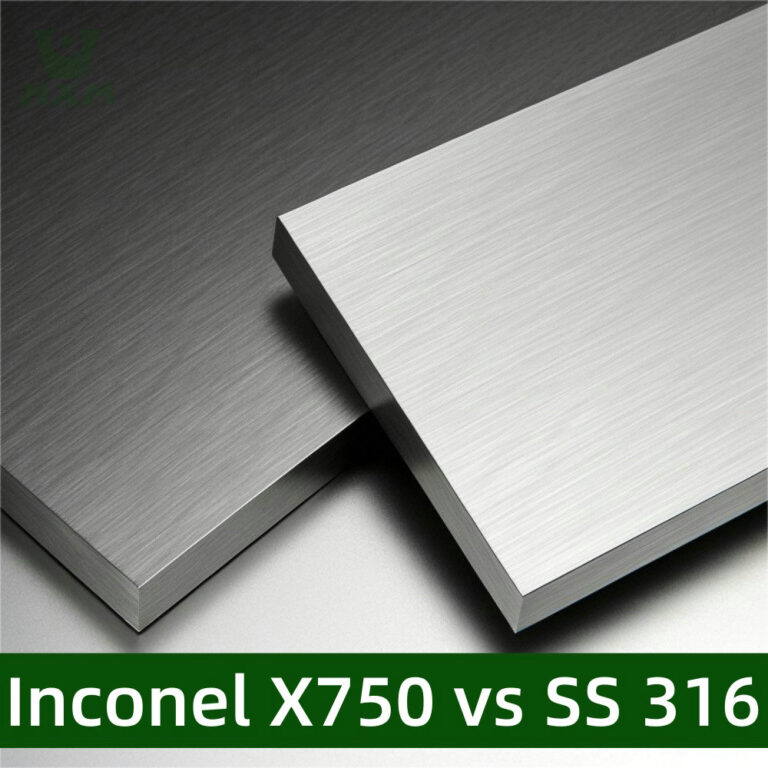
Inconel X750 vs SS 316 – 1. Composition
Inconel X750, a nickel-chromium-based alloy, is renowned for its high strength and excellent corrosion resistance. It typically contains a significant amount of nickel, chromium, and titanium, along with smaller amounts of aluminum and iron. The addition of titanium in Inconel X750 helps stabilize the alloy against sensitization and intergranular corrosion.
On the other hand, SS 316 is a molybdenum-bearing austenitic stainless steel. Its composition primarily consists of iron, chromium, nickel, and molybdenum. The molybdenum content gives SS 316 superior corrosion resistance, particularly against chloride ions, compared to other stainless steel grades.
The key difference between Inconel X750 and SS 316 lies in their chemical composition, which directly impacts their properties and performance.
-
Inconel X750:
-
Nickel (Ni): 70% (primary element)
-
Chromium (Cr): 14-17%
-
Iron (Fe): 5-9%
-
Niobium (Nb): 0.7-1.2%
-
Titanium (Ti): 2.25-2.75%
-
Aluminum (Al): 0.4-1.0%
-
Other elements: Small amounts of cobalt, manganese, and copper.
Inconel X750 is a nickel-chromium superalloy with added titanium and aluminum, which enable it to achieve high strength through precipitation hardening.
-
-
SS 316:
-
Iron (Fe): 60-65% (primary element)
-
Chromium (Cr): 16-18%
-
Nickel (Ni): 10-14%
-
Molybdenum (Mo): 2-3%
-
Manganese (Mn): 2% max
-
Other elements: Small amounts of silicon, phosphorus, sulfur, and carbon.
SS 316 is an austenitic stainless steel with added molybdenum, which enhances its corrosion resistance, especially in chloride environments.
-
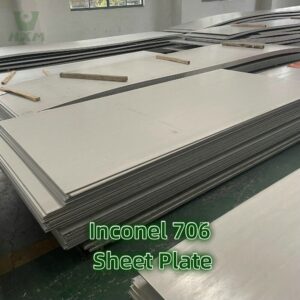
Inconel 706 Sheet / Plate / Coil
Huaxiao-Alloy, a trusted Inconel 706 sheet manufacturer, delivers ASTM/ASME-certified sheets, plates, and coils with unmatched high-temperature strength and weldability for aerospace, power generation, and oil & gas industries.

Inconel 718 Sheet / Plate / Coil
Huaxiao-Alloy, a trusted Inconel 718 sheet manufacturer, delivers ASTM/ASME-certified sheets, plates, and coils with unmatched high-temperature strength and corrosion resistance for aerospace, oil & gas, and energy industries.
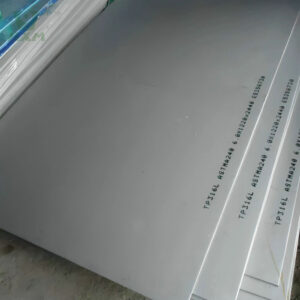
316 / 316L Stainless Steel Sheet&Plate
Huaxiao Alloy is a professional stainless steel supplier, specializing in high-quality stainless steel sheets and plates for global industries. Our TP316 / 316L stainless steel sheets and plates are manufactured to international standards, ensuring excellent corrosion resistance, durability, and reliability for demanding applications.
