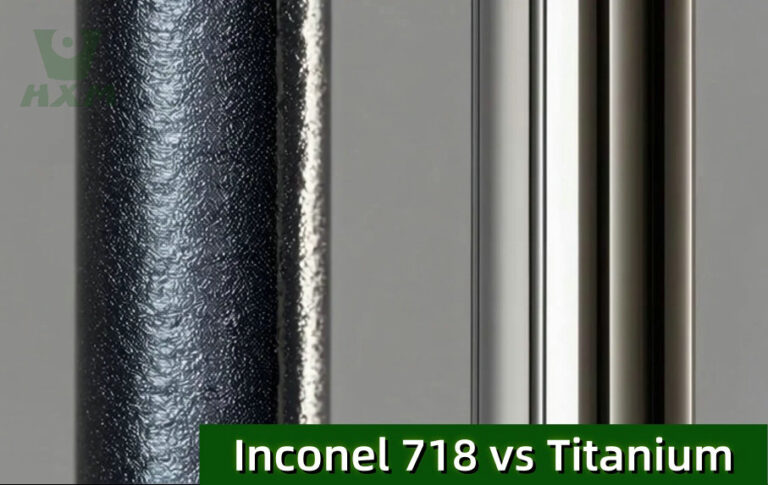
In the world of high-performance materials, Inconel 718 vs titanium each holds a unique position, offering distinct advantages and applications across various industries. While both materials excel in demanding environments, they differ significantly in their composition, properties, and usage. In this article, let’s delve into the details of these differences.
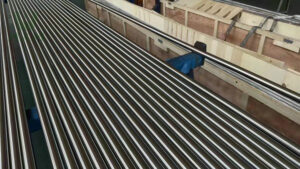
Inconel 601 UNS N06601 has excellent oxidation resistance at high temperatures, very good resistance to carbonization, can be very good oxidation resistance sulfur-containing atmosphere, at room temperature and high temperatures have very good mechanical properties very good resistance to stress corrosion cracking properties due to the control of the carbon content and grain size.
Inconel 601 has a high creep fracture strength, so in the field of 500 ℃ above the recommended use of Inconel 601.
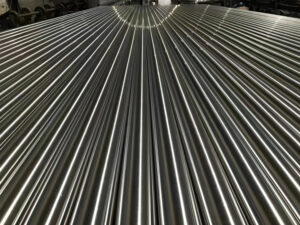
Inconel 625(UNS N06625) is a corrosion and oxidation resistant nickel alloy used for its high strength and excellent resistance to water corrosion. Its excellent strength and toughness is due to the addition of niobium, which along with molybdenum hardens the matrix of the alloy.
Alloy 625 has excellent fatigue strength and stress corrosion cracking resistance to chloride ions. This nickel alloy has excellent weldability and is often used to weld AL-6XN. This alloy is resistant to a variety of severely corrosive environments and is particularly resistant to pitting and crevice corrosion.
Inconel 718 vs Titanium
Inconel 718 vs Titanium – 1. Composition:
Inconel 718, also known as UNS N07718, is a nickel-chromium superalloy that was developed in the 1960s. It’s composed primarily of nickel, with significant amounts of chromium, iron, and other elements like molybdenum, titanium, aluminum, and cobalt added to enhance its mechanical properties. This complex composition gives Inconel 718 its excellent strength, corrosion resistance, and high-temperature performance.
Titanium, on the other hand, is a transition metal with a unique combination of properties. It’s strong, lightweight, and highly resistant to corrosion. Commercially pure titanium grades, such as Grade 2 and Grade 5, are pure titanium with small amounts of other elements added to improve specific properties. Titanium alloys, such as Ti-6Al-4V, further enhance these properties by adding aluminum and vanadium.
