The aerospace industry demands materials that can withstand the harshest environments, enduring extreme temperatures, corrosive atmospheres, and high mechanical loads. High-temperature alloys have emerged as the front-runners in meeting these stringent requirements. In this article, we have compiled a list of the top 10 high-temperature alloys that are currently revolutionizing aerospace applications.
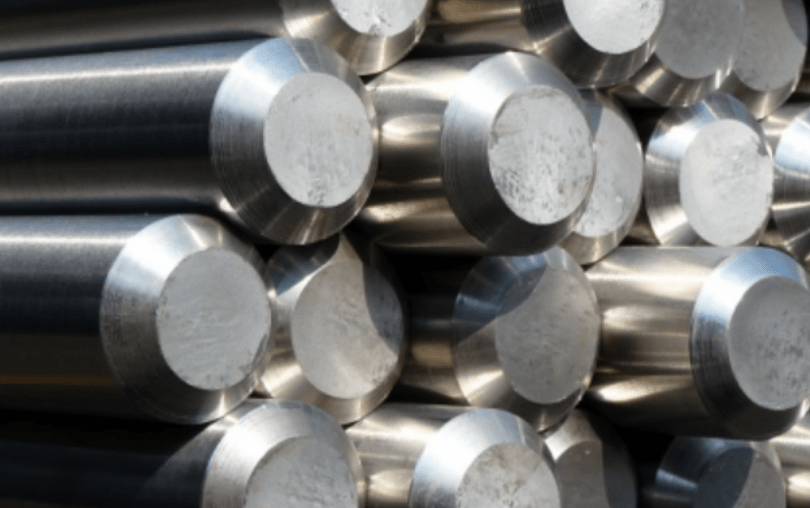
Top 10 High-Temperature Alloys for Aerospace Applications:
- Inconel 718: This nickel-based superalloy is a workhorse in the aerospace industry. Its combination of high strength, excellent corrosion resistance, and outstanding weldability makes it a preferred choice for turbine blades, disks, and other critical engine components.
- Inconel 625: Possessing excellent oxidation and corrosion resistance, Inconel 625 is a nickel-chromium–molybdenum alloy that finds extensive use in jet engines, rocket motors, and other high-temperature applications. Its high ductility and toughness also contribute to its widespread use.
- Hastelloy X: This cobalt-chromium-nickel alloy is renowned for its exceptional resistance to oxidation and corrosion at temperatures up to 2200°F. It is commonly used in gas turbine engines, combustion chambers, and other high-temperature components.
- Titanium Alloys (Ti-6Al-4V): Lightweight and strong, titanium alloys offer excellent high-temperature properties and corrosion resistance. Ti-6Al-4V is a particularly popular alloy in aerospace due to its balance of strength, ductility, and weldability. It is used in aircraft structures, engine components, and even landing gear.
- René 41: This cobalt-based alloy is known for its high strength and excellent oxidation resistance at temperatures exceeding 1800°F. René 41 finds application in turbine blades and other high-stress, high-temperature components.
- Waspaloy: A nickel-based superalloy, Waspaloy exhibits excellent strength and creep resistance at elevated temperatures. It is often used in turbine disks and shafts where high performance and durability are crucial.
- Inconel X-750: This nickel-chromium alloy is renowned for its stability and resistance to corrosion and oxidation. It is commonly used in turbine seals, exhaust systems, and other components that require good high-temperature performance.
- Mar-M 247: A nickel-cobalt-chromium alloy, Mar-M 247 offers exceptional strength and oxidation resistance at temperatures approaching 2000°F. It is used in turbine blades and other critical engine parts that operate in extreme environments.
- CMSX-4: This single-crystal nickel-based superalloy is designed for ultra-high-temperature applications. Its unique microstructure confers exceptional creep resistance and mechanical strength, making it suitable for the hottest sections of jet engines.
- Rene N5: Another cobalt-based alloy, Rene N5 is noted for its high tensile strength and resistance to creep deformation at temperatures up to 1900°F. It finds application in turbine blades and vanes that require exceptional mechanical properties at elevated temperatures.
The selection of these alloys is based on their unique combinations of mechanical properties, corrosion resistance, and thermal stability. However, it is important to note that the choice of the most suitable alloy for a specific aerospace application depends on a range of factors, including the operating temperature, the corrosive environment, the mechanical loads, and the desired weight reduction. As such, it is crucial to consult with materials experts and conduct detailed engineering analyses to ensure the selection of the optimal alloy for each application.
Conclusion
In conclusion, the top 10 high-temperature alloys listed above represent the cream of the crop in aerospace applications. Their exceptional properties and performance make them indispensable in meeting the stringent demands of the aerospace industry. As technology continues to evolve, we can expect to see even more innovative alloys emerge that will further enhance the performance and reliability of aerospace systems.