Monel 400
Monel 400 (UNS N04400, NCu30) The organization of Monel 400 alloy is a high-strength single-phase solid solution, which is one of the most used, most versatile, and excellent all-around corrosion-resistant alloys. This alloy has high quality corrosion resistance in hydrofluoric acid and fluorine gas media, and also has excellent corrosion resistance to hot concentrated alkaline solutions. It is also resistant to corrosion from neutral solutions, water, seawater, atmosphere, organic compounds, and so on. An important feature of this alloy is that it is generally free from stress corrosion cracks and has good cutting properties.
Chemical composition of monel 400(%)
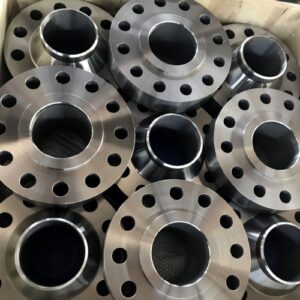
Element | Percentage (%) |
---|---|
Nickel (Ni) | 63 min |
Copper (Cu) | 28-34 |
Iron (Fe) | 2.5 max |
Manganese (Mn) | 2.0 max |
Carbon (C) | 0.3 max |
Silicon (Si) | 0.5 max |
Sulphur (S) | 0.024 max |
Content
Applications of monel 400
Monel 400’s unique properties, particularly its excellent resistance to corrosion, high strength, and ability to remain ductile at sub-zero temperatures, make it suitable for various specialized applications. Here are some key applications that leverage these unique characteristics of Monel 400:
Marine Engineering: Monel 400 is extensively used in marine engineering due to its exceptional resistance to seawater corrosion. It is utilized for marine fixtures and fasteners, boat shafts, and propellers. Its resistance to saltwater makes it an ideal choice for these applications.
Chemical Processing Industry: Due to its excellent resistance to a wide range of acids and alkalis, Monel 400 is used in chemical processing equipment. It is suitable for handling hydrofluoric acid, sulfuric acid, and hydrochloric acid, among others, used in reactors, heat exchangers, and pumps.
Petroleum Industry: Monel 400 is used in the oil and gas industry, especially in applications like valves, pumps, and piping systems that are exposed to sour gas. Its resistance to stress corrosion cracking in the presence of hydrogen sulfide is particularly valuable.
Desalination Plants: In desalination plants, Monel 400 is used for its corrosion resistance to high-velocity seawater, making it suitable for tubing and other components.
Aerospace Industry: Its high strength and resistance to corrosion make Monel 400 a good choice for certain aerospace applications, including as part of the fuel and hydraulic line systems.
Electronic and Electrical Applications: Due to its low electrical conductivity relative to other metals, Monel 400 is used in electrical and electronic applications, particularly in the manufacturing of precision resistors and other components where its properties can be advantageous.
Cryogenic Applications: Monel 400 retains its mechanical properties at very low temperatures, making it suitable for cryogenic applications. It is used in equipment handling liquefied gases like liquid oxygen, nitrogen, and natural gas.
These applications highlight the versatility of Monel 400, leveraging its unique combination of corrosion resistance, strength, and ductility in challenging and aggressive environments.
Production standards for monel 400
Product Form | Standard Specification | Description |
---|---|---|
Plate, Sheet, and Strip | ASTM B127 | This standard specifies the requirements for nickel-copper alloy (UNS N04400) plate, sheet, and strip. |
Bar, Rod, and Wire | ASTM B164 | This specification covers nickel-copper alloy (UNS N04400) rods, bars, and wires. |
Seamless Pipe and Tube | ASTM B165 | This standard specifies the requirements for nickel-copper alloy (UNS N04400) seamless pipe and tube. |
Welded Pipe | ASTM B725 | This specification covers welded nickel-copper alloy (UNS N04400) pipe. |
Welded Tube | ASTM B730 | This standard specifies the requirements for welded tube made from nickel-copper alloy (UNS N04400). |
Forgings | ASTM B564 | This specification includes nickel alloy forgings, including Monel 400. |
Physical properties of monel 400
Physical Property | Value |
---|---|
Density | 8.80 g/cm³ |
Melting Point | 1300-1350°C (2372-2462°F) |
Thermal Conductivity | 21.8 W/m·K (at 20°C) |
Specific Heat Capacity | 427 J/kg·K (at 20°C) |
Electrical Resistivity | 0.511 μΩ·m (at 20°C) |
Magnetic Permeability | Typically < 1.002 (at 200 Oersted) |
Expansion Coefficient | 13.9 x 10^-6 /°C (20-100°C) |
Mechanical properties of monel 400
Mechanical Property | Value (Annealed Condition) |
---|---|
Tensile Strength | 550-600 MPa (80-87 ksi) |
Yield Strength (0.2% Offset) | 240-345 MPa (35-50 ksi) |
Elongation | 40-45% |
Hardness | 65-70 Rockwell B |
Modulus of Elasticity | 179 GPa (26 x 10^6 psi) |
FAQs about monel 400
Monel 400 and Monel K-500 (often referred to as Monel 500) are two popular nickel-copper alloys known for their excellent corrosion resistance and strength. While they share some basic characteristics due to their nickel-copper base, there are significant differences in their compositions and properties, which make them suitable for different applications.
Monel 400:
- Composition: Monel 400 typically contains about 63% nickel, 28-34% copper, and smaller amounts of iron and manganese.
- Properties: It offers excellent resistance to seawater and steam at high temperatures, as well as to salt and caustic solutions. Monel 400 is characterized by good general corrosion resistance, good weldability, and moderate to high strength.
