Inconel Pipe
Product grades: Inconel 600, Inconel 625, Inconel 718, N07718, W.Nr. 2.4668, NiCr19Fe19Nb5Mo3, NA 51, NC19FeNb
Implementation standards: ASTM B163, ASTM B167, ASTM B444, and ASTM B829
Certification: ISO9001:2015
Features: Exceptional creep rupture strength, exceeding 140 MPa at 700°C, ensuring outstanding long-term stability in high-temperature environments.
Product usage: Aerospace, chemical, and marine industries.
MOQ: 500KG
Payment method: T/T, LC
Price: To negotiate
Inconel pipes are high-performance alloy pipes known for their exceptional resistance to high temperatures, oxidation, and corrosion, making them ideal for demanding industrial applications in aerospace, chemical processing, power generation, and marine engineering.
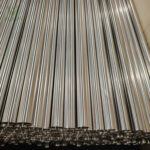
Dimensions of Inconel Pipe standard specifications
Nominal Pipe Size (NPS) | Outer Diameter (OD) (inches) | Outer Diameter (OD) (mm) | Schedule 10 Wall Thickness (inches) | Schedule 40 Wall Thickness (inches) | Schedule 80 Wall Thickness (inches) |
---|---|---|---|---|---|
1/8 | 0.405 | 10.29 | 0.049 | 0.068 | 0.095 |
1/4 | 0.540 | 13.72 | 0.065 | 0.088 | 0.119 |
3/8 | 0.675 | 17.15 | 0.065 | 0.091 | 0.126 |
1/2 | 0.840 | 21.34 | 0.083 | 0.109 | 0.147 |
3/4 | 1.050 | 26.67 | 0.083 | 0.113 | 0.154 |
1 | 1.315 | 33.40 | 0.109 | 0.133 | 0.179 |
1-1/4 | 1.660 | 42.16 | 0.109 | 0.140 | 0.191 |
1-1/2 | 1.900 | 48.26 | 0.109 | 0.145 | 0.200 |
2 | 2.375 | 60.33 | 0.109 | 0.154 | 0.218 |
2-1/2 | 2.875 | 73.03 | 0.120 | 0.203 | 0.276 |
3 | 3.500 | 88.90 | 0.120 | 0.216 | 0.300 |
4 | 4.500 | 114.30 | 0.120 | 0.237 | 0.337 |
5 | 5.563 | 141.30 | 0.134 | 0.258 | 0.375 |
6 | 6.625 | 168.28 | 0.134 | 0.280 | 0.432 |
8 | 8.625 | 219.08 | 0.148 | 0.322 | 0.500 |
10 | 10.750 | 273.05 | 0.165 | 0.365 | 0.500 |
12 | 12.750 | 323.85 | 0.180 | 0.375 | 0.500 |
14 | 14.000 | 355.60 | 0.188 | 0.375 | 0.500 |
16 | 16.000 | 406.40 | 0.188 | 0.375 | 0.500 |
18 | 18.000 | 457.20 | 0.188 | 0.375 | 0.500 |
20 | 20.000 | 508.00 | 0.218 | 0.375 | 0.500 |
24 | 24.000 | 609.60 | 0.218 | 0.375 | 0.500 |
Different grades of Inconel alloy
Mechanical Properties of Inconel Pipe
Alloy Grade | Density (g/cm³) | Melting Point (°C) | Specific Heat Capacity (J/kg·K) | Thermal Conductivity (W/m·K) | Thermal Expansion Coefficient (µm/m·K) | Electrical Resistivity (µΩ·cm) | Hardness (HB) |
---|---|---|---|---|---|---|---|
Inconel 600 Pipe | 8.47 | 1370-1425 | 444 | 14.9 | 13.3 | 128 | 150-190 |
Inconel 625 Pipe | 8.44 | 1290-1350 | 419 | 9.8 | 12.8 | 134 | 150-180 |
Inconel 718 Pipe | 8.19 | 1260-1336 | 435 | 11.4 | 13.0 | 125 | 180-220 |
Inconel 800 Pipe | 7.94 | 1357-1385 | 460 | 11.3 | 13.7 | 107 | 160-200 |
Advantages of each inconel pipe grade
Inconel 600 Pipe
Advantages:
- Corrosion Resistance: Exceptional resistance to oxidation and corrosion at high temperatures, making it ideal for applications in the chemical and aerospace industries. Among these grades, Inconel 600 is the best for environments requiring oxidation resistance.
- High Temperature Strength: Maintains high strength and stability at temperatures up to 700°C (1300°F), suitable for furnace components and heat exchangers. Compared to the other grades, it offers a balance of properties without the specialized enhancements of Inconel 625 or 718.
- Versatility: Good performance in both oxidizing and reducing environments, making it more versatile than Inconel 800.
Inconel 625 Pipe
Advantages:
- High Strength: Outstanding tensile and creep-rupture strength, especially at high temperatures up to 982°C (1800°F), making it the strongest among these grades for high-temperature applications.
- Corrosion Resistance: Superior resistance to a wide range of corrosive environments, including pitting and crevice corrosion. It surpasses Inconel 600 and 800 in terms of corrosion resistance in harsh environments.
- Fabricability: Excellent weldability and fabricability, allowing for complex and critical part manufacturing. Inconel 625 is the best choice for applications requiring extensive fabrication.
Inconel 718 Pipe
Advantages:
- Mechanical Properties: Exceptional mechanical properties, particularly at cryogenic temperatures up to 704°C (1300°F), ideal for gas turbines and aerospace engines. Among the listed grades, Inconel 718 offers the best combination of high strength and toughness at low temperatures.
