The debate surrounding the superiority of Inconel or Hastelloy is as enduring as it is complex. Both alloys are renowned for their unique properties and applications in diverse industrial settings, making a direct comparison challenging. In this blog post, we will offer an analysis of these two alloys, striving to provide an accurate, professional, and authoritative assessment.
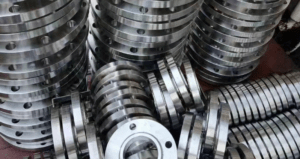
Which is better Inconel or Hastelloy?
Inconel, a nickel-chromium-based superalloy, is renowned for its excellent high-temperature performance and corrosion resistance. Its strength and ductility are remarkable, even under extreme thermal conditions, making it a preferred choice for applications such as jet engines, turbines, and nuclear reactors. The alloy’s ability to maintain its mechanical properties at elevated temperatures is a testament to its engineering prowess. Furthermore, Inconel’s resistance to oxidation and corrosion in harsh environments ensures its longevity and reliability in critical applications.
On the other hand, Hastelloy, a nickel-molybdenum alloy, is prized for its remarkable resistance to corrosion in highly acidic and oxidizing environments. Its unique composition allows it to withstand the aggressive attack of various chemicals, making it ideal for use in chemical processing plants, oil and gas refineries, and pulp and paper mills. Hastelloy’s exceptional corrosion resistance, coupled with its good weldability and fabricability, ensures its versatility in a wide range of industrial applications.
Comparing the two alloys, one must consider the specific requirements of the application. If high-temperature performance is paramount, Inconel might be the better choice. Its ability to retain strength and ductility at extreme temperatures is unparalleled, making it suitable for applications where thermal stress is a concern. On the other hand, if corrosion resistance is the primary concern, Hastelloy would be the preferred option. Its resilience against aggressive chemicals ensures long-term durability in corrosive environments.
However, it is worth noting that the superiority of one alloy over the other is not absolute. The choice often depends on the specific operating conditions, the nature of the corrosive media, and the desired service life of the component. In some cases, a hybrid approach may be adopted, utilizing both Inconel and Hastelloy in different parts of a system to optimize performance and durability.
Furthermore, the cost of materials and processing must also be taken into account. While both Inconel and Hastelloy are relatively expensive due to their specialized alloying elements and manufacturing processes, the cost can vary depending on the specific grade and form of the alloy. Cost-effective substitutions or alloys with similar properties may be considered if budget constraints are a concern.
Conclusion
In conclusion, the debate surrounding the superiority of Inconel or Hastelloy is multifaceted and cannot be resolved with a simple answer. The choice between these two alloys depends on the specific application, operating conditions, corrosion environment, and cost considerations.
Thank you for reading our article and we hope it can help you to find the answer to the question: Which is better Inconel or Hastelloy? If you are looking for Inconel or Hastelloy suppliers and manufacturers online now, we would advise you to visit Huaxiao Alloy.
As a leading supplier of Inconel & Hastelloy suppliers online now, Huaxiao Alloy offers customers high-quality Inconel 600, Inconel 625, Inconel 601, Inconel 718, Hastelloy C22, Hastelloy C276, Hastelloy C2000, and Hastelloy B2 at a very competitive price.