- Applications: It is widely used in marine engineering, chemical and hydrocarbon processing equipment, valves, pumps, shafts, fittings, fasteners, and heat exchangers.
Monel K-500:
- Composition: Monel K-500 adds aluminum (around 2.3-3.15%) and titanium (0.35-0.85%) to the nickel-copper base, which allows it to be precipitation hardened. This alteration in composition enhances its strength and hardness.
- Properties: While retaining similar corrosion resistance as Monel 400, Monel K-500 has greater strength and hardness. It is particularly resistant to sour gas environments and is non-magnetic.
- Applications: Due to its enhanced strength and resistance to wear, Monel K-500 is used in more demanding applications than Monel 400. This includes oil and gas extraction components like drill collars and instruments, pump shafts and impellers, valve components, and springs.
Key Differences:
- Strength and Hardness: Monel K-500 is stronger and harder than Monel 400 due to the addition of aluminum and titanium, which allows for age hardening.
- Magnetic Properties: Monel 400 is slightly magnetic, whereas Monel K-500 is non-magnetic.
- Corrosion Resistance: Both alloys offer excellent corrosion resistance, but their different compositions may make one more suitable than the other depending on the specific environment.
- Applications: The choice between Monel 400 and Monel K-500 often comes down to the need for higher strength and hardness (K-500) vs. the requirement for slightly better corrosion resistance and weldability (400).
In summary, the choice between Monel 400 and Monel K-500 will depend on the specific needs of the application, considering factors like required strength, exposure to corrosive environments, and any need for non-magnetic properties.
Monel 400 is slightly magnetic. Despite its high nickel content, which typically lends a non-magnetic character to alloys, the presence of other elements like iron and copper in Monel 400 imparts a small magnetic response to the alloy. However, this magnetic property is relatively weak compared to ferromagnetic materials like iron or steel. In practical applications, Monel 400 is often considered essentially non-magnetic, especially when compared to materials specifically chosen for their magnetic properties.
Monel 400 and Hastelloy C-276 are both nickel-based alloys known for their excellent corrosion resistance, but they have distinct compositions, leading to different properties and applications. Here’s a comparison of the two:
Monel 400:
- Composition: Mainly composed of nickel (about 63%) and copper (28-34%), with small amounts of iron, manganese, carbon, and silicon.
- Corrosion Resistance: Exhibits excellent resistance to a range of corrosive environments, particularly seawater, hydrofluoric acid, sulfuric acid, and hydrochloric acid. It’s also resistant to stress corrosion cracking and pitting in most fresh and industrial waters.
- Mechanical Properties: Monel 400 has good strength and ductility with a moderate to high tensile strength.
- Applications: Widely used in marine engineering, chemical and hydrocarbon processing equipment, and various applications in the oil and gas industry.
Hastelloy C-276:
- Composition: A nickel-molybdenum-chromium alloy with a significant amount of tungsten, containing approximately 57% nickel, 16% molybdenum, 16% chromium, and 4% tungsten.
- Corrosion Resistance: Known for outstanding resistance to a wide variety of chemical process environments, including strong oxidizers such as ferric and cupric chlorides, chlorine, hot contaminated media (organic and inorganic), formic and acetic acids, acetic anhydride, and seawater and brine solutions. It has excellent resistance to pitting and crevice corrosion.
- Mechanical Properties: Hastelloy C-276 has strong durability and excellent weldability, despite its high strength.
- Applications: Commonly used in pollution control, chemical processing, pulp and paper production, and waste treatment industries.
Key Differences:
- Corrosion Resistance: While both alloys offer excellent corrosion resistance, Hastelloy C-276 generally provides superior performance in more aggressive and oxidizing environments, especially where chlorides are present.
- Composition: Hastelloy C-276 has a more complex composition, with significant amounts of molybdenum and chromium, enhancing its resistance to a broader range of chemicals.
- Applications: The choice between the two often depends on the specific environment and the types of chemicals involved. Hastelloy C-276 is typically preferred in more severe corrosive conditions, particularly where oxidation is a concern.
Choosing between Monel 400 and Hastelloy C-276 depends on the specific requirements of the application, including the type of corrosive environment, mechanical strength requirements, and cost considerations.
Recent Post
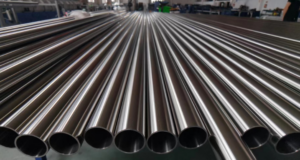
Pros and Cons of Monel Alloy: What You Should Know
Monel alloy, known for its remarkable resistance to corrosion and high strength, is a preferred material in various demanding applications. Whether you’re considering it for
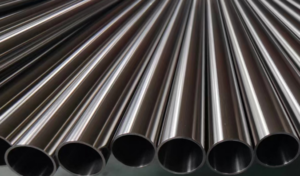
Factors Affecting the Corrosion Resistance Duration of Monel Alloy
Monel alloy, a superior nickel-based alloy, enjoys widespread applications across numerous industrial sectors due to its unique chemical composition, which enables it to exhibit outstanding
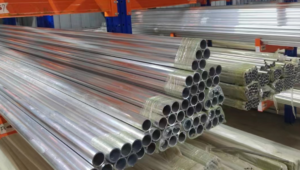
Monel Alloy Welding Performance and Techniques
Monel alloy, as a high-strength nickel-copper series alloy, boasts exceptional heat resistance and corrosion resistance, making it widely applicable across numerous industries. However, despite its