- Creep and Stress-Rupture: High resistance to creep and stress-rupture at elevated temperatures, ensuring longevity and reliability in extreme conditions. It outperforms Inconel 600 and 800 in maintaining strength over prolonged high-temperature exposure.
- Ease of Fabrication: Good formability and machinability, suitable for producing intricate components. While Inconel 625 also offers good fabricability, Inconel 718 provides a better balance of properties for aerospace components.
Inconel 800 Pipe
Advantages:
- Stability: Excellent structural stability and resistance to carburization, oxidation, and nitridation, making it ideal for heat-treating equipment. It provides superior stability compared to Inconel 600 and 625 at elevated temperatures.
- Thermal Expansion: Lower thermal expansion coefficient compared to other grades, reducing thermal fatigue in cyclic temperature conditions. It is the best choice among these grades for applications involving frequent temperature changes.
- Strength: High strength at elevated temperatures, suitable for applications in nuclear and petrochemical industries. While not as strong as Inconel 625, it offers sufficient strength combined with excellent stability.
Each grade of Inconel pipe has its unique advantages tailored to specific applications, ensuring optimal performance under different operating conditions. The comparisons highlight the most notable attributes of each grade relative to the others.
Applications of Inconel Pipes
1. Aerospace Industry:
- Jet Engines and Turbines: Inconel pipes are used extensively in jet engines and gas turbines due to their ability to maintain strength and resist oxidation at high temperatures. Specifically, Inconel 718 is preferred for turbine blades, seals, and combustion chamber parts, where high mechanical strength and creep resistance are critical.
- Spacecraft: Inconel materials are used in rocket engines and other spacecraft components that require excellent performance in extreme temperatures and corrosive environments.
2. Chemical Processing:
- Heat Exchangers and Reactors: Inconel 625 pipes are widely used in heat exchangers and reactor vessels within the chemical processing industry. Their superior resistance to a wide range of corrosive chemicals, including acids and alkalis, makes them ideal for such applications.
- Piping Systems: The excellent oxidation and corrosion resistance of Inconel 600 pipes make them suitable for piping systems in harsh chemical environments, ensuring longevity and reliability.
3. Power Generation:
- Nuclear Reactors: Inconel 800 pipes are used in steam generator tubing and other components within nuclear reactors due to their structural stability and resistance to oxidation and carburization at high temperatures. This makes them crucial for maintaining the integrity of reactor systems.
- Superheater and Reheater Tubes: Inconel 600 and Inconel 625 pipes are employed in superheater and reheater tubes in fossil fuel power plants, where they endure high temperatures and corrosive flue gases.
4. Marine Engineering:
- Offshore Oil and Gas Extraction: Inconel 625 pipes are extensively used in offshore platforms and undersea pipelines due to their outstanding resistance to seawater corrosion and high mechanical strength. They are essential for subsea systems, risers, and flexible pipe connections.
- Shipbuilding: The durability and corrosion resistance of Inconel pipes make them suitable for critical ship components exposed to harsh marine environments.
5. Automotive Industry:
- Exhaust Systems: Inconel 625 pipes are used in high-performance and racing car exhaust systems due to their ability to withstand high temperatures and corrosive exhaust gases, ensuring improved performance and durability.
- Turbochargers: The use of Inconel in turbocharger components helps in maintaining efficiency and performance under extreme conditions.
6. Environmental Control:
- Pollution Control Equipment: Inconel pipes are used in equipment designed to control and reduce environmental pollution, such as scrubbers and heat exchangers in waste treatment facilities, due to their resistance to high-temperature corrosive gases and chemicals.
- Desalination Plants: Inconel 625 and 718 pipes are crucial in desalination plants for their resistance to saltwater corrosion and high-pressure environments, ensuring efficient and reliable fresh water production.
7. Medical Industry:
- Medical Devices: The biocompatibility, corrosion resistance, and strength of Inconel alloys make them suitable for certain medical devices and surgical instruments that require high reliability and performance under bodily conditions.
Conclusion
Inconel pipes are essential across various industries due to their exceptional properties, including high-temperature strength, corrosion resistance, and structural stability. Their application spans critical sectors like aerospace, chemical processing, power generation, marine engineering, automotive, environmental control, and even medical devices. The widespread use of Inconel pipes in these areas underscores their significance in advancing technology and ensuring safety and efficiency in extreme and demanding conditions.
Inconel piping refers to pipes made from Inconel, a family of nickel-chromium-based superalloys designed for exceptional resistance to high temperatures, oxidation, and corrosion. These pipes are used in highly demanding environments where other materials would fail.
Inconel material is used in applications requiring high strength and resistance to heat and corrosion. Common uses include aerospace components such as jet engines and gas turbines, chemical processing equipment, nuclear reactors, marine engineering, and high-performance automotive parts.
Inconel is generally considered better than stainless steel for high-temperature and highly corrosive environments due to its superior oxidation and corrosion resistance. However, stainless steel is often preferred for lower-cost and less extreme applications.
The main difference between Inconel and 316 stainless steel lies in their composition and performance characteristics. Inconel, a nickel-chromium alloy, offers superior resistance to high temperatures and severe corrosion, while 316 stainless steel, an iron-based alloy with chromium and nickel, provides good corrosion resistance but is less effective at high temperatures and in highly corrosive environments.
The primary disadvantages of Inconel are its high cost and difficulty in machining. Inconel’s superior performance in extreme conditions comes at a significantly higher price compared to other materials, and its high strength and hardness make it challenging to work with during manufacturing.
The choice between Inconel and Hastelloy depends on the specific application requirements. Hastelloy, another high-performance nickel-based alloy, generally offers better corrosion resistance, especially in reducing and acidic environments. Inconel, on the other hand, provides better performance at very high temperatures. The decision should be based on the specific environmental and operational conditions of the intended application.