Inconel 82 filler wire, as a highly specialized material within the realm of nickel-based alloys, holds a pivotal position in various industrial applications. In this article, I will delve into the composition, properties, and uses of Inconel 82 filler wire, providing a comprehensive and authoritative overview.
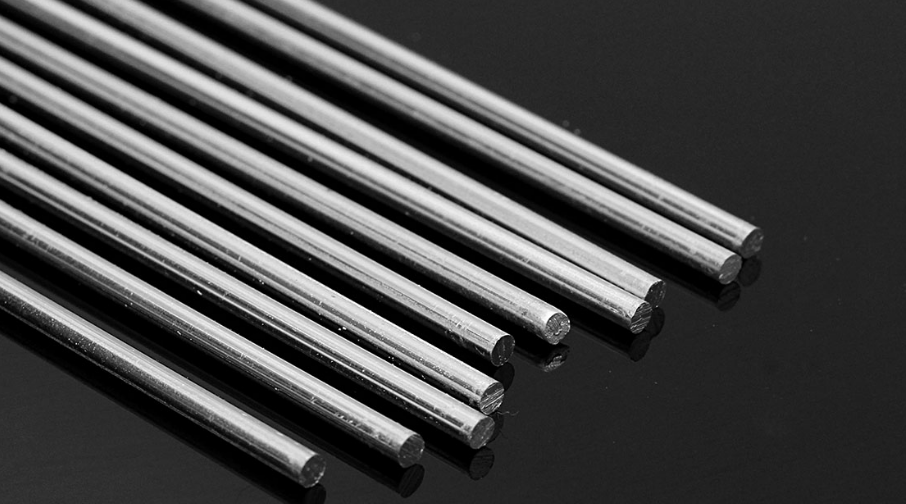
Inconel 82 Filler Wire – Composition, Properties, and Uses
1. Composition
The composition of Inconel 82 filler wire is tailored to offer exceptional performance in high-temperature environments. Primarily, it consists of a high percentage of nickel, which forms the basis of its excellent corrosion resistance and thermal stability. Additionally, chromium and iron are key components that contribute to the alloy’s overall strength and ductility. The precise balance of these elements, along with trace amounts of other alloys such as titanium and aluminum, ensures that Inconel 82 filler wire possesses the desired mechanical and chemical properties.
2. Properties
The properties of Inconel 82 filler wire are what make it a standout material in its class. Firstly, its high nickel content ensures excellent resistance to oxidation and corrosion, even in extreme environments. This allows it to retain its integrity and performance over long periods of exposure to high temperatures and corrosive media.
Moreover, Inconel 82 filler wire exhibits remarkable strength and ductility. Its ability to withstand significant mechanical loads without fracturing or deforming makes it ideal for welding applications that require high-quality joints. Its ductility ensures that the wire can be easily formed and manipulated during the welding process, reducing the risk of weld defects and ensuring a smooth, uniform weld bead.
Additionally, Inconel 82 filler wire demonstrates excellent thermal stability. This means that it maintains its mechanical properties even when exposed to extreme temperatures, making it suitable for use in high-temperature applications such as turbine engines, exhaust systems, and other heat-intensive components.
3. Uses
The versatility and performance of Inconel 82 filler wire have made it a crucial material in numerous industrial sectors. Its primary use lies in welding applications where high-temperature resistance and corrosion resistance are paramount. For instance, it is widely used in the aerospace industry for welding components that are exposed to extreme heat and corrosive environments, such as turbine blades and engine parts.
Furthermore, Inconel 82 filler wire finds applications in the chemical processing industry, where resistance to various chemical agents is essential. Its ability to withstand corrosive chemicals makes it a suitable choice for welding pipes, tanks, and other equipment used in chemical processing plants.
Additionally, the oil and gas industry also benefits from the use of Inconel 82 filler wire. In offshore drilling and pipeline construction, the material’s resistance to seawater corrosion and high-temperature stability are crucial for ensuring the integrity and longevity of welded joints.
Conclusion
Inconel 82 filler wire, with its unique composition and exceptional properties, has established itself as a key material in various industrial welding applications. Its high-temperature resistance, corrosion resistance, and mechanical strength make it an ideal choice for welding components that operate in extreme environments.
Thank you for reading our article and we hope you’ve enjoyed it. If you are looking for Inconel 82 Filler Wire suppliers online now, we would advise you to visit Huaxiao Alloy for more information.
As a leading supplier of Inconel Alloys from Shanghai China, Huaxiao Alloy offers customers high-quality Inconel 82 Filler Wire, Inconel X750, Inconel 625 Alloy, Inconel 602 Alloy, and Inconel Alloy 601 at a very competitive price