Inconel 718 vs Titanium – 2. Properties:
Inconel 718 boasts high strength and toughness, even at elevated temperatures, making it suitable for use in high-stress and high-temperature applications. Its corrosion resistance, especially against oxidizing agents, is excellent, making it suitable for use in corrosive environments. Additionally, its resistance to creep and fatigue at high temperatures makes it a prime choice for components that need to withstand long-term exposure to heat.
Titanium, on the other hand, is renowned for its lightweight properties, making it an ideal material for applications where weight reduction is critical. Its corrosion resistance, particularly in saltwater and other harsh environments, is excellent. Titanium alloys, such as Ti-6Al-4V, offer a balance of strength, ductility, and toughness, making them suitable for a wide range of applications.
Inconel 718 vs Titanium – 3. Applications:
Inconel 718’s unique combination of properties makes it a preferred material for high-performance applications in the aerospace, gas turbine, and chemical processing industries. It’s commonly used in components like turbine disks, engine mounts, and fasteners that require exceptional strength and corrosion resistance.
Titanium and its alloys are widely used in the aerospace, medical, chemical, and marine industries due to their lightweight, corrosion resistance, and biocompatibility. Titanium implants in dentistry and orthopedic surgery are common examples of its use in the medical field. In the aerospace industry, titanium is used in aircraft frames, engine components, and landing gear due to its high strength-to-weight ratio.
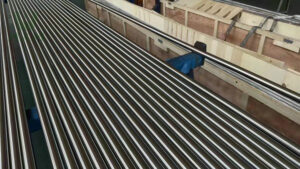
Inconel 601 UNS N06601 has excellent oxidation resistance at high temperatures, very good resistance to carbonization, can be very good oxidation resistance sulfur-containing atmosphere, at room temperature and high temperatures have very good mechanical properties very good resistance to stress corrosion cracking properties due to the control of the carbon content and grain size.
Inconel 601 has a high creep fracture strength, so in the field of 500 ℃ above the recommended use of Inconel 601.
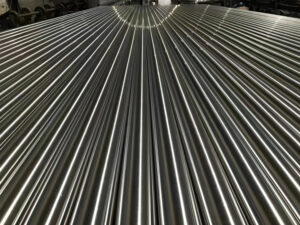
Inconel 625(UNS N06625) is a corrosion and oxidation resistant nickel alloy used for its high strength and excellent resistance to water corrosion. Its excellent strength and toughness is due to the addition of niobium, which along with molybdenum hardens the matrix of the alloy.
Alloy 625 has excellent fatigue strength and stress corrosion cracking resistance to chloride ions. This nickel alloy has excellent weldability and is often used to weld AL-6XN. This alloy is resistant to a variety of severely corrosive environments and is particularly resistant to pitting and crevice corrosion.
Conclusion
Inconel 718 and titanium are two distinct high-performance materials with unique compositions, properties, and applications. Inconel 718 excels in high-temperature and corrosive environments, making it a preferred choice for demanding applications in the aerospace and chemical processing industries. Titanium, on the other hand, offers a unique combination of strength, lightweight, and corrosion resistance, making it ideal for weight-sensitive applications in the aerospace, medical, and marine sectors.
Thank you for reading our article. We hope it can help you to have a better understanding of the differences between Inconel 718 vs Titanium. If you are looking for Inconel 718 suppliers online now, please don’t hesitate to contact Huaxiao Alloy.
As a leading supplier of Inconel Alloys from Shanghai China, Huaxiao Alloy offers customers high-quality high-temperature alloys such as Monel K500 and Monel 400, Inconel 602 alloy, Hastelloy S Alloy, Inconel Alloy 600, Inconel Alloy 601, Inconel 625 UNS N06625, Hastelloy B3 (UNS N10675), Hastelloy D205, Hastelloy G30 (UNS N06030), and Hastelloy C-2000 at a very competitive price.
Inconel 718 is generally stronger than titanium in terms of yield strength and high-temperature strength, particularly at elevated temperatures. However, the comparison depends on the grade of titanium being considered:
- At Room Temperature: Inconel 718 has a higher tensile and yield strength than commercially pure titanium but is comparable to titanium alloys like Ti-6Al-4V.
