Inconel, a nickel-based superalloy, has established itself as a cornerstone in the high-performance material sector due to its exceptional properties such as high temperature resistance, corrosion resistance, and mechanical strength. Its widespread applications in aerospace, oil and gas, chemical processing, and energy sectors have made Inconel machining a crucial skill for modern manufacturers. This article delves into the intricacies of Inconel machining, providing insights into its material characteristics, machining challenges, recommended techniques, and best practices.
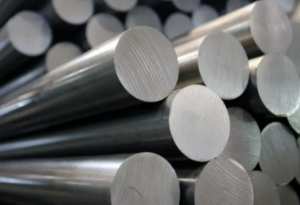
Material Characteristics of Inconel
Inconel alloys are characterized by their nickel-rich composition, often containing chromium, molybdenum, and other alloying elements. These elements contribute to the alloy’s excellent corrosion resistance, even in oxidizing and reducing environments. The addition of aluminum and titanium enables the formation of strengthening precipitates, enhancing the material’s mechanical properties at high temperatures.
The high thermal stability of Inconel alloys allows them to retain their strength and ductility even at temperatures exceeding 1000°C. However, this same property also poses challenges during machining operations, as the material’s hardness and thermal conductivity affect tool wear and heat generation.
Machining Challenges of Inconel
Machining Inconel alloys presents several challenges due to their unique material properties. The high hardness and toughness of Inconel require the use of specialized cutting tools and techniques. Additionally, the material’s low thermal conductivity results in increased heat generation during machining, leading to tool wear and potential workpiece distortion.
Furthermore, the tendency of Inconel to work harden under cutting pressures can exacerbate tool wear and shorten tool life. This necessitates the use of tools with high-temperature resistance and wear resistance.
Machining Techniques for Inconel
To effectively machine Inconel alloys, it is crucial to employ the appropriate techniques and tools. Here are some recommended practices:
- Tool Selection: Choose carbide or ceramic cutting tools with high hardness and wear resistance. Coated tools, such as TiAlN or TiCN, can provide additional protection against wear and heat.
- Cutting Speeds and Feeds: Reduce cutting speeds and increase feeds to minimize heat generation and tool wear. Lower cutting speeds allow the tool to cut through the material more efficiently, while higher feeds reduce the time the tool is in contact with the workpiece.
- Cooling and Lubrication: Use high-pressure coolant systems to effectively dissipate heat and reduce tool wear. Coolants also help lubricate the cutting interface, further reducing friction and wear.
- Rigidity and Stability: Ensure the machining setup is rigid and stable to minimize vibrations that can lead to tool breakage and workpiece damage.
- Post-Processing: After machining, consider using heat treatment or stress relief techniques to minimize residual stresses and improve the workpiece’s dimensional stability.
Best Practices for Inconel Machining
Adopting best practices for Inconel machining can significantly improve efficiency, tool life, and workpiece quality. Here are some key considerations:
- Tool Condition Monitoring: Implement regular tool condition monitoring to detect wear and breakage early. This allows for timely tool replacement, minimizing downtime and scrap rates.
- Optimization of Machining Parameters: Continuously optimize cutting speeds, feeds, and depths of cut based on the specific workpiece geometry and machining requirements.
- Use of Advanced Machining Techniques: Consider employing advanced machining techniques such as high-speed machining (HSM), which can reduce cycle times and improve surface finishes.
- Quality Assurance: Implement stringent quality assurance measures to ensure that machined parts meet the required specifications and tolerances.
- Training and Education: Provide regular training to operators on the latest machining techniques and best practices for Inconel alloys. This ensures that they are equipped with the necessary skills and knowledge to handle the challenges of machining this material.
Conclusion
Machining Inconel alloys requires a combination of specialized tools, techniques, and best practices. By understanding the material’s unique properties and challenges, and adopting appropriate machining strategies, manufacturers can effectively produce high-quality parts from Inconel while minimizing tool wear and maximizing efficiency.
Thank you for reading our article and we hope it can help you to have a better understanding of Inconel machining. If you are looking for Inconel Alloy suppliers and manufacturers online now, we would advise you to visit Huaxiao Alloy.
As a leading supplier of Inconel Alloy from Shanghai China, Huaxiao Alloy offers customers high-quality Inconel 600, Inconel 601, Inconel 625, and Inconel 718 at a very competitive price.