you are looking for Inconel 182 & Inconel 625 suppliers online, we would advise you to visit Huaxiao Alloy.
As a leading supplier of Inconel Alloys from Shanghai China, Huaxiao Alloy offers customers high-quality Inconel 182 Alloy, Inconel 625 Alloy, Inconel 82 Filler Wire, Inconel X750, Inconel 602 Alloy, and Inconel Alloy 601 at a very competitive price.