- At High Temperatures: Inconel 718 maintains its mechanical properties better than titanium alloys, making it a preferred choice for applications like jet engines and gas turbines.
- Weight-to-Strength Ratio: Titanium alloys outperform Inconel in terms of weight-to-strength ratio, as titanium is much lighter.
Some disadvantages of Inconel 718 include:
- Cost: It is significantly more expensive than many other materials due to its complex manufacturing process and high nickel content.
- Density: Inconel 718 is relatively heavy compared to materials like titanium and aluminum, which can be a drawback in weight-sensitive applications.
- Machinability: The alloy is difficult to machine due to its high strength and work-hardening characteristics, requiring specialized tools and techniques.
- Corrosion in Specific Environments: While it is highly resistant to corrosion in many environments, Inconel 718 may not perform as well in extremely reducing or sulfur-rich conditions.
Materials that are comparable to Inconel 718 include:
- Waspaloy: Another nickel-based superalloy with excellent high-temperature strength, often used in aerospace applications.
- Haynes 718: Similar in composition and properties, suitable for the same high-performance applications.
- Alloy 625: While not as strong at high temperatures as 718, Alloy 625 offers superior corrosion resistance and is used in marine and chemical environments.
- Maraging Steel: Offers similar strength but is not as corrosion-resistant or temperature-resistant as Inconel 718.
No, Inconel is generally more expensive than titanium due to:
- The high cost of raw materials (nickel and chromium).
- Complex and energy-intensive manufacturing processes.
- Specialized machining and fabrication requirements.
However, titanium can become more expensive for certain high-grade or rare alloys, especially those designed for aerospace or medical applications.
Inconel 718 is expensive due to several factors:
- Raw Materials: It contains high amounts of nickel and chromium, which are costly.
- Manufacturing Process: The production involves precise control of alloying elements and heat treatments to achieve desired properties.
- Machining Difficulties: Inconel is tough and work-hardens, increasing tooling costs and manufacturing time.
- Specialized Applications: It is designed for critical applications in aerospace, defense, and energy sectors, where performance outweighs cost considerations.
The term “better” depends on the application. Some metals outperform titanium in specific areas:
- Inconel: Superior in high-temperature and high-strength applications but heavier.
- Steel: Offers better toughness and strength in some grades, especially tool steels, but is heavier and less corrosion-resistant.
- Tungsten: Exceptional in hardness and melting point, but it is very dense and brittle.
- Carbon Fiber (not a metal): Superior strength-to-weight ratio for lightweight applications but lacks the thermal properties of titanium.
The strongest metals based on yield strength, hardness, and tensile strength are:
- Tungsten: The strongest natural metal with the highest melting point and tensile strength.
- Chromium: Known for its high hardness and corrosion resistance.
- Titanium Alloys: Exceptional strength-to-weight ratio, used extensively in aerospace and medical applications.
- Inconel: High strength, particularly at elevated temperatures, used in extreme environments.
- Steel Alloys: Tool steels and maraging steels offer impressive strength and durability.
The best alternative to titanium depends on the application:
- Aluminum Alloys: Lightweight and cost-effective for applications where extreme strength is not critical.
- Stainless Steel: Durable, corrosion-resistant, and cost-effective, but heavier than titanium.
- Inconel: Ideal for high-temperature or extreme environments, though heavier and costlier.
- Carbon Fiber: Excellent strength-to-weight ratio for lightweight applications like sports equipment or aerospace structures.
Materials that “beat” titanium vary by specific properties:
- Strength: Tungsten and some tool steels are stronger but much heavier.
- Corrosion Resistance: Inconel and other nickel-based alloys can resist more aggressive environments.
- Temperature Resistance: Tungsten and Inconel outperform titanium at extreme temperatures.
- Lightweight Alternatives: Carbon fiber has a better strength-to-weight ratio but lacks the thermal and chemical properties of titanium.