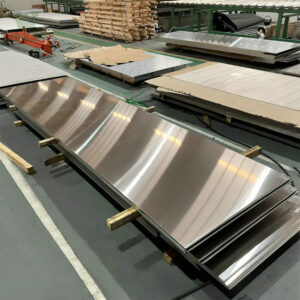
304 / 304L Stainless Steel Sheet&Plate
Huaxiao Alloy is a professional stainless steel supplier dedicated to providing high-quality materials for global industries. Our 304 / 304L stainless steel sheets and plates are manufactured to meet international standards, ensuring superior performance in various applications.
Inconel X750 vs SS 316 – 2. Mechanical Properties
Inconel X750 exhibits high tensile strength and ductility, making it suitable for applications that require both strength and the ability to be formed or worked. It also maintains its mechanical properties at elevated temperatures, making it a preferred choice for high-temperature applications.
SS 316, while not as strong as Inconel X750, still possesses good mechanical properties. It is tougher and more ductile than some other stainless steel grades, allowing it to be used in a wide range of applications. However, its strength and ductility may not match those of Inconel X750 in extreme conditions.
Inconel X750 vs SS 316 – 3. Corrosion Resistance
Both Inconel X750 and SS 316 are known for their excellent corrosion resistance. Inconel X750’s corrosion resistance is attributed to its nickel and chromium content, which forms a protective oxide layer on the surface of the alloy. This layer effectively resists attack from various corrosive agents, including acids, alkalis, and saltwater.
SS 316’s corrosion resistance is enhanced by the addition of molybdenum, which significantly improves its resistance to chloride-induced corrosion. This makes SS 316 particularly suitable for applications in marine environments and other chloride-rich conditions.
Property | Inconel X750 | SS 316 |
---|---|---|
Corrosion Resistance | Excellent resistance to oxidation and high-temperature corrosion. | Excellent resistance to pitting and crevice corrosion, especially in chloride environments. |
Strength | Extremely high strength, especially at elevated temperatures. | Moderate strength, suitable for general-purpose applications. |
Temperature Resistance | Performs well in extreme temperatures (up to 1300°F/700°C). | Performs well in moderate temperatures (up to 800°F/427°C). |
Hardness | High hardness due to precipitation hardening. | Lower hardness compared to Inconel X750. |
Magnetic Properties | Non-magnetic. | Non-magnetic in annealed condition. |
Machinability | Difficult to machine due to high strength. | Easier to machine compared to Inconel X750. |
Weldability | Requires specialized welding techniques. | Easier to weld with standard techniques. |
Inconel X750 vs SS 316 – 4. Applications
-
Inconel X750 Applications:
-
Aerospace: Jet engine components, gas turbine blades, and rocket engines.
-
Nuclear Industry: Reactor core components and fuel assembly parts.
-
Oil and Gas: High-temperature fasteners, valves, and downhole tools.
-
Industrial Gas Turbines: Turbine wheels and seals.
-
High-Temperature Springs: Used in extreme environments.
-
-
SS 316 Applications:
-
Marine Industry: Boat fittings, propeller shafts, and offshore platforms.
-
Food and Beverage: Processing equipment, storage tanks, and piping.
-
Pharmaceutical: Surgical instruments, implants, and sterilization equipment.
-
Chemical Industry: Tanks, valves, and piping for corrosive chemicals.
-
Architecture: Decorative panels, handrails, and structural components.
-
Due to its high strength and excellent corrosion resistance, Inconel X750 is widely used in the aerospace, chemical processing, and nuclear industries. It is often found in turbine engines, exhaust systems, and other high-temperature, high-stress components.
SS 316, on the other hand, is a popular choice for applications that require good corrosion resistance, such as marine equipment, chemical tanks, and food processing equipment. Its ability to withstand chloride-induced corrosion makes it a preferred material for use in coastal areas and other environments exposed to saltwater.
Cost: Which is More Economical?
-
Inconel X750: Due to its high nickel content and specialized manufacturing process, Inconel X750 is significantly more expensive than SS 316. It is typically used in high-performance applications where cost is secondary to performance.
-
SS 316: SS 316 is more cost-effective and widely available, making it a popular choice for general-purpose applications.
Which One Should You Choose?
The choice between Inconel X750 and SS 316 depends on your specific requirements:
-
Choose Inconel X750 if:
-
You need exceptional strength and performance at high temperatures.
-
Your application involves extreme environments, such as aerospace or nuclear industries.
-
Corrosion resistance in highly oxidizing environments is critical.
-
-
Choose SS 316 if:
-
You need a cost-effective material with good corrosion resistance.
-
Your application involves exposure to chlorides, such as in marine or chemical environments.
-
You require a material that is easier to machine and weld.
-
Why Choose Huaxiao Alloy?
In summary, Inconel X750 and SS 316 are both excellent alloys with unique properties and applications. Inconel X750 excels in high-temperature and high-stress environments due to its high strength and corrosion resistance. SS 316, on the other hand, is renowned for its corrosion resistance, particularly against chloride ions, making it suitable for marine and chemical applications.
