Inconel 625 Bars - Composition, Properties and Uses
- March 18, 2024
- 12:57 am
- 1204
Inconel 625 bars, a nickel-chromium-molybdenum-based superalloy, have emerged as a leading material choice in numerous industrial sectors, renowned for their superior mechanical properties, resistance to corrosion and oxidation, and exceptional fabrication characteristics. In this article, we will take a closer look at the composition, properties, and uses of Inconel 625 bars.
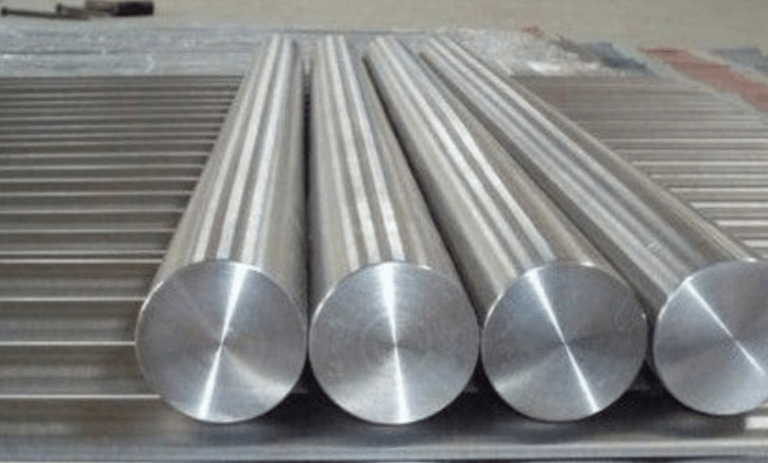
The composition of Inconel 625 bars is tailored to provide optimal performance in extreme conditions. The primary elements in its composition are nickel, chromium, and molybdenum, which together contribute to the alloy’s corrosion resistance and high-temperature stability. Nickel, being the base element, offers resistance to corrosion and oxidation. Chromium enhances the corrosion resistance, particularly against oxidizing acids, while molybdenum adds further resistance to reducing environments and enhances the alloy’s strength.
Additionally, Inconel 625 contains small amounts of aluminum and titanium, which form gamma prime precipitates during heat treatment. These precipitates strengthen the alloy, improving its mechanical properties at elevated temperatures. The controlled addition of iron and carbon also contributes to the alloy’s overall performance.
The properties of Inconel 625 bars are truly exceptional. One of the most notable properties is its high tensile strength, even at elevated temperatures. This allows it to maintain structural integrity in demanding applications where conventional materials would fail. Furthermore, the alloy exhibits excellent ductility and toughness, enabling it to withstand significant deformation without fracturing.
The corrosion resistance of Inconel 625 bars is unparalleled, resisting attack from a wide range of acids, alkalis, and salts. This property is crucial in chemical processing, marine, and other corrosive environments where materials must withstand prolonged exposure to harsh chemicals.
The alloy’s weldability is another significant advantage. It can be welded using various techniques, such as gas tungsten arc welding (GTAW) and gas metal arc welding (GMAW), without the need for pre- or post-weld heat treatment in most cases. This simplifies the manufacturing process and reduces production costs.
Due to these exceptional properties, Inconel 625 bars find widespread use in various industries. In the aerospace sector, they are used in jet engines, turbines, and other high-temperature components due to their ability to withstand extreme temperatures and maintain mechanical properties. The alloy’s corrosion resistance also makes it suitable for use in aircraft fuel systems and exhaust components.
In the oil and gas industry, Inconel 625 bars are employed in downhole drilling equipment, pipelines, and valves. They can withstand the corrosive effects of crude oil and gas, as well as the high temperatures and pressures encountered during drilling and production operations.
The nuclear industry also benefits from the use of Inconel 625 bars. Their resistance to radiation and high temperatures makes them suitable for use in nuclear reactors and associated equipment, such as fuel rods and heat exchangers.