Thank you for reading our article and we hope it can help you to have a better understanding of the differences between Inconel X750 vs SS 316. If you are looking for Inconel X750 suppliers online now, we would advise you to visit Huaxiao Alloy.
As a leading supplier of Inconel Alloy from Shanghai China, Huaxiao Alloy offers high-quality Inconel X750, Inconel 625 Alloy, Inconel 602 Alloy, and Inconel Alloy 601 at a very competitive price.
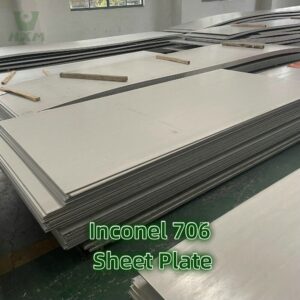
Inconel 706 Sheet / Plate / Coil
Huaxiao-Alloy, a trusted Inconel 706 sheet manufacturer, delivers ASTM/ASME-certified sheets, plates, and coils with unmatched high-temperature strength and weldability for aerospace, power generation, and oil & gas industries.

Inconel 718 Sheet / Plate / Coil
Huaxiao-Alloy, a trusted Inconel 718 sheet manufacturer, delivers ASTM/ASME-certified sheets, plates, and coils with unmatched high-temperature strength and corrosion resistance for aerospace, oil & gas, and energy industries.
Inconel and stainless steel serve different purposes, so “better” depends on the application.
- Inconel is a high-performance nickel-based superalloy designed for extreme heat, corrosion, and oxidation resistance. It performs exceptionally well in high-temperature environments (e.g., aerospace, gas turbines, and nuclear reactors).
- Stainless Steel, particularly grades like 304 and 316, is an iron-based alloy with good corrosion resistance and mechanical properties. It is widely used in marine, medical, and food processing industries due to its durability and affordability.
Key Differences:
- If high-temperature strength and oxidation resistance are required, Inconel is better.
- If cost-effectiveness and general corrosion resistance are the priority, stainless steel is the preferred choice.
Inconel X-750 is a nickel-chromium superalloy known for its:
- Excellent high-temperature strength (up to 980°C / 1800°F)
- Corrosion and oxidation resistance
- Good mechanical properties under extreme conditions
Composition:
- Nickel (≈70%), Chromium, Iron, Titanium, and Aluminum
- Strengthened through precipitation hardening
Applications:
- Aerospace (gas turbines, jet engine components)
- Nuclear power plants (springs, fasteners)
- High-performance industrial components
Property | Inconel 718 | 316 Stainless Steel |
---|---|---|
Composition | Nickel-based (Ni ~50%) | Iron-based (Fe ~60-70%) |
Temperature Resistance | Up to 700°C (1290°F) | Up to 870°C (1600°F) but loses strength |
Corrosion Resistance | Excellent in extreme environments | Very good, especially against chlorides |
Strength | High tensile & yield strength | Moderate strength |
Cost | Expensive | More affordable |
Applications | Aerospace, nuclear, high-stress environments | Marine, medical, food processing |
Key Takeaway: Inconel 718 outperforms 316 SS in high-temperature and high-strength applications, while 316 SS is a cost-effective choice for corrosion resistance in non-extreme conditions.
The strongest Inconel alloys are:
- Inconel 718 – High tensile strength (~1380 MPa), excellent creep resistance.
- Inconel 625 – Outstanding corrosion resistance with high strength.
- Inconel X-750 – Strong at elevated temperatures, commonly used in aerospace.
For room temperature and cryogenic applications, Inconel 718 is considered the strongest due to its high yield and tensile strength.
Property | Inconel 600 | Inconel X-750 |
---|---|---|
Composition | Ni (76%), Cr (15%), Fe (8%) | Ni (70%), Cr (15-17%), Fe (5-9%), Ti, Al |
Strengthening Mechanism | Solid solution strengthening | Precipitation hardening |
Temperature Resistance | Up to 1093°C (2000°F) | Up to 980°C (1800°F) |
Corrosion Resistance | Excellent in oxidation & chloride environments | Good, but optimized for high strength |
Applications | Heat exchangers, furnace components | Jet engines, nuclear reactors |
Key Takeaway:
- Inconel 600 is better for general high-temperature corrosion resistance.
- Inconel X-750 is superior for high-strength applications requiring creep resistance.
Several stainless steel grades offer superior performance to 316 in specific areas:
- 317L Stainless Steel – Higher molybdenum content, better corrosion resistance than 316.
- 904L Stainless Steel – Excellent resistance to chlorides and acids, often used in chemical industries.
- Duplex Stainless Steel (e.g., 2205, 2507) – Higher strength and superior corrosion resistance, commonly used in marine and offshore applications.
- Super Austenitic Stainless Steels (e.g., AL-6XN) – Extreme corrosion resistance, surpassing 316 in aggressive environments.
Key Takeaway:
- If better corrosion resistance is needed → 904L or AL-6XN.
- If higher strength is required → Duplex 2205 or 2507.
- If cost-effectiveness with improved performance is needed → 317L.