Moreover, the chemical processing industry relies on Inconel 625 bars for the manufacture of reactors, heat exchangers, and other equipment that handles corrosive chemicals. The alloy’s corrosion resistance ensures the longevity and reliability of these critical components.
conclusion
In conclusion, Inconel 625 bars, with their unique composition and exceptional properties, are a vital material in various industries. Their high strength, corrosion resistance, and weldability make them ideal for use in high-temperature and corrosive environments.
Thank you for reading our article and we hope it can help you to have a better understanding of the composition, properties, and uses of Inconel 625 bars. If you are looking for Inconel 625 bar suppliers online now, we would advise you to visit Huaxiao Alloy.
As a leading supplier of Inconel Alloys from Shanghai China, Huaxiao Alloy offers customers high-quality Inconel 600, Inconel 601, Inconel 625, and Inconel 718 at a very competitive price.
- In ASME (American Society of Mechanical Engineers) standards, Inconel 625 is classified as a Nickel-Chromium-Molybdenum alloy with excellent resistance to oxidation and corrosion. It is specified in ASME Boiler and Pressure Vessel Code, Section II, as a material suitable for high-temperature and high-stress applications, especially in harsh environments. ASME designations for Inconel 625 include specifications for seamless and welded pipes, sheets, plates, and bars.
- Inconel 625 is widely used in industries that require materials with high strength and resistance to extreme conditions. Its primary applications include:
- Aerospace: Components in jet engines, exhaust systems, and turbine blades due to its resistance to heat and oxidation.
- Marine and Offshore: Subsea equipment, seawater processing, and marine engineering components because of its exceptional corrosion resistance.
- Chemical Processing: Heat exchangers, reactor vessels, and process piping in aggressive chemical environments.
- Nuclear: Nuclear reactors and containment systems because of its stability under high stress and radiation.
- The ASTM standards for Inconel 625 include:
- ASTM B443: Standard Specification for Nickel-Chromium-Molybdenum-Columbium Alloy (UNS N06625) Plate, Sheet, and Strip.
- ASTM B444: Standard Specification for Nickel-Chromium-Molybdenum-Columbium Alloy (UNS N06625) Seamless Pipe and Tube.
- ASTM B446: Standard Specification for Nickel-Chromium-Molybdenum-Columbium Alloy (UNS N06625) Rod and Bar.
- These standards cover various forms of Inconel 625, outlining requirements for chemical composition, mechanical properties, and heat treatment.
- The cost of Inconel 625 varies depending on market demand, form (sheet, bar, pipe), and supplier. Generally, Inconel 625 can cost between $15 to $25 per pound, although prices may fluctuate. High-grade or specialty forms (like thick plates or specific dimensions) may cost more. For precise pricing, it’s best to request a quote from suppliers as prices can vary significantly based on quantity and specifications.
- Inconel vs. Stainless Steel:
- Corrosion Resistance: Inconel 625 has superior corrosion resistance, especially in high-temperature and corrosive environments, where it outperforms most stainless steels.
- High-Temperature Performance: Inconel 625 retains its strength and oxidation resistance at higher temperatures than stainless steel, making it more suitable for high-temperature applications.
- Strength: Inconel is generally stronger at both high and low temperatures compared to stainless steel.
- Cost: Inconel is significantly more expensive than stainless steel, which makes stainless steel a more economical choice for less demanding applications.
- Conclusion: Inconel is better for extreme conditions, but for most applications where high-temperature resistance is not critical, stainless steel is a more cost-effective choice.
- 625 steel grade refers to Inconel 625, a high-performance alloy composed primarily of nickel, chromium, and molybdenum with niobium additions. It is not technically “steel” (which is iron-based), but rather a nickel-based superalloy. Its unique composition provides outstanding resistance to oxidation, corrosion, and high temperatures, making it suitable for harsh industrial environments.
Recent Blog
If you found this article good, feel free to share it on your other